Aluminum Industry's Bright Future in the EV Revolution
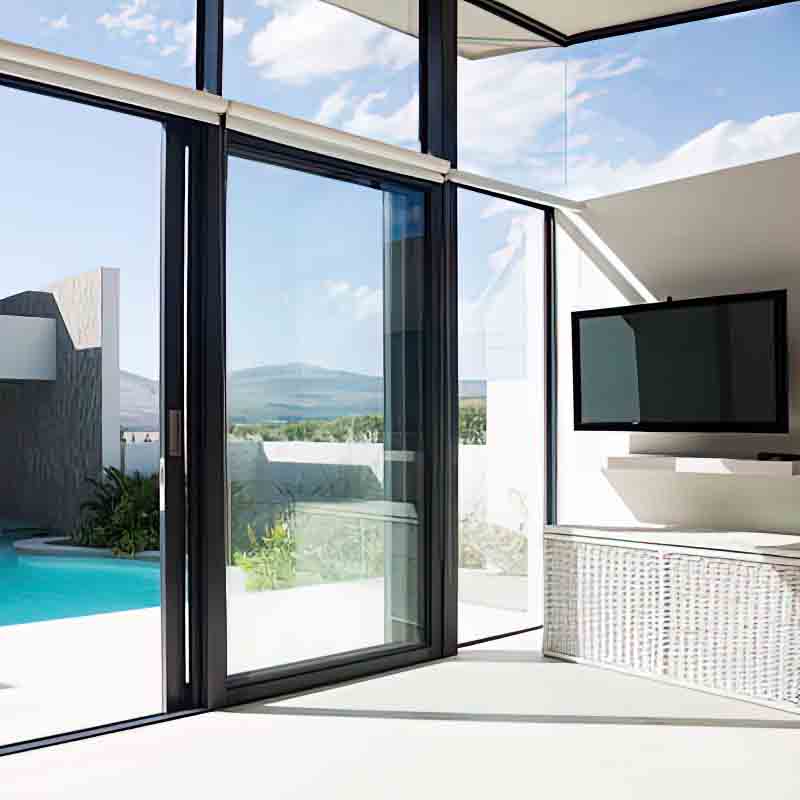
I. Introduction
Ⅰ. Introduction
1.1 The Surging EV Tide and Its Global Impact
The electric vehicle (EV) market has been booming in recent years, driven by factors such as environmental concerns, government incentives, and technological advancements. This growth has been nothing short of remarkable, with sales figures skyrocketing globally. Governments worldwide are imposing stricter emission regulations, pushing automakers to accelerate the transition to electric mobility. This has led to a flurry of activity in the EV sector, with new models being introduced regularly and production capacities expanding rapidly. The shift towards EVs is not only changing the way we commute but also has a profound impact on various industries, and the aluminum industry is at the forefront of this transformation.
1.2 The Pivotal Role of Aluminum in This Transformation
Aluminum has become an essential material in the EV revolution due to its unique combination of properties. Its low density makes it significantly lighter than traditional materials like steel, enabling EVs to reduce weight and improve energy efficiency. This weight reduction directly translates into increased driving range, a crucial factor for the widespread adoption of EVs. Additionally, aluminum's excellent corrosion resistance ensures the durability of vehicle components, even in challenging environmental conditions. Its recyclability further enhances its appeal, as it aligns with the sustainability goals of the automotive industry.
Ⅱ. Aluminum: An Ideal Material for EVs
2.1 The Superior Properties of Aluminum
2.1.1 Lightweight Advantage
Aluminum's density is about one-third that of steel. This characteristic allows EV manufacturers to achieve substantial weight savings when using aluminum in components such as the body structure, chassis, and battery enclosure. For example, replacing steel parts with aluminum in an EV can reduce the vehicle's weight by hundreds of kilograms, resulting in improved acceleration, better handling, and a longer driving range. In some cases, a 30% reduction in weight can lead to a 15% increase in range, making aluminum an attractive option for enhancing EV performance.
2.1.2 Corrosion Resistance
When exposed to air, aluminum forms a thin oxide layer on its surface, which acts as a natural barrier against corrosion. This self-protecting property makes aluminum highly resistant to rust and degradation, even in the presence of moisture, salt, and other corrosive substances commonly encountered on roads. In EVs, this corrosion resistance ensures that components maintain their structural integrity and functionality over the vehicle's lifespan, reducing maintenance costs and enhancing reliability.
2.1.3 Recyclability
Aluminum is highly recyclable, and recycling it requires only a fraction of the energy needed to produce new aluminum from bauxite ore. At the end of an EV's life cycle, aluminum components can be easily collected and recycled into new products with the same quality and properties. This closed-loop recycling process not only conserves natural resources but also reduces the environmental impact associated with aluminum production. It also helps to stabilize the supply of aluminum for the EV industry, making it a sustainable choice for the long term.
2.2 Cost - effectiveness and Abundant Resources
While the initial cost of aluminum may be higher than some other materials in certain applications, its long-term cost-effectiveness in EVs is significant. The weight reduction achieved by using aluminum leads to lower energy consumption during the vehicle's operation, which can offset the higher material cost over time. Moreover, aluminum is the most abundant metal in the Earth's crust, ensuring a reliable and abundant supply for the growing EV market. With continuous improvements in extraction and production technologies, the cost of aluminum is expected to become even more competitive in the future.
Ⅲ. Aluminum Profiles in EV Manufacturing
3.1 The Significance of Aluminum Profiles
3.1.1 Structural Integrity and Design Flexibilit
Aluminum profiles play a crucial role in maintaining the structural integrity of EVs. They can be customized into various shapes and sizes to meet the specific design requirements of different vehicle components. Whether it's the frame that provides the backbone of the vehicle or the intricate supports for the battery system, aluminum profiles offer the necessary strength and rigidity. Their flexibility in design allows engineers to optimize the vehicle's structure for better performance and safety while also enabling creative and aesthetically pleasing designs.
3.1.2 Contribution to Vehicle Performance
The use of aluminum profiles in EVs contributes significantly to overall vehicle performance. In addition to weight reduction, they enhance the vehicle's safety by effectively absorbing and dissipating energy during collisions. Their high thermal conductivity is also beneficial for the thermal management of the battery and other components, ensuring stable operation and prolonging their lifespan. This, in turn, improves the reliability and efficiency of the EV.
3.2 Types of Aluminum Profiles in EVs
3.2.1 Extrusion Aluminium
Extrusion is a commonly used method for producing aluminum profiles for EVs. In this process, heated aluminum billets are forced through a die to create the desired shape. Extrusion aluminum profiles are widely used in key EV components such as the body frame and battery tray. They can be manufactured with high precision and complex cross-sections, providing excellent strength-to-weight ratios. For example, the body frame made from extrusion aluminum profiles can withstand heavy loads while keeping the vehicle lightweight, enhancing both performance and safety.
3.2.2 Custom Aluminum
To meet the unique and specific needs of EVs, custom aluminum profiles are often required. These profiles are designed and manufactured to fit precisely into specialized applications. For instance, in some high-performance EVs, custom aluminum profiles are used in the battery enclosure to optimize space utilization and ensure maximum protection for the battery cells. They can also be found in unique interior and exterior components, adding a touch of individuality to the vehicle's design.
3.2.3 Industrial Aluminium Profile
Industrial aluminum profiles are essential for the efficient production of EVs. They are standardized and produced in large quantities, facilitating the assembly process. Commonly used in manufacturing equipment such as robotic arms and conveyor systems, they ensure smooth production operations. Their modular design allows for easy installation and disassembly, making them highly adaptable to different production setups.
Ⅳ. Aluminum's Application in Different EV Components
4.1 Body Structure
4.1.1 Using Aluminum Profiles for Frame Construction
In the body structure of EVs, aluminum profiles are widely utilized to construct the frame. The frame provides support and protection for the vehicle occupants and other components. By using aluminum profiles, the frame can achieve a high strength-to-weight ratio. Advanced manufacturing techniques enable the production of frames with complex geometries that are optimized for strength and stiffness. This not only reduces the vehicle's weight but also improves its handling and crash safety.
4.1.2 Advantages in Crash Safety and Energy Absorption
During a collision, the aluminum frame of an EV plays a critical role in ensuring occupant safety. Aluminum has excellent energy absorption capabilities, which means it can effectively dissipate the impact energy. This helps to reduce the force transmitted to the cabin, protecting the passengers. Compared to traditional steel frames, aluminum frames can provide better protection while being lighter, making them an ideal choice for modern EVs.
4.2 Battery Systems
4.2.1 Aluminum in Battery Housing
The battery is the heart of an EV, and its safety and performance are of utmost importance. Aluminum is widely used in battery housing due to its lightweight, corrosion-resistant, and good thermal conductivity properties. The battery housing made of aluminum provides a reliable enclosure for the battery cells, protecting them from external impacts and environmental factors. It also helps in heat dissipation, maintaining the optimal operating temperature of the battery, which is crucial for its efficiency and lifespan.
4.2.2 Heat Dissipation and Thermal Management
Efficient heat dissipation is essential for the performance and longevity of the battery. Aluminum's high thermal conductivity allows it to transfer heat quickly away from the battery cells. In the battery's thermal management system, aluminum heat sinks and cooling channels are commonly used to regulate the temperature. By keeping the battery at an appropriate temperature, its performance can be maximized, and the risk of overheating and degradation can be minimized.
4.3 Interior and Exterior Components
4.3.1 Interior Trim and Cabin Comfort
Aluminum profiles are also used in the interior of EVs to enhance the aesthetic and comfort of the cabin. They can be found in components such as door handles, instrument panel supports, and seat frames. The sleek and modern appearance of aluminum adds a touch of luxury to the interior. Moreover, its lightweight nature does not add excessive weight to the vehicle, contributing to better energy efficiency. Additionally, the use of aluminum in seat frames can provide better support and comfort for the occupants.
4.3.2 Exterior Styling and Aerodynamics
In the exterior design of EVs, aluminum profiles contribute to both the styling and aerodynamics of the vehicle. They can be used to create unique body lines and contours, giving the vehicle a distinctive and modern look. At the same time, the smooth surface of aluminum and its ability to be shaped into streamlined forms help to improve the vehicle's aerodynamic performance. By reducing air resistance, the energy consumption of the vehicle during driving can be further decreased, thereby increasing the driving range.
Ⅴ. The Market Landscape of Aluminum in the EV Industry
5.1 Current Market Trends
5.1.1 Increasing Demand for Aluminum in EV Production
The rapid growth of the EV market has led to a significant increase in the demand for aluminum in the automotive industry. According to industry data, the amount of aluminum used in each EV has been steadily rising. In some advanced models, the aluminum content can account for up to 30% of the vehicle's weight. This trend is expected to continue as EV manufacturers strive to improve vehicle performance through weight reduction. The increasing demand for aluminum has also spurred the growth of the aluminum industry, with many producers focusing on developing products tailored for the EV market.
5.1.2 Expansion of Aluminum Suppliers in the EV Supply Chain
To meet the growing demand for aluminum in the EV industry, numerous aluminum suppliers are expanding their production capacities and strengthening their positions in the supply chain. They are investing in new technologies and equipment to improve production efficiency and product quality. Some suppliers are also forging strategic partnerships with EV manufacturers to ensure a stable supply of aluminum and to jointly develop new applications. This collaboration between the two industries is driving innovation and growth.
5.2 Future Projections
5.2.1 Estimated Growth in Aluminum Consumption for EVs
Looking ahead, the consumption of aluminum in the EV industry is projected to experience substantial growth. With the continuous expansion of the EV market and the increasing penetration rate of EVs, the demand for aluminum will continue to soar. Industry experts predict that by 2030, the global demand for aluminum in the EV sector could double or even triple compared to current levels. This growth will have a significant impact on the aluminum industry and the broader economy.
5.2.2 Technological Innovations and Their Influence on the Market
The development of new technologies in the aluminum industry is expected to have a profound impact on the EV market. For example, the research and development of new aluminum alloys with enhanced properties will enable the production of more advanced aluminum profiles for EVs. These alloys could offer higher strength, better formability, and improved corrosion resistance, further enhancing the performance of EVs. Additionally, advancements in manufacturing technologies such as 3D printing and advanced extrusion techniques will allow for more complex and customized aluminum components to be produced, providing greater design flexibility for EV manufacturers.
Ⅵ. Challenges and Solutions in the Aluminum - EV Nexus
6.1 Challenges
6.1.1 High - end Manufacturing Technology Requirements
The application of aluminum in EVs demands high-end manufacturing technologies to ensure the quality and performance of components. Producing high-precision aluminum profiles with complex shapes requires advanced extrusion equipment and precise control of the manufacturing process. Moreover, the joining and assembly of aluminum components pose challenges, as traditional welding methods may not be suitable. Special joining techniques like friction stir welding and self-piercing riveting need to be further developed and optimized.
6.1.2 Cost - Efficiency in Production
Although aluminum offers many advantages in EVs, the cost of production and processing remains a concern. To make aluminum more competitive in the EV market, efforts are needed to reduce production costs while maintaining product quality. This involves continuous improvement of production technologies, optimization of the production process, and reduction of energy consumption. Enhancing the recycling and reuse of aluminum is also crucial to lower the overall cost.
6.2 Solutions
6.2.1 R & D Investment and Technological Upgrades
To address the challenges, increased investment in research and development is essential. The aluminum industry should focus on developing new manufacturing technologies and materials. For instance, investing in advanced extrusion processes and new aluminum alloys can improve product quality and reduce costs. Collaboration between academia, research institutions, and industry players can accelerate technological innovation.
6.2.2 Industry Collaboration and Optimization of the Supply Chain
Closer collaboration between the aluminum and EV industries is necessary. Aluminum suppliers should work closely with EV manufacturers to understand their requirements and develop customized solutions. This includes joint product development, quality control, and supply chain optimization. By streamlining the supply chain and reducing intermediate links, the cost of aluminum products can be effectively reduced.
Ⅶ. Aluinno: Shining in the EV - Aluminum Realm
7.1 Company Introduction
Aluinno is a renowned company in the aluminum industry, dedicated to providing high-quality aluminum profiles. With a wealth of experience and a team of skilled professionals, it has established a solid reputation in the market. The company is committed to serving the EV industry with innovative and sustainable aluminum solutions.
7.2 Product Portfolio for EVs
7.2.1 High - quality Aluminum Profiles
Aluinno offers a diverse range of aluminum profiles for EVs, including extrusion aluminum and custom aluminum profiles. These are manufactured using state-of-the-art technologies and premium raw materials, ensuring excellent mechanical properties and surface finishes. The profiles are available in various shapes and sizes, suitable for different EV applications such as body frames, battery trays, and interior components.
7.2.2 Custom - tailored Solutions
Understanding the unique needs of the EV market, Aluinno provides comprehensive custom-tailored services. Its experienced engineers collaborate closely with customers from the design stage to production, ensuring that the aluminum profiles meet specific requirements. Whether it's a complex shape or a special performance need, Aluinno can deliver a satisfactory solution.
7.3 Competitive Edge
7.3.1 Advanced Manufacturing Capabilities
Aluinno is equipped with advanced manufacturing facilities and cutting-edge production technologies. Its extrusion lines can produce high-precision aluminum profiles with intricate cross-sections. The use of advanced control systems ensures stable and consistent production processes. Strict quality control measures are in place, from raw material inspection to final product testing, guaranteeing the quality of each profile.
7.3.2 Professional Technical Support and Service
In addition to top-quality products, Aluinno offers professional technical support and excellent customer service. Its technical team has in-depth knowledge of aluminum and EV applications, providing valuable advice on product selection and design optimization. The responsive customer service department ensures that any customer issues are promptly addressed, ensuring a smooth cooperation experience.
Ⅷ. Conclusion
8.1 Recap of Aluminum's Promising Future in the EV Boom
In summary, the EV boom has presented the aluminum industry with significant opportunities. Aluminum's properties make it indispensable in EVs, and its applications in various components enhance vehicle performance and sustainability. The growing demand and technological advancements promise a bright future for both industries.
8.2 Call to Action for Collaboration and Innovation
To fully capitalize on these opportunities, continued collaboration and innovation among all stakeholders are crucial. Aluinno stands ready to contribute with its high-quality products and services, inviting partners to join in driving the growth of the EV-aluminum sector.