Why is aluminum the metal of choice for modern aerospace engineering
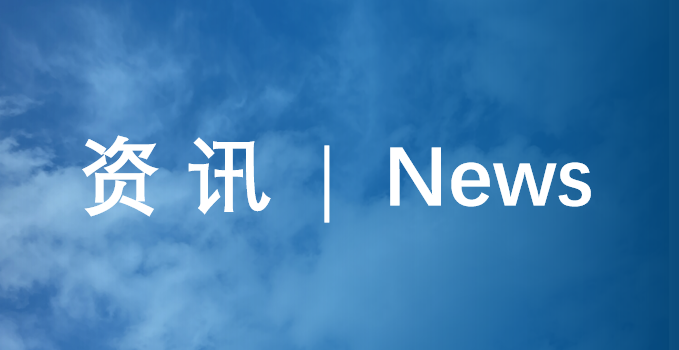
The unique properties of aluminum
Aluminum's appeal in aerospace engineering stems from its unique properties. First and foremost is its strength-to-weight ratio. Aluminum is much lighter than steel, but depending on the alloy used, its strength can be almost equal to that of steel. This lightweight feature is critical for aerospace applications, as weight reduction is directly linked to improved fuel efficiency, payload capacity and overall performance.
Another key characteristic is the corrosion resistance of aluminum. When aluminum is exposed to air, it naturally forms a thin oxide layer that protects it from further oxidation. This makes aluminum ideal for use in environments where it may come into contact with moisture or other corrosive elements, such as saltwater in coastal areas or humid environments at high altitudes. This corrosion resistance is invaluable for aircraft that are often exposed to harsh environments.
Aluminum is also highly malleable and can be shaped into a variety of shapes and structures without compromising its integrity. This feature allows aerospace engineers to design complex components that are both lightweight and robust, improving the aerodynamic efficiency and structural integrity of modern aircraft.
Advances in aluminum alloy technology
The application of aluminum in aerospace has been further enhanced by the development of advanced aluminum alloys. These alloys combine aluminum with other elements such as copper, magnesium and zinc to improve specific properties such as strength, hardness and fatigue resistance.
One of the most significant advances has been the development of aluminum lithium alloy (Al-Li). These alloys offer a higher strength-to-weight ratio than conventional aluminum alloys. By adding lithium, the lightest metal, the overall density of the alloy is reduced, while increasing its rigidity and reducing the growth of fatigue cracks. This makes aluminum-lithium alloys particularly valuable in the production of aircraft fuselage and wing structures, where minimising weight while maximising strength is critical.
Another notable development is the use of composite materials reinforced with aluminum. These composites combine the properties of aluminum with those of other materials such as carbon fiber to create structures that are lighter and stronger than aluminum alone. These composites are increasingly used in the production of aircraft components, such as wing skins and fuselage panels, and their superior properties help improve fuel efficiency and overall aircraft performance.
The unique properties of aluminum
The role of aluminum in modern aircraft design
The unique properties of aluminum and advances in its alloying technology have made it an integral part of modern aircraft design. The airframe, the main structural component of the aircraft, is mainly made of aluminum alloy.
The tensile strength and corrosion resistance of aluminum enable it to withstand the stresses and strains encountered during flight, while its lightweight properties ensure the strength and efficiency of the airframe.
In addition to the body, aluminum is widely used in engine components, including fan blades and heat exchangers, which are often made of aluminum alloys because of their excellent thermal conductivity and high temperature strength. Aluminum also plays a key role in reducing engine weight, which improves fuel efficiency and reduces emissions, in line with the industry's goal of pushing for more environmentally friendly aviation technology.
In addition, aircraft interior components, such as seats, luggage and cabin walls, are often made of aluminum or aluminum alloys. The lightweight nature of aluminum makes the design more comfortable and spacious without compromising aircraft performance or fuel efficiency.
The role of aluminum in the future of aerospace engineering
With the continuous development of the aerospace industry, the role of aluminum is also expanding. Driven by environmental concerns and economic factors, the aviation industry is moving in a more sustainable direction, further cementing aluminum's place in future aircraft designs. For example, in the design of electric and hybrid aircraft, aluminum is widely used due to its lightweight properties to offset the weight of batteries and other powertrains.
In addition, advanced manufacturing technologies being studied, such as 3D printing of aluminum alloys, open up new possibilities for aircraft design and production. These technologies allow the creation of complex lightweight parts that are difficult or impossible to produce through traditional methods. This not only improves the performance of the aircraft, but also reduces manufacturing costs and material waste, contributing to more sustainable production practices.
Challenges and considerations
Although aluminum is crucial in aerospace engineering, it is not without its challenges. One of the main problems is material fatigue, where repeated stresses during flight can cause aluminum components to gradually weaken over time. This requires rigorous monitoring and maintenance to ensure the safety and reliability of the aircraft.
Another consideration is competition from other materials. Composites such as carbon fiber reinforced polymers (CFRP), which offer even greater advantages over aluminum in terms of strength-to-weight ratio, have been increasingly used in aircraft design. However, aluminum's recyclability, lower cost, and mature supply chain ensure that it will remain important in aerospace engineering for the foreseeable future.
conclusion
Aluminum's light weight, strength, corrosion resistance and plasticity, as well as the evolving alloying technology, ensure its central position in aerospace engineering. As the industry moves toward more sustainable and efficient aviation solutions, aluminum will continue to be at the forefront of driving the next generation of aircraft. Despite challenges from other materials, aluminum's versatility and proven track record of use make it an irreplaceable material in the modern aerospace industry.