Aluminum Profile News: Unveiling the Latest Trends and Innovations
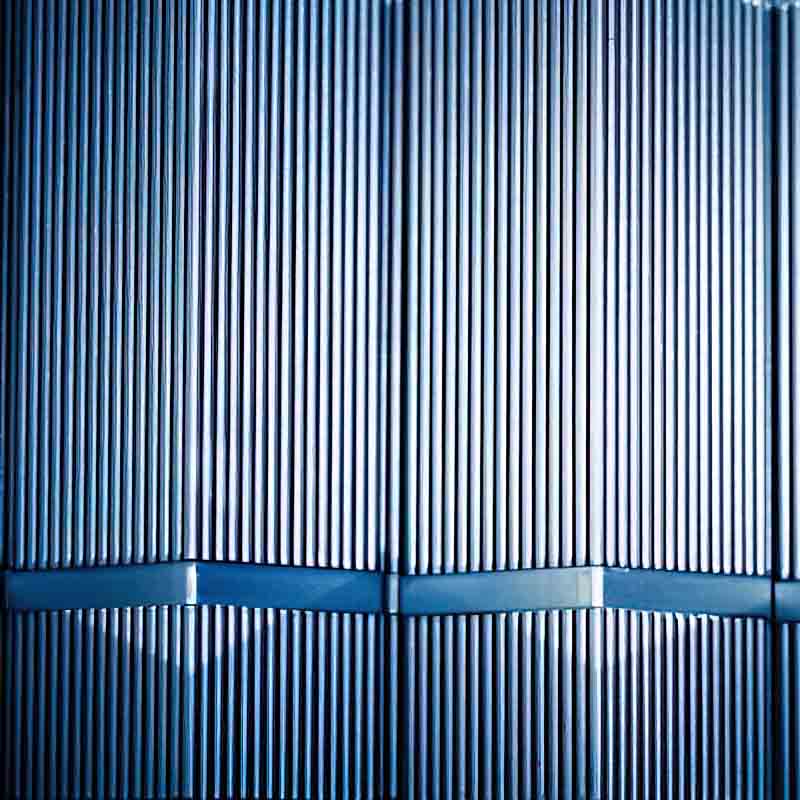
Outline
Introduction:
Introduce the importance of aluminum profiles in modern industries and the purpose of the article.
Overview of Aluminum Profiles:
Explain extruded aluminum profiles' formation and applications.
Describe custom aluminum profiles and Aluinno's role.
Latest Trends:
Technological innovation: Discuss 3D printing, high-precision extrusion, and intelligent production.
Sustainable development: Focus on recycled aluminum use and energy-saving technologies.
Design diversity: Illustrate applications in construction and industry.
Innovative Applications:
Highlight aluminum casement windows and industrial aluminum profiles.
Choosing the Right Profile:
Mention factors to consider and the importance of a reliable supplier like Aluinno.
Conclusion:
Summarize the evolving industry and Aluinno's commitment to meeting customers' needs.
I. Introduction
In modern industries, aluminum profiles have emerged as indispensable materials. Their lightweight, high strength, and excellent corrosion resistance properties have made them a top choice in construction, automotive, aerospace, and numerous other fields. With the continuous advancement of technology and the increasing demand for high-quality materials, the aluminum profile industry is witnessing a wave of new trends and innovations. In this article, we will explore these developments and also introduce how Aluinno Aluminum Company is keeping pace with the times and contributing to this evolving landscape.
II. Overview of Aluminum Profiles
2.1 Extruded Aluminum Profiles
Extruded aluminum profiles are formed by forcing heated aluminum billets through a precisely designed die. This process imparts the aluminum with a specific cross-sectional shape, creating profiles of various geometries. The extrusion method allows for high precision and repeatability, ensuring that each profile meets strict dimensional requirements. These profiles find extensive use in multiple industries due to their ability to provide structural integrity while being lightweight. For example, in the construction of buildings, they are used in window frames, curtain walls, and structural supports, offering durability and ease of installation. In transportation, they contribute to reducing the weight of vehicles, enhancing fuel efficiency without sacrificing safety.
2.2 Custom Aluminum Profiles
Custom aluminum profiles are tailored to meet the unique demands of specific projects. Unlike standard profiles, which come in common shapes and sizes, custom profiles can be designed to fit complex and specialized applications. Aluinno Aluminum Company specializes in providing custom aluminum solutions. Our team of experienced engineers works closely with clients to understand their exact requirements. Whether it's a particular shape needed for an innovative architectural design or a specific strength and dimension for a high-performance industrial component, we can manufacture custom aluminum profiles with precision. This flexibility gives our customers a competitive edge in their respective industries, enabling them to achieve their design goals and improve product performance.
III Technological innovation
3.1.1 advanced manufacturing process
In recent years, the aluminum profile industry has witnessed remarkable advancements in manufacturing processes, with 3D printing and high - precision extrusion technology leading the charge.
3D printing, also known as additive manufacturing, has emerged as a revolutionary technology in the production of aluminum profiles. This technology allows for the creation of highly complex and customized aluminum components with unprecedented precision. By layering aluminum materials in a controlled manner based on digital models, 3D printing enables the production of parts that were previously difficult or impossible to manufacture using traditional methods. For example, in the aerospace industry, 3D - printed aluminum components can be designed to have intricate internal structures that optimize strength - to - weight ratios. This not only reduces the weight of aircraft parts but also enhances their performance and functionality.
High - precision extrusion technology has also made significant strides. Modern extrusion equipment is equipped with advanced control systems that can precisely regulate parameters such as temperature, pressure, and speed during the extrusion process. This level of precision ensures that the extruded aluminum profiles have consistent dimensions and excellent surface quality. For instance, in the production of aluminum profiles for high - end electronics, where tight tolerances are crucial, high - precision extrusion technology can meet the strict requirements. The ability to produce profiles with extremely accurate dimensions allows for better integration of components, improving the overall performance and reliability of electronic devices.
Moreover, high - precision extrusion technology can also produce profiles with complex cross - sectional shapes. This opens up new possibilities for designers and engineers, enabling them to create innovative products that were previously limited by the capabilities of traditional extrusion methods. In the automotive industry, for example, complex - shaped aluminum profiles can be used to design more aerodynamic and lightweight vehicle frames, contributing to improved fuel efficiency and driving performance.
3.1.2 intelligent production
The integration of automation and digital management systems has transformed the aluminum profile production landscape, bringing about substantial improvements in efficiency and quality.
Automation has become a cornerstone of modern aluminum profile manufacturing. Robots and automated machinery are increasingly being employed in various stages of the production process, from raw material handling to the final assembly of products. In the extrusion process, automated systems can precisely load and unload aluminum billets, adjust the extrusion equipment, and monitor the process in real - time. This not only reduces the need for manual labor but also minimizes human - error, ensuring a more consistent and reliable production output. For example, in a large - scale aluminum profile factory, automated robotic arms can quickly and accurately move aluminum billets into the extrusion press, significantly reducing the time required for material handling and increasing the overall production speed.
Digital management systems play a crucial role in optimizing production processes. These systems utilize advanced software and sensors to collect and analyze data from every aspect of the production line. By monitoring variables such as temperature, pressure, and production rates in real - time, manufacturers can identify potential issues before they escalate into major problems. For instance, if a digital management system detects a slight deviation in the temperature of the extrusion process, it can automatically adjust the heating system to maintain the optimal temperature, preventing the production of defective profiles.
Furthermore, digital management systems enable better inventory control. By tracking the quantity and location of raw materials, semi - finished products, and finished goods, manufacturers can streamline their supply chains and reduce waste. This level of precision in inventory management ensures that production is not interrupted due to shortages of materials, while also preventing overstocking, which ties up valuable capital.
In addition, the use of artificial intelligence (AI) and machine learning algorithms in digital management systems is becoming more prevalent. These technologies can analyze large volumes of production data to identify patterns and trends, allowing manufacturers to make data - driven decisions. For example, AI can predict equipment maintenance needs based on historical data, enabling proactive maintenance and reducing unplanned downtime. This not only improves the overall efficiency of the production line but also extends the lifespan of the manufacturing equipment.
3.2 Sustainable development
3.2.1 use of recycled aluminum
The utilization of recycled aluminum has become an increasingly prominent trend in the aluminum profile industry, driven by growing environmental awareness and the need for sustainable resource management.
Recycled aluminum, also known as secondary aluminum, is produced from scrap aluminum materials. The process of recycling aluminum requires significantly less energy compared to primary aluminum production, which involves extracting aluminum from bauxite ore through electrolysis. According to industry data, recycling aluminum can save up to 95% of the energy required to produce primary aluminum. This substantial energy savings not only reduces the carbon footprint of the aluminum industry but also helps in conserving valuable natural resources.
In recent years, the use of recycled aluminum in the production of aluminum profiles has been on the rise. Many aluminum profile manufacturers, including aluinno, are increasingly incorporating recycled aluminum into their product lines. For example, in the construction industry, aluminum profiles made from recycled aluminum are being used for window frames, curtain walls, and structural components. These recycled aluminum profiles offer the same high - quality performance and durability as profiles made from primary aluminum, while also contributing to environmental sustainability.
The use of recycled aluminum also has economic benefits. As the demand for sustainable products grows, aluminum profiles made from recycled materials are becoming more market - competitive. By using recycled aluminum, manufacturers can reduce their production costs, as recycled materials are often more cost - effective than primary aluminum. This cost advantage can be passed on to consumers, making sustainable aluminum profile products more affordable.
Furthermore, the increased use of recycled aluminum helps to close the loop in the aluminum lifecycle. Instead of ending up in landfills, scrap aluminum is recycled and transformed into new products, reducing waste and conserving resources. This circular economy approach is essential for the long - term sustainability of the aluminum industry.
3.2.2 energy saving technology
The aluminum profile industry is actively embracing energy - saving technologies and equipment to reduce its environmental impact and operational costs.
One of the key areas where energy - saving technologies are being applied is in the melting and casting processes. Traditional melting furnaces often consume large amounts of energy. However, modern melting technologies, such as induction melting, are more energy - efficient. Induction melting uses electromagnetic fields to heat the aluminum, resulting in faster and more uniform heating. This not only reduces energy consumption but also improves the quality of the molten aluminum. For example, some aluminum profile manufacturers have reported a significant reduction in energy usage after switching to induction melting furnaces.
In the extrusion process, energy - saving measures are also being implemented. High - efficiency extrusion presses are designed to consume less energy while maintaining high production rates. These presses are equipped with advanced hydraulic systems and motors that are optimized for energy efficiency. Additionally, the use of insulation materials in the extrusion equipment helps to reduce heat loss, further conserving energy.
Another energy - saving technology gaining popularity is waste heat recovery. During the aluminum production process, a significant amount of heat is generated as a by - product. Waste heat recovery systems capture this heat and use it for other purposes, such as pre - heating raw materials or heating the factory premises. This not only reduces the need for additional energy sources but also improves the overall energy efficiency of the production process.
In addition to these technologies, the use of energy - efficient lighting systems and variable - speed drives in aluminum profile factories is becoming more common. Energy - efficient lighting, such as LED lights, consumes less electricity compared to traditional lighting sources. Variable - speed drives can adjust the speed of motors based on the actual load requirements, reducing energy consumption during periods of low demand.
3.3 Design diversity
3.3.1 Construction
In the construction industry, aluminum profiles have become a preferred choice for architects and designers due to their versatility and aesthetic appeal. Their use in building design has led to the creation of some truly remarkable and innovative structures.
One such example is the Burj Khalifa, the world's tallest building. Aluminum profiles were extensively used in its construction, particularly in the curtain wall system. The curtain wall, which consists of aluminum - framed glass panels, not only provides a stunning visual appearance but also offers excellent thermal insulation and weather resistance. The use of aluminum profiles in the Burj Khalifa allowed for the creation of a lightweight yet sturdy structure that could withstand the harsh environmental conditions at such heights. The sleek and modern design of the aluminum - framed curtain wall has made the Burj Khalifa an iconic symbol of contemporary architecture.
Another notable example is the Sydney Opera House. While the building's iconic shell - like structures are primarily made of concrete, aluminum profiles play a crucial role in its interior and exterior finishes. Aluminum was used for the construction of window frames, door frames, and decorative elements. The use of aluminum profiles added a touch of elegance and durability to the building, complementing its unique architectural design. The corrosion resistance of aluminum ensures that these components remain in excellent condition despite the building's exposure to the salt - laden air of Sydney Harbour.
In modern sustainable building designs, aluminum profiles are being used in innovative ways to enhance energy efficiency. For instance, in green buildings, aluminum - framed windows with low - emissivity glass are commonly used. These windows can effectively reduce heat transfer, keeping the building cool in summer and warm in winter. Additionally, aluminum profiles are used in the construction of solar panel mounts. Their lightweight nature and corrosion resistance make them ideal for supporting solar panels, which are an essential component of renewable energy systems in buildings.
3.3.2 industry
In the industrial sector, aluminum profiles are playing an increasingly important role in the design and construction of machinery and automated equipment. Their unique properties make them well - suited for a variety of industrial applications.
In the manufacturing of automated production lines, aluminum profiles are used to create lightweight and modular frameworks. These frameworks provide a stable and durable structure for mounting various components, such as conveyor belts, robotic arms, and sensors. The lightweight nature of aluminum reduces the overall weight of the equipment, making it easier to move and reconfigure. For example, in a food processing factory, an automated conveyor system made with aluminum profiles can be easily adjusted to accommodate different production requirements. The modular design of aluminum profiles allows for quick and easy assembly and disassembly, enabling efficient maintenance and upgrades of the production line.
In the field of robotics, aluminum profiles are used to construct the bodies and joints of robots. Their high strength - to - weight ratio ensures that the robots are both lightweight and strong, allowing for faster and more precise movements. Additionally, the corrosion resistance of aluminum is beneficial in environments where robots may be exposed to moisture or chemicals. For instance, in a pharmaceutical manufacturing plant, robots made with aluminum profiles can operate in cleanroom environments without the risk of corrosion, ensuring the integrity of the production process.
Aluminum profiles are also being used in the design of industrial enclosures. These enclosures protect sensitive equipment from dust, moisture, and other environmental factors. The use of aluminum profiles in enclosures provides a combination of strength and aesthetic appeal. They can be customized to fit specific equipment sizes and shapes, and their surface can be finished in various ways to meet different design requirements. For example, in an electronics manufacturing facility, aluminum - framed enclosures with powder - coated finishes not only protect the electronic components but also give the equipment a professional and modern look.
IV. Innovative Applications of Aluminum Profiles
4.1 Aluminum Casement Windows
Aluminum casement windows have seen significant innovations in recent years. The frames are now designed with enhanced strength and better sealing properties, improving energy efficiency and weather resistance. The use of high-quality aluminum alloys and advanced manufacturing techniques ensures that the windows can withstand strong winds and heavy rain while maintaining a smooth operation. Aluinno Aluminum Company's aluminum casement windows are available in a variety of styles and finishes, allowing customers to choose the ones that best suit their architectural designs and functional requirements.
4.2 Industrial Aluminum Profiles
Industrial aluminum profiles are widely used in machinery manufacturing, robotics, and material handling systems. They offer lightweight yet sturdy structures, facilitating the movement and assembly of components. In the automotive industry, for example, aluminum profiles are used in the construction of car frames and body parts, reducing vehicle weight and improving fuel economy. In the aerospace sector, high-strength aluminum profiles are crucial for the construction of aircraft wings and fuselages, meeting the strict requirements of weight reduction and structural integrity. Aluinno provides a diverse range of industrial aluminum profiles, customized to the specific needs of different industries, ensuring optimal performance and reliability.
V. Choosing the Right Aluminum Profile
5.1 Consideration Factors
When selecting an aluminum profile for a project, several factors need to be taken into account. Firstly, the strength requirements must be carefully evaluated. Depending on the application, whether it's a load-bearing structure or a non-structural component, the appropriate alloy and profile shape should be chosen to ensure sufficient strength. Secondly, corrosion resistance is a crucial factor, especially in outdoor or harsh chemical environments. Profiles with proper surface treatments such as anodizing or powder coating should be considered. Thirdly, the size and shape of the profile should fit the specific installation space and design requirements. Standard profiles may be suitable for common applications, but for more complex projects, custom profiles might be necessary.
5.2 Collaboration with Suppliers
Working with a reliable aluminum profile supplier is essential. A good supplier like Aluinno Aluminum Company can provide not only high-quality products but also professional technical support and advice. We have a team of experts who can help customers analyze their project needs and recommend the most suitable aluminum profiles. Additionally, we offer customization services, ensuring that the profiles meet the exact specifications of the project. Our commitment to quality and customer satisfaction makes us a trusted partner in the aluminum profile market.
VI. Conclusion
The aluminum profile industry is constantly evolving, driven by technological innovations and the pursuit of sustainable development. The latest trends in manufacturing processes, design, and application are opening up new possibilities for various industries. By understanding these trends and choosing the right aluminum profiles, businesses can enhance the performance and competitiveness of their products. Aluinno Aluminum Company will continue to stay at the forefront of the industry, providing high-quality aluminum profiles and innovative solutions to meet the diverse needs of our customers. Whether it's for construction, automotive, aerospace, or other applications, we are dedicated to helping our clients achieve success with our advanced aluminum products and services.