What is the process of profile extrusion?
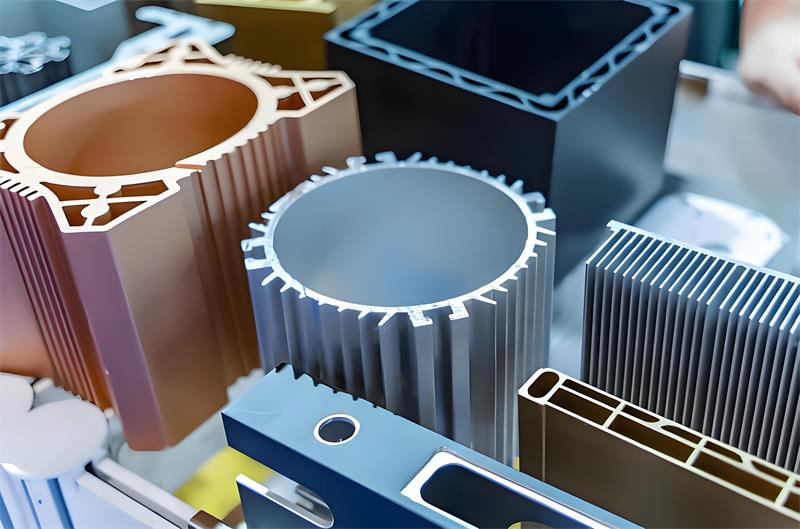
1、Introduction
Aluminium, owing to its distinctive attributes, has emerged as a fundamental material across a multitude of industries. In the following discourse, we shall conduct an in - depth exploration into the production procedures of aluminium extrusion profiles and acquaint you with Aluinno Aluminum Profile Co., Ltd.
2、Aluinno Aluminum Profile Co., Ltd
(1) Company Profile
Aluinno Aluminum Profile Co., Ltd is a preeminent entity within the aluminium manufacturing sector. It has garnered a reputation for its unwavering dedication to quality and its penchant for innovation. The company's operations are underpinned by a robust quality management system and a team of highly - skilled professionals. Through continuous research and development initiatives, it has been able to maintain a competitive edge in the market, offering products that meet and exceed industry standards.
(2) Product Portfolio
The company's product portfolio encompasses a comprehensive and diverse range of aluminium extrusion profiles. Foremost among these is the highly - 6063 6061 6082 aluminium profile and special profile 7005 7075. This alloy, with its excellent formability and remarkable corrosion - resistance properties, is widely utilized in various applications. The catalogue further includes aluminum window and door profiles. These products not only enhance the structural integrity of architectural edifices but also contribute to their aesthetic allure. The aluminum tube profile is ubiquitously employed in a gamut of mechanical and structural assemblies due to its versatility and strength - to - weight ratio.
Aluminum heatsink extrusion profiles play a crucial role in the efficient thermal management of electronic apparatuses. Their design and material properties are optimized to ensure maximum heat dissipation. T - slot aluminum extrusions and v - slot aluminum profiles present remarkable versatility, finding extensive utility in modular and do - it - yourself (DIY) undertakings. These profiles offer ease of assembly and customization, enabling the creation of complex structures.
Aluminum balustrade profiles confer an air of refinement and security to balconies and staircases. Their design adheres to strict safety standards while maintaining an aesthetically pleasing appearance. Aluminum sunroom and pergola profiles are engineered to create captivating outdoor living environs. These profiles are designed to withstand environmental factors while providing a comfortable and stylish space.
3、The Production Process of Aluminium Extrusion Profiles
(1)Melting and Casting
· Ingredient Selection and Preparation: The production of aluminium extrusion profiles commences with a meticulous selection of raw materials. The choice of alloying elements is based on the desired properties of the final product. For instance, in the case of the 6063 aluminium profile, precise proportions of magnesium and silicon are added to the aluminium base. These elements are carefully weighed and mixed in accordance with the strict specifications of the alloy composition.
· Melting Procedure:The prepared mixture is then introduced into a high - temperature furnace. The melting process is carefully monitored to ensure a homogeneous melt. The temperature is maintained within a specific range to prevent over - heating or under - melting. This is crucial as it affects the quality of the subsequent casting process.
· Refining and Casting: After melting, the liquid aluminium undergoes a refining process to remove impurities such as oxides and non - metallic inclusions. This is achieved through the use of various refining agents and techniques. Once refined, the molten aluminium is cast into billets or other pre - determined shapes. The casting process requires precise control of temperature, flow rate, and other parameters to ensure the formation of high - quality semi - finished products.
(2)Extrusion
· Die Design: A fundamental aspect of the extrusion process is the design of the die. The die is custom - designed based on the specific geometry of the desired aluminium extrusion profile. Advanced computer - aided design (CAD) software is often employed to create a precise and optimized die shape. The die design takes into account factors such as the flow characteristics of the aluminium during extrusion and the desired dimensional accuracy of the final product.
· Extrusion Press Operation: The pre - heated aluminium billet is placed in the extrusion press and forced through the die. The extrusion pressure is carefully controlled to ensure a smooth and consistent flow of the material. The speed of extrusion also plays a vital role, as it affects the surface quality and dimensional stability of the extruded profile. During extrusion, the aluminium undergoes plastic deformation, taking on the shape of the die cavity.
(3) Heat Treatment
· Necessity of Heat Treatment: Certain aluminium extrusion profiles require heat treatment to enhance their mechanical properties. Heat treatment is a critical step in the production process as it can significantly improve the strength, hardness, and other mechanical characteristics of the material. For example, in the case of profiles used in load - bearing applications, heat treatment is essential to ensure their structural integrity.
· Quenching and Aging Processes: The heat treatment process typically involves quenching and artificial aging. Quenching involves rapid cooling of the extruded profile from a high temperature to room temperature. This rapid cooling creates a supersaturated solid solution of alloying elements in the aluminium matrix. Subsequently, the profile is subjected to artificial aging, during which the alloying elements precipitate out, strengthening the material.
(4) Surface Treatment
· Anodizing: Anodizing is a widely - used surface treatment method for aluminium extrusion profiles. It involves the formation of an oxide layer on the surface of the aluminium through an electrochemical process. This oxide layer not only enhances the corrosion - resistance of the profile but also provides a base for further surface finishing. The thickness and quality of the anodized layer can be controlled through the adjustment of process parameters such as voltage, current density, and electrolyte composition.
· Powder Coating: Powder coating is another popular surface treatment option. It involves the application of a dry powder coating material to the surface of the aluminium profile. The powder is electrostatically charged and then sprayed onto the surface, where it adheres due to the electrostatic attraction. The coated profile is then cured in an oven, during which the powder melts and forms a continuous, durable film. This film provides excellent protection against corrosion and abrasion and also offers a wide range of color options.
· Electrostatic Powder Spraying: Electrostatic powder spraying is similar to powder coating in principle. However, it may involve different equipment and process parameters. This method also provides good adhesion and a smooth surface finish. The choice between powder coating and electrostatic powder spraying depends on factors such as the specific requirements of the product, production volume, and cost - effectiveness.
(5)Finishing Processes
· Machining: Machining operations are often required to achieve the final dimensions and tolerances of the aluminium extrusion profiles. This may involve processes such as cutting, drilling, milling, and turning. Precision machining is essential to ensure that the profiles meet the exact specifications of the end - use applications. Advanced machining tools and techniques are employed to achieve high - quality surface finishes and accurate dimensions.
· Packaging: Packaging is the final step in the production process of aluminium extrusion profiles. The profiles are carefully packaged to protect them from damage during transportation and storage. The packaging materials and methods are selected based on the size, shape, and quantity of the profiles. Adequate cushioning and protection are provided to prevent scratches, dents, and other forms of damage.
4、Applications of Aluminium Extrusion Profiles
(1)Construction Industry
· Windows and Doors: Aluminium profiles used in windows and doors offer a multitude of advantages. Their high - strength - to - weight ratio enables the production of large - sized and lightweight structures. The excellent corrosion - resistance properties ensure a long service life, even in harsh environmental conditions. Additionally, aluminium profiles can be easily fabricated into complex shapes, allowing for the design of aesthetically - pleasing and energy - efficient windows and doors.
· Curtain Walls: Curtain walls constructed using aluminium extrusion profiles provide a modern and sleek appearance to buildings. These profiles offer excellent thermal and acoustic insulation, contributing to the energy - efficiency and comfort of the interior spaces. The modular nature of aluminium curtain wall systems allows for easy installation and customization, making them a popular choice in modern architecture.
· Balustrades and Pergolas: Aluminium balustrade profiles are designed to meet strict safety standards while adding an element of elegance to balconies and staircases. Their corrosion - resistance and low - maintenance characteristics make them an ideal choice for outdoor applications. Aluminium pergola profiles, on the other hand, are used to create outdoor structures that provide shade and a pleasant living space. These profiles can be designed to withstand various weather conditions and can be customized to match the architectural style of the building.
(2) Automotive Industry
· Lightweight Components: The use of aluminium extrusion profiles in the automotive industry is driven by the need for lightweighting. These profiles are used to manufacture components such as chassis parts, body frames, and interior trims. The reduction in vehicle weight achieved through the use of aluminium components leads to improved fuel efficiency and reduced emissions. Additionally, the excellent formability of aluminium allows for the production of complex - shaped components with high - strength requirements.
· Heat Sinks: Aluminium heatsink extrusion profiles play a critical role in the cooling systems of automotive electronics. These profiles are designed to efficiently dissipate heat generated by electronic components such as engine control units and power electronics. The high thermal conductivity of aluminium, combined with its ability to be extruded into complex shapes, makes it an ideal material for heat sink applications.
(3) Electrical and Electronic Industry
· Enclosures for Electrical Equipment: Aluminium extrusion profiles are widely used to manufacture enclosures for electrical equipment such as control panels, distribution boxes, and communication equipment. These profiles provide a strong and durable housing that protects the internal components from mechanical damage, electromagnetic interference, and environmental factors. The ease of customization and assembly of aluminium profiles also enables the production of enclosures with specific dimensions and configurations.
· Heat Sinks for Electronic Components: In the electronic industry, heat dissipation is a crucial concern. Aluminium heatsink extrusion profiles are designed to effectively remove heat from electronic components such as microprocessors, power transistors, and integrated circuits. The design of these profiles takes into account factors such as heat transfer area, air flow, and thermal resistance to ensure efficient cooling.
5、Conclusion
Aluminium extrusion profiles occupy a pivotal position in diverse industries. Aluinno Aluminum Profile Co., Ltd is resolutely committed to proffering premium - grade products and avant - garde solutions. Through a profound comprehension of the production process and applications, one can more fully fathom the ubiquity and profound significance of aluminium in contemporary society. The company's continuous efforts in research and development, quality control, and customer service ensure that its products remain at the forefront of the aluminium extrusion profile market, catering to the evolving needs of various industries. Future research and innovation in the field of aluminium extrusion profiles are expected to further expand their applications and improve their performance, strengthening the role of aluminium as a key material in modern manufacturing.