How Strong is Aluminium Profile?
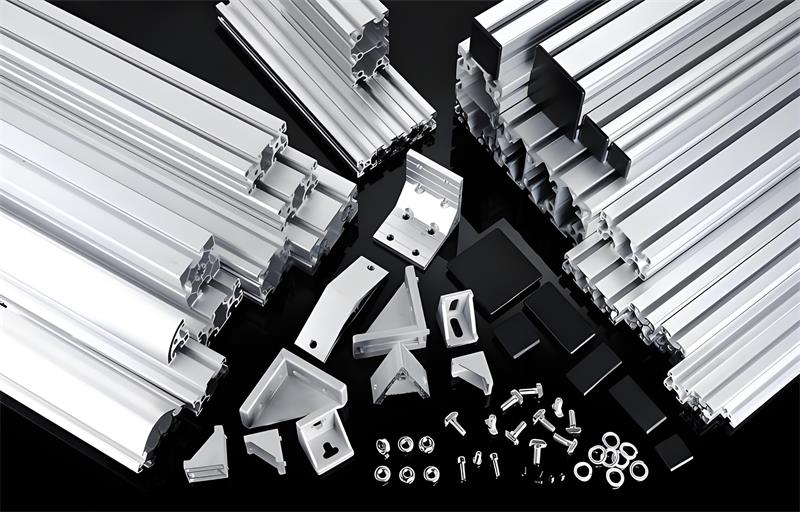
How Strong is Aluminium Profile?
Outline
Introduction
1. Overview of aluminum extrusion profiles
2. Importance of strength in aluminum profiles
3. Why strength matters across various industries
What Are Aluminum Extrusion Profiles?
1. Definition and explanation of aluminum extruded profiles
2. Types of aluminum profiles available
Why Choose Aluminum Extrusion Profiles?
1. Key benefits of aluminum profiles (durability, lightweight, corrosion resistance)
2. Sustainability and recyclability
3. The strength-to-weight ratio advantage
Factors That Affect the Strength of Aluminum Extruded Profiles
1. Alloy composition and selection (6061 vs. 6063)
2. Profile design and thickness
3. Manufacturing and extrusion processes
Comparing the Strength of Aluminum Profiles to Other Materials
1. Aluminum vs. steel
2. Aluminum vs. plastic
3. Aluminum vs. wood
Applications of Aluminum Extrusion Profiles Based on Strength
1. Construction and architecture
2. Automotive industry
3. Industrial machinery
4. Aerospace applications
Surface Finishing Options That Enhance Durability
1. Anodizing for corrosion resistance
2. Powder coating for appearance and protection
3. Mill finish for internal or unseen components
Custom vs. Standard Aluminum Profiles
1. When to opt for custom profiles for strength
2. Cost and performance considerations
Why Aluinno Aluminum Company is a Trusted Supplier
1. The importance of choosing a reliable aluminum profiles manufacturer
2. Aluinno Aluminum’s commitment to quality and strength
Conclusion
1. Recap of the strength and versatility of aluminum extruded profiles
2. Why aluminum profiles are a go-to choice across industries
3. Contacting Aluinno Aluminum
Introduction
When you think about materials that combine durability with versatility, aluminum extrusion profiles stand out as one of the best options. From supporting structures in buildings to the lightweight frames in vehicles, aluminum profiles offer unmatched strength relative to their weight. But how strong are aluminum profiles, and can they handle the stresses your project demands?
Whether you’re working on a new construction project, upgrading automotive components, or developing industrial machinery, aluminum’s strength is a key factor. In this comprehensive guide, we’ll explain how strong aluminum extruded profiles really are, how they compare to other materials, and why they’re a preferred choice in industries worldwide. We’ll also highlight Aluinno Aluminum Company, a trusted manufacturer of top-tier aluminum profiles designed to meet stringent strength requirements.
By the end of this article, you’ll have a complete understanding of how strong aluminum profiles can be, what affects their strength, and how to choose the right profile for your needs.
What Are Aluminum Extrusion Profiles?
Aluminum extrusion profiles are structural components that are made by pushing aluminum through a die, shaping it into a long piece with a consistent cross-section. The extrusion process gives these profiles a wide variety of shapes and sizes, from simple round or rectangular forms to complex custom designs.
Common Types of Aluminum Extruded Profiles
Aluminum profiles are used across many industries, and the variety of shapes reflects the diverse applications. Here are some common types:
· T-slot profiles: These are often used to build frames for machinery, conveyors, and enclosures. Their modular design allows for easy assembly and customization.
· Round and square profiles: Commonly used for structural supports, these profiles can be found in construction, automotive applications, and more.
· L-shaped or U-shaped profiles: These profiles provide structural support and are often used as brackets, trim, or reinforcement elements.
Beyond the standard profiles, custom aluminum profiles can be created to meet specific project needs. Whether you need a lightweight structure or a heavy-duty industrial component, aluminum profiles offer the flexibility to match almost any design requirement.
Why Choose Aluminum Extrusion Profiles?
Aluminum extrusion profiles are widely chosen for a multitude of reasons. Here’s why they continue to dominate industries from construction to aerospace:
1. Durability and Strength
Aluminum is naturally resistant to corrosion. When exposed to the elements, an oxide layer forms on the surface, protecting it from further damage. This corrosion resistance is especially important in industries like construction and marine engineering, where materials are regularly exposed to moisture and harsh weather conditions.
Aluminum extrusion profiles are also strong enough to be used in structural applications. Their strength-to-weight ratio is particularly beneficial in projects that require both durability and minimal mass, such as in the automotive or aerospace industries.
2. Lightweight Advantage
Aluminum's lightweight nature is a significant advantage in many industries. For example, reducing the weight of a vehicle's frame can improve fuel efficiency, while maintaining strength for safety. In construction, using lightweight materials like aluminum can make buildings easier to assemble and reduce load-bearing requirements, without compromising on stability or longevity.
3. Sustainability and Recyclability
Aluminum is one of the most eco-friendly materials available. It’s 100% recyclable, meaning it can be reused without losing any of its properties. Recycling aluminum takes only 5% of the energy required to produce new aluminum, making it an excellent option for industries looking to reduce their environmental footprint.
4. Strength-to-Weight Ratio
One of the primary reasons aluminum extrusion profiles are preferred is their exceptional strength-to-weight ratio. Aluminum offers about a third of the weight of steel while still providing impressive strength. This property is particularly beneficial in applications where reducing weight is crucial, such as in transportation and aerospace.
Aluinno Aluminum specializes in producing high-quality aluminum profiles that meet specific strength and weight requirements, making them a trusted partner for industries that depend on this balance.
Factors That Affect the Strength of Aluminum Extruded Profiles
When it comes to aluminum extruded profiles, several factors influence their strength. Let’s dive deeper into these factors to understand how they contribute to the overall performance of the material:
1. Alloy Composition
Different alloys provide different levels of strength, and the choice of alloy can significantly affect the performance of an aluminum profile. The two most common alloys used in aluminum profiles are 6061 and 6063.
6061 Alloy: Known for its high tensile strength and excellent corrosion resistance, 6061 is often used in structural applications. It can be heat-treated to further improve its mechanical properties, making it ideal for load-bearing applications like bridge components or heavy-duty machine parts.
6063 Alloy: Known as the “architectural alloy,” 6063 provides a smoother surface finish while still offering adequate strength. It’s often used for window frames, door frames, and other aesthetic architectural applications. While it’s not as strong as 6061, it’s still highly durable and perfect for projects where appearance is critical.
2. Profile Design and Thickness
The shape and thickness of an aluminum profile have a direct impact on its strength. Profiles with thicker walls are naturally stronger and more capable of bearing loads than thinner profiles. Similarly, designs with added support elements, such as ribs or flanges, provide extra rigidity.
For example, T-slot aluminum extrusion profiles are often used in industrial machinery because their design allows for added reinforcement at critical points, improving their strength while keeping them lightweight.
3. Manufacturing and Extrusion Process
The extrusion process itself can also influence the strength of the aluminum profile. When aluminum is pushed through a die at high temperatures, its grain structure is altered, which affects its mechanical properties. Manufacturers like Aluinno Aluminum carefully control the extrusion process to ensure that the aluminum profiles have the desired strength and durability.
After extrusion, some aluminum profiles undergo heat treatment to enhance their strength even further. This process can make a significant difference in how well the profile performs under stress.
Comparing the Strength of Aluminum Profiles to Other Materials
How does the strength of aluminum extruded profiles stack up against other common materials like steel, plastic, and wood? Let’s take a closer look:
1. Aluminum vs. Steel
Steel is often considered the benchmark for strength, especially in heavy-duty applications. However, steel is significantly heavier than aluminum. While steel may provide greater strength in certain applications, aluminum’s superior strength-to-weight ratio makes it a more efficient choice in industries where weight reduction is essential, such as in automotive manufacturing and aerospace.
For example, in car manufacturing, switching from steel to aluminum for body panels and frames can dramatically reduce the vehicle’s weight, leading to better fuel efficiency without compromising safety.
2. Aluminum vs. Plastic
Plastic is lighter and less expensive than aluminum, but it falls short when it comes to strength and durability. Plastic components may work well for short-term or lightweight applications, but they’re prone to warping, cracking, and degradation over time. On the other hand, aluminum extrusion profiles provide long-lasting strength and resistance to environmental factors like UV exposure, moisture, and extreme temperatures.
3. Aluminum vs. Wood
Wood is still used in construction and furniture manufacturing, but it requires a lot of maintenance. Wood can rot, warp, and lose strength when exposed to moisture or insects. Aluminum extruded profiles, in contrast, do not suffer from these problems and can maintain their strength and shape over long periods, even in challenging environments. Furthermore, aluminum can be finished to mimic the look of wood, offering an aesthetic solution without sacrificing durability.
Applications of Aluminum Extrusion Profiles Based on Strength
Aluminum extrusion profiles are found in numerous industries because of their strength and versatility. Here are some key applications where strength plays a crucial role:
1. Construction and Architecture
In construction, aluminum extrusion profiles are widely used for structural and decorative purposes. They can be found in window and door frames, curtain walls, railings, and more. Their lightweight nature makes them easy to transport and install, while their strength ensures the structural integrity of buildings, even in areas prone to extreme weather conditions.
2. Automotive Industry
The automotive industry is constantly seeking ways to reduce vehicle weight to improve fuel efficiency. Aluminum profiles are increasingly replacing steel in vehicle frames, body panels, and decorative trims. The ability to maintain strength while reducing weight helps automakers design cars that are both energy-efficient and safe.
3. Industrial Machinery
In industrial settings, aluminum extrusion profiles are used to build machine frames, conveyors, workstations, and structural supports. Their modular nature makes them perfect for building custom solutions, and their strength ensures they can handle the rigors of heavy machinery operation. T-slot aluminum extrusion profiles are particularly popular because they can be easily assembled and reconfigured.
4. Aerospace Applications
In the aerospace industry, where weight reduction is critical, aluminum extruded profiles are used in everything from aircraft fuselage components to interior structures. The strength-to-weight ratio of aluminum makes it the material of choice for constructing safe, lightweight aircraft that can handle the high stresses of flight.
Surface Finishing Options That Enhance Durability
Aluminum extruded profiles are strong, but adding the right surface finish can make them even more durable, especially in environments where they are exposed to harsh conditions. Here are some common finishing options:
1. Anodizing
Anodizing increases the thickness of the oxide layer on the surface of the aluminum, enhancing its corrosion resistance. This process also allows the aluminum to be colored, providing both functional and aesthetic benefits. Anodized aluminum is often used in architectural applications where appearance and durability are equally important.
2. Powder Coating
Powder coating involves applying a dry powder to the surface of the aluminum profile and then baking it to form a durable, attractive finish. This method is ideal for applications where the aluminum will be exposed to the elements, as the coating provides extra protection against UV rays, moisture, and corrosion. Powder-coated profiles can be found in outdoor furniture, building exteriors, and automotive components.
3. Mill Finish
Mill finish is the natural, unprocessed finish of aluminum as it comes out of the extrusion process. While it’s less polished than anodized or powder-coated finishes, it’s suitable for internal or hidden components where appearance isn’t a priority. Mill finish aluminum is often used in industrial applications where the profile’s functionality is more important than its look.
Custom vs. Standard Aluminum Profiles
When choosing aluminum extruded profiles for your project, you’ll need to decide whether to go with standard profiles or opt for a custom solution. Here’s what to consider:
When to Choose Custom Profiles
Custom profiles are the way to go when your project requires unique shapes, sizes, or enhanced strength. With custom profiles, you can specify the exact dimensions, alloy composition, and finishing options needed to meet your performance requirements. Custom profiles are often used in specialized industrial machinery, aerospace components, and high-end architectural designs.
Cost and Performance Considerations
While custom profiles can be more expensive than standard profiles due to the additional design and manufacturing steps involved, the performance benefits often outweigh the cost, particularly in applications where strength and durability are critical. Aluinno Aluminum offers both standard and custom profiles, helping customers find the right solution for their specific needs.
Why Aluinno Aluminum Company is a Trusted Supplier
Choosing the right aluminum supplier is essential to ensuring that your profiles meet the required strength and quality standards. Aluinno Aluminum Company has built a reputation as a reliable provider of high-quality aluminum extrusion profiles for various industries. Their commitment to quality, innovation, and customer satisfaction makes them a trusted partner for projects that demand strong, durable aluminum profiles.
Aluinno Aluminum offers a wide range of profiles, from standard options to fully customized solutions, ensuring that your project’s strength requirements are met without compromising on quality.
Conclusion
Aluminum extruded profiles offer a unique combination of strength, lightweight construction, and versatility. Whether you’re working in construction, automotive, industrial manufacturing, or aerospace, aluminum profiles provide the strength needed to withstand heavy loads, harsh environments, and constant wear.
By understanding factors like alloy composition, profile design, and the extrusion process, you can choose the perfect aluminum profile for your project. And when it comes to finding a reliable supplier, Aluinno Aluminum Company delivers the high-quality, strong aluminum profiles you need to ensure long-lasting performance.
Ready to find strong, durable aluminum profiles for your next project? Contact Aluinno Aluminum Company today for expert advice and a wide selection of high-quality aluminum extrusion profiles. Whether you need standard or custom profiles, we’re here to help you achieve the perfect balance of strength, weight, and durability.