what is aluminum oxide used for
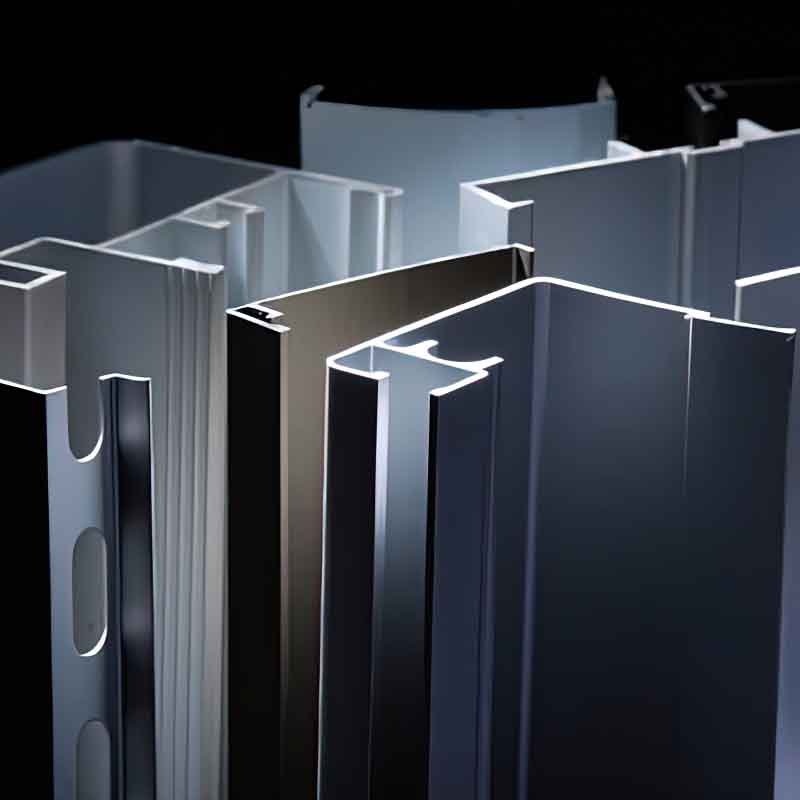
I. Introduction
A. Hook: Briefly mention the prevalence of aluminum products and the hidden role of aluminum oxide.
B. Thesis statement: Explore the significance and applications of aluminum oxide in the aluminum industry.
II. Aluminum Oxide Basics
A. Definition and chemical formula
B. Common crystal structures and their characteristics
III. Properties of Aluminum Oxide
A. High hardness and its implications
B. Melting point and thermal stability
C. Chemical resistance properties
IV. Applications in Aluminum Profiles
A. In extrusion processes
V. Role in Aluminium Casement Windows
A. Durability enhancement
VI. Use in Industrial Aluminium Profiles
A. In machinery and equipment
VII. Other Applications
A. In aluminum casting
VIII. Conclusion
A. Recap of key points
B. Future prospects and importance of continued research
Introduction
Aluminum oxide, also known as alumina, is a chemical compound that holds significant importance in various industries, especially those related to aluminum products such as aluminum profiles, extrusion aluminium, custom aluminum, aluminium casement windows, and industrial aluminium profiles. Its unique properties make it an essential component in the production and functionality of these items. In this blog post, we will delve into the diverse applications of aluminum oxide, exploring how it contributes to the quality, durability, and performance of aluminum - related products.
Aluminum oxide is not just a simple compound; it is a key player in enhancing the characteristics of aluminum materials. For instance, in the manufacturing of aluminum profiles, which are widely used in construction, automotive, and industrial applications, aluminum oxide plays a crucial role in determining the profile's strength, corrosion resistance, and surface finish. Extrusion aluminium, a process that creates various shapes of aluminum products, also benefits from the properties of aluminum oxide. The compound helps in achieving better formability during extrusion and improves the final product's properties.
Custom aluminum products, designed to meet specific requirements, often rely on aluminum oxide to ensure that they can withstand the demands of their intended use. Aluminium casement windows, popular for their energy - efficiency and aesthetic appeal, utilize aluminum oxide - treated aluminum frames to resist the elements and maintain their appearance over time. Industrial aluminium profiles, which are used in heavy - duty applications such as machinery and infrastructure, need the strength and durability provided by aluminum oxide.
Understanding the uses of aluminum oxide is essential for anyone involved in the aluminum industry, whether it's manufacturers looking to improve their products, architects and designers seeking the best materials for their projects, or consumers interested in making informed choices about the aluminum products they purchase. So, let's explore the many ways aluminum oxide is used and how it impacts our daily lives.
Aluminum Oxide Basics
Definition and Structure
Aluminum oxide, with the chemical formula Al₂O₃, is an inorganic compound that occurs naturally in various forms. It is an ionic compound, consisting of aluminum cations (Al³⁺) and oxygen anions (O²⁻). The strong electrostatic forces between these oppositely charged ions result in a stable and robust structure.
Aluminum oxide exists in multiple crystal structures, each with distinct characteristics. The most common polymorphs are α - Al₂O₃ (alpha - alumina), β - Al₂O₃ (beta - alumina), and γ - Al₂O₃ (gamma - alumina). α - Al₂O₃, also known as corundum, is the most stable form at high temperatures. Its crystal structure features a hexagonal close - packed arrangement of oxygen ions, with aluminum ions occupying specific octahedral and tetrahedral interstitial sites. This compact and ordered structure contributes to its excellent mechanical and chemical properties. For example, in the production of industrial aluminium profiles, the use of α - Al₂O₃ - rich raw materials can enhance the profiles' hardness and wear resistance.
β - Al₂O₃ is a non - stoichiometric compound with a more complex structure. It contains layers of oxygen and aluminum ions separated by mobile cations, such as sodium or potassium. This unique structure gives β - Al₂O₃ certain ionic conductivity properties, making it suitable for applications in solid - state electrolytes in some battery systems.
γ - Al₂O₃ has a metastable structure and is often formed at lower temperatures. It has a higher surface area compared to α - Al₂O₃, which makes it useful in applications where a large surface area is required, such as in catalysts and adsorbents. For instance, in the automotive industry, γ - Al₂O₃ is used as a catalyst support in catalytic converters to help break down harmful exhaust gases.
Properties of Aluminum Oxide
Aluminum oxide exhibits a remarkable set of properties that make it highly valuable in numerous applications. One of its most notable properties is its extreme hardness. With a Mohs hardness of 9, it is only surpassed by diamond. This hardness makes it an ideal material for abrasives and cutting tools. In the manufacturing of aluminum profiles, aluminum oxide - based abrasives are used to finish the surfaces, ensuring a smooth and precise finish. Whether it's for custom aluminum products that require a high - quality appearance or industrial aluminium profiles that need to withstand heavy use, the hardness of aluminum oxide plays a crucial role.
The melting point of aluminum oxide is extremely high, around 2054°C. This high melting point makes it suitable for applications in high - temperature environments. In the production of extrusion aluminium, the high - temperature resistance of aluminum oxide helps maintain the integrity of the extrusion dies, which are subjected to intense heat during the extrusion process. It also enables the use of aluminum oxide in refractory materials, such as those used in furnaces and kilns.
Aluminum oxide is chemically stable and is classified as an amphoteric oxide. This means it can react with both acids and bases. In acidic solutions, it acts as a base, reacting to form aluminum salts and water. For example, when aluminum oxide reacts with hydrochloric acid, it produces aluminum chloride and water. In basic solutions, it behaves as an acid, forming aluminates. This amphoteric nature is exploited in various chemical processes, such as in the extraction of aluminum from bauxite ore.
Furthermore, aluminum oxide has excellent electrical insulating properties. It is a poor conductor of electricity, making it useful in electrical applications where insulation is required. In the production of aluminium casement windows, the aluminum frames can be treated with aluminum oxide coatings to improve their electrical insulation properties, which is important for safety and energy - efficiency.
The high chemical stability of aluminum oxide also makes it resistant to corrosion. This property is highly beneficial for aluminum products, as it helps protect them from environmental degradation. For example, aluminum profiles used in outdoor construction projects are often treated with aluminum oxide - based coatings to prevent rust and corrosion, ensuring their long - term durability.
Aluminum Oxide in Aluminium Casement Windows
Enhancing Durability
Aluminium casement windows are a popular choice for many homeowners due to their energy - efficiency, aesthetic appeal, and functionality. Aluminum oxide plays a crucial role in enhancing the durability of these windows, ensuring they can withstand the test of time and various environmental factors.
One of the primary ways aluminum oxide contributes to durability is by providing excellent corrosion resistance. Aluminium casement windows are often exposed to moisture, rain, and humidity, which can cause corrosion over time. However, the presence of aluminum oxide on the surface of the aluminum frames acts as a protective barrier. When aluminum reacts with oxygen in the air, a thin layer of aluminum oxide forms naturally. This layer is extremely dense and adheres tightly to the aluminum surface. It prevents further oxidation of the underlying aluminum, effectively stopping the corrosion process. For example, in coastal areas where the air is laden with salt - water particles, aluminum oxide - protected casement windows can resist the corrosive effects of salt spray much better than unprotected windows.
Aluminum oxide also enhances the hardness of the aluminum frames. With its high Mohs hardness of 9, aluminum oxide significantly increases the scratch and abrasion resistance of the windows. Daily use, such as opening and closing the casement windows, can cause minor abrasions. In addition, external factors like wind - blown debris can impact the window frames. The hard aluminum oxide layer ensures that the frames maintain their smooth surface and shape, preventing premature wear and tear. This is especially important for custom aluminum casement windows that are designed to meet specific architectural requirements and need to retain their appearance over an extended period.
Furthermore, the presence of aluminum oxide can improve the structural integrity of the windows. It helps the aluminum frames maintain their shape and dimensions, even when subjected to mechanical stress. For instance, in areas prone to strong winds, the windows may experience significant pressure. The aluminum oxide - treated frames are more likely to resist deformation, ensuring the proper functioning of the casement windows. This is crucial for maintaining the energy - efficiency of the windows, as a well - fitting window frame helps prevent air leakage.
Improving Aesthetic Appeal
In addition to enhancing durability, aluminum oxide also plays a significant role in improving the aesthetic appeal of aluminium casement windows. Aluminum oxide coatings can be customized to achieve a wide range of colors and finishes, allowing homeowners and designers to create windows that complement any architectural style.
One common method of applying aluminum oxide to achieve different colors is through anodizing. Anodizing is an electrochemical process that thickens the natural aluminum oxide layer on the surface of the aluminum. During this process, the aluminum is placed in an electrolytic bath, and an electric current is passed through it. This causes the aluminum to react with oxygen in the bath, forming a thicker and more porous aluminum oxide layer. The porous nature of the anodized layer allows for the absorption of dyes, which can be used to achieve various colors. For example, anodized aluminum casement windows can be colored in classic shades like silver, bronze, or black, which are popular choices for modern and contemporary architecture. These colors not only add a touch of elegance but also blend well with different building materials such as glass, stone, and brick.
Another way aluminum oxide contributes to the aesthetic appeal is through the creation of a smooth and lustrous finish. The anodizing process, as well as other surface treatments that involve aluminum oxide, can result in a sleek and shiny surface. This finish not only makes the windows visually appealing but also gives them a high - quality look. The reflective properties of the aluminum oxide - coated surface can also enhance the overall appearance of the building, especially when the windows are exposed to sunlight.
For those who prefer a more natural or understated look, a mill finish with a thin layer of aluminum oxide can be used. A mill finish is the natural, untreated surface of aluminum after the extrusion process, with a thin layer of aluminum oxide already present. This finish gives the windows a raw, industrial - like appearance that can be very appealing in certain architectural styles, such as industrial or minimalist designs. It provides a sense of authenticity and simplicity, while still benefiting from the protective properties of aluminum oxide.
In addition, aluminum oxide - based powder coatings can be used to achieve a wide variety of textures and colors. Powder coating involves applying a dry powder, which contains aluminum oxide and other additives, to the surface of the aluminum. The powder is then cured under heat, forming a durable and attractive finish. Powder coatings can mimic the appearance of wood, stone, or other materials, allowing for a more diverse range of design options. For example, a powder - coated aluminium casement window can be made to look like a wooden window, providing the aesthetic appeal of wood without the maintenance issues associated with it. This is particularly useful for homeowners who want the look of a traditional wooden window but prefer the durability and low - maintenance characteristics of aluminum.
Aluminum Oxide in Industrial Aluminium Profiles
For Machinery and Equipment
In the realm of industrial machinery and equipment, industrial aluminium profiles are the building blocks for creating robust and efficient structures, and aluminum oxide plays a pivotal role in enhancing their performance.
One of the primary applications of aluminum - oxide - treated industrial aluminium profiles is in the construction of machinery frames. These frames need to withstand significant mechanical stress, vibrations, and heavy loads during the operation of the machinery. Aluminum oxide, with its high hardness and excellent wear - resistance properties, helps the profiles maintain their structural integrity over time. For example, in large - scale manufacturing plants, such as automotive assembly lines, the conveyor systems are often supported by industrial aluminium profiles. The constant movement of heavy automotive parts along the conveyor exerts substantial pressure on the supporting profiles. Aluminum oxide - coated profiles can resist the resulting abrasion and deformation, ensuring the smooth and continuous operation of the conveyor system.
In addition to frames, industrial aluminium profiles are used in the production of various mechanical components. For instance, gears and pulleys made from aluminum profiles can be treated with aluminum oxide to improve their surface hardness. This increased hardness reduces the wear and tear that occurs during the meshing of gears or the rotation of pulleys, thus extending their service life. In high - speed machinery, where the components are subjected to rapid movement and friction, the use of aluminum oxide - treated profiles becomes even more crucial. It helps to minimize the energy losses due to friction and reduces the need for frequent maintenance and replacement of parts.
Moreover, aluminum oxide can enhance the corrosion resistance of industrial aluminium profiles in machinery used in harsh environments. In industries such as chemical processing, where the machinery is exposed to corrosive chemicals and moisture, the presence of aluminum oxide on the surface of the profiles acts as a protective barrier. It prevents the aluminium from reacting with the corrosive substances, thereby safeguarding the integrity of the machinery. This is especially important for equipment like pumps, valves, and storage tanks that are made from or supported by industrial aluminium profiles.
In Construction and Infrastructure
Industrial aluminium profiles are extensively used in construction and infrastructure projects, and aluminum oxide significantly contributes to their performance and durability in these applications.
In the construction of industrial buildings, aluminum - oxide - treated industrial aluminium profiles are used for structural support. These profiles can be used to create columns, beams, and trusses that bear the weight of the building and its contents. The high strength - to - weight ratio of aluminum, combined with the enhanced properties provided by aluminum oxide, makes it an ideal choice for such applications. For example, in large - scale warehouses or factory buildings, the use of aluminum oxide - coated industrial aluminium profiles can reduce the overall weight of the structure without sacrificing its strength. This not only simplifies the construction process but also allows for more flexible design options.
Aluminum oxide also plays a crucial role in improving the corrosion resistance of industrial aluminium profiles in outdoor construction and infrastructure projects. Bridges, walkways, and outdoor platforms are often exposed to various environmental factors such as moisture, rain, and temperature fluctuations. Aluminum oxide - treated profiles can withstand these conditions better than untreated profiles. The protective layer of aluminum oxide prevents the formation of rust and corrosion, ensuring the long - term stability and safety of the structures. In coastal areas, where the air contains salt - water particles, the use of aluminum oxide - coated industrial aluminium profiles is particularly beneficial. It helps to prevent the rapid degradation of the profiles that would otherwise occur due to the corrosive effects of salt.
Furthermore, in the construction of infrastructure such as power transmission towers and communication masts, industrial aluminium profiles treated with aluminum oxide are used. These structures need to be strong, lightweight, and resistant to environmental factors. The high hardness and corrosion resistance provided by aluminum oxide enable the profiles to withstand the mechanical stress of supporting heavy electrical equipment and antennas, as well as the harsh weather conditions they are exposed to. This ensures the reliable operation of power transmission and communication systems.
In addition, aluminum oxide can be used to improve the aesthetic appearance of industrial aluminium profiles in construction projects. In modern industrial architecture, there is an increasing emphasis on creating visually appealing structures. Aluminum oxide coatings can be applied in a variety of colors and finishes, allowing for the customization of the profiles to match the overall design of the building or infrastructure. This not only enhances the visual appeal but also adds a touch of professionalism and modernity to the construction.
Conclusion
In conclusion, aluminum oxide is an essential and versatile component in the aluminum industry. It permeates every aspect, from the manufacturing of aluminum profiles for construction, automotive, and industrial applications to the enhancement of the performance and appearance of aluminum products like casement windows. Its ability to improve durability, strength, and aesthetic appeal makes it indispensable. As technology advances and the demand for high-quality aluminum-based materials grows, the role of aluminum oxide will only become more prominent. Manufacturers and engineers must continue to harness its potential to develop innovative and reliable aluminum products, ensuring the continued growth and evolution of the aluminum industry