Corrosion Resistance in Harsh Environments: Why Aluminum Profiles Outperform Steel
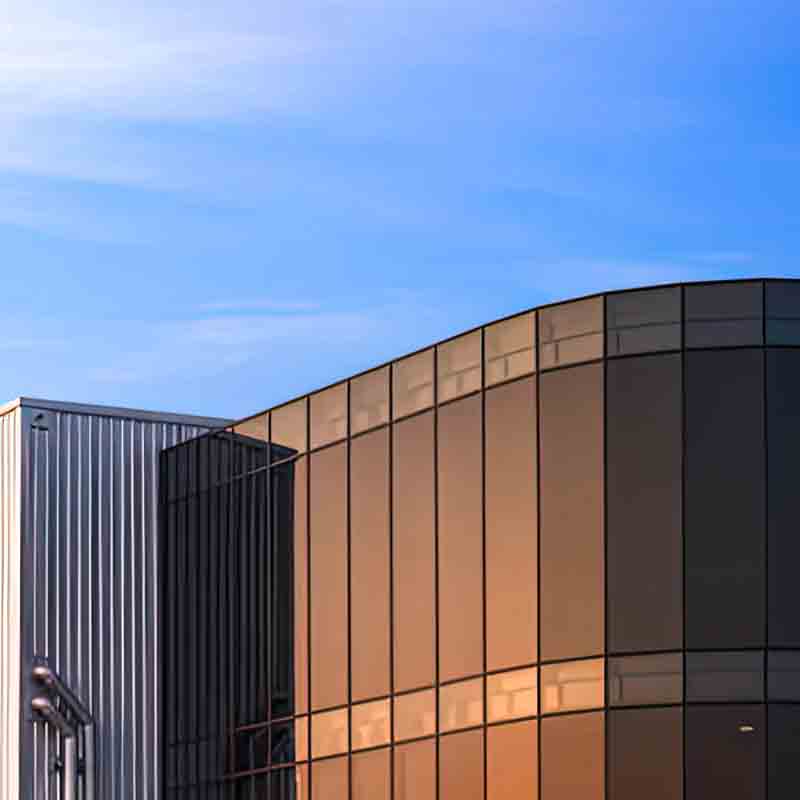
1 Introduction
1.1 Setting the Stage
In the vast spectrum of materials used across industries, aluminum and steel stand out as two of the most widely utilized. However, when it comes to withstanding the onslaught of harsh environments, a distinct difference emerges. Consider coastal areas where the air is thick with salt-laden moisture, or industrial zones filled with acidic fumes and chemical pollutants. These environments can be extremely unforgiving to materials, causing rapid degradation and structural failure. It is in such settings that the remarkable corrosion resistance of aluminum profiles truly shines, outperforming their steel counterparts in ways that have far - reaching implications for various applications.
1.2 Significance of the Topic
In the construction industry, the integrity of building materials is crucial for the safety and longevity of structures. Corrosion can lead to weakened frameworks, compromised load - bearing capacities, and costly repairs. In industrial applications, equipment made from corroded materials may malfunction, leading to production delays and financial losses. In the automotive and aerospace sectors, where weight and durability are equally important, corrosion can pose serious threats to performance and safety. Thus, understanding why aluminum profiles are more corrosion - resistant than steel is not just an academic exercise but a matter of practical importance for industries worldwide.
1.3 Thesis Statement
This article delves deep into the scientific and practical aspects of why aluminum profiles demonstrate superior corrosion resistance in harsh environments compared to steel. By examining the chemical and physical properties of both materials, as well as real - world applications and case studies, we aim to provide a comprehensive understanding of this crucial material advantage.
2 Understanding Corrosion
2.1 Definition and Types of Corrosion
Corrosion is the gradual destruction of a material, usually a metal, by chemical or electrochemical reactions with its environment. There are several types of corrosion, each with its own characteristics and mechanisms. Uniform corrosion is the most common type, where the metal surface is uniformly attacked, resulting in a general thinning of the material. Pitting corrosion occurs when small, localized areas of the metal surface are preferentially attacked, forming pits. This type of corrosion can be particularly dangerous as it can lead to sudden failures, even when the overall material thickness seems to be only slightly affected. Stress - corrosion cracking is another serious form of corrosion that occurs when a metal is under tensile stress in a corrosive environment. The combination of stress and corrosion can cause cracks to form and propagate, ultimately leading to catastrophic failure.
2.2 How Corrosion Occurs
At its core, corrosion is an electrochemical process. Metals, in their pure form, have a tendency to return to their more stable, oxidized states. For example, when iron (Fe) is exposed to oxygen (O₂) and water (H₂O), a series of chemical reactions take place. First, iron atoms lose electrons and become iron ions (Fe²⁺), a process called oxidation. The electrons released during oxidation react with oxygen and water to form hydroxide ions (OH⁻). The iron ions then react with the hydroxide ions to form iron hydroxide (Fe(OH)₂), which further oxidizes to form the familiar rust, iron(III) oxide (Fe₂O₃). This process is accelerated in the presence of electrolytes, such as salts in seawater or acids in industrial environments.
2.3 Impact of Corrosion in Different Industries
In the construction industry, corrosion of steel reinforcement bars in concrete can lead to the expansion of the corroded areas, causing cracks in the concrete and ultimately weakening the entire structure. In the automotive industry, corrosion can affect the body panels, chassis components, and engine parts, reducing the vehicle's lifespan and safety. In the aerospace industry, where every component must be highly reliable, corrosion can compromise the structural integrity of aircraft, leading to potential flight - safety issues.
3 Aluminum Profiles: An Overview
3.1 What are Aluminum Profiles
Aluminum profiles are extruded shapes made from aluminum alloys. The extrusion process involves forcing a heated billet of aluminum through a die with a specific cross - sectional shape. This allows for the production of a wide variety of profiles with complex geometries, such as those used in aluminium casement windows, aluminum extrusion tubes, and aluminium handrail profiles. Aluminum profiles can be customized to meet specific requirements in terms of strength, dimensional accuracy, and surface finish.
3.2 Properties of Aluminum
Aluminum is a lightweight metal with a density of about one - third that of steel. It has a high strength - to - weight ratio, making it an ideal choice for applications where weight reduction is crucial, such as in the aerospace and automotive industries. Aluminum also has excellent thermal and electrical conductivity, which makes it useful in applications like heat sinks and electrical wiring. Additionally, aluminum is non - magnetic and has good formability, allowing it to be easily shaped into various profiles.
3.3 Common Applications of Aluminum Profiles
In the construction industry, aluminum profiles are widely used in the manufacture of windows, doors, curtain walls, and structural components. The use of aluminum in aluminium casement windows not only provides a sleek and modern look but also offers good insulation properties and durability. In the industrial sector, aluminum extrusion tubes are used in heat exchangers, fluid transfer systems, and as structural members in machinery. In the decorative and architectural fields, aluminium handrail profiles are popular for their aesthetic appeal and corrosion resistance, making them suitable for both indoor and outdoor applications.
4 Steel Profiles: A Comparison
4.1 What are Steel Profiles
Steel profiles are made from iron alloyed with carbon and other elements, such as manganese, silicon, and chromium. The carbon content in steel can vary, with low - carbon steel containing less than 0.3% carbon, medium - carbon steel having 0.3% - 0.6% carbon, and high - carbon steel containing more than 0.6% carbon. Steel profiles can be produced through various processes, including rolling, forging, and casting, and come in a wide range of shapes, such as I - beams, channels, and angles.
4.2 Properties of Steel
Steel is known for its high strength and toughness. It can withstand large tensile, compressive, and shear forces, making it suitable for use in load - bearing structures. However, steel is relatively heavy compared to aluminum, which can be a drawback in applications where weight is a concern. Steel also has good magnetic properties, which are useful in electrical applications such as transformers and motors.
4.3 Common Applications of Steel Profiles
Steel profiles are extensively used in the construction of buildings, bridges, and industrial plants. In the automotive industry, steel is used in the manufacture of chassis, body panels, and engine components. In the manufacturing sector, steel is used to make machinery, tools, and equipment due to its high strength and wear resistance.
5 Why Aluminum Profiles Outperform Steel in Corrosion Resistance
5.1 The Natural Oxide Layer of Aluminum
One of the key reasons for aluminum's superior corrosion resistance is the formation of a natural oxide layer on its surface. When aluminum is exposed to air, a thin layer of aluminum oxide (Al₂O₃) immediately forms. This oxide layer is extremely thin, typically only a few nanometers thick, but it is highly dense and adherent to the underlying aluminum surface. The oxide layer acts as a barrier, preventing further oxidation of the aluminum by blocking the access of oxygen and moisture to the metal surface. In contrast, when steel corrodes, the iron oxide (rust) that forms is porous and flaky. This porous rust layer does not effectively protect the underlying steel from further corrosion, allowing oxygen and water to penetrate and continue the corrosion process.
5.2 Alloying Elements in Aluminum
Aluminum alloys often contain alloying elements such as magnesium, silicon, copper, and zinc. These alloying elements can significantly improve the corrosion resistance of aluminum. For example, magnesium - containing aluminum alloys are known for their good corrosion resistance in marine environments. Magnesium helps to enhance the stability of the oxide layer and also promotes the formation of a more protective surface film. Silicon can improve the strength and corrosion resistance of aluminum alloys, especially in applications where the alloy is exposed to high - temperature and corrosive environments. Copper and zinc are added to some aluminum alloys to improve their mechanical properties, and they also contribute to the overall corrosion resistance of the alloy to a certain extent.
5.3 Surface Finishes for Aluminum
Aluminum profiles can be further protected from corrosion by applying various surface finishes. Anodizing is a popular surface treatment method for aluminum. During anodizing, an aluminum profile is immersed in an electrolyte solution and an electric current is passed through it. This causes the formation of a thick, porous oxide layer on the aluminum surface. The porous oxide layer can then be sealed with a variety of substances, such as water or organic sealants, to improve its corrosion resistance and durability. Powder coating is another common surface finish for aluminum. In powder coating, a dry powder of polymer resin is electrostatically applied to the aluminum surface and then cured in an oven. The powder coating forms a hard, durable, and corrosion - resistant film on the aluminum surface. These surface finishes not only enhance the corrosion resistance of aluminum profiles but also provide additional benefits such as improved aesthetics and increased wear resistance.
5.4 Case Studies and Real - world Examples
There are numerous real - world examples that demonstrate the superior corrosion resistance of aluminum profiles. In coastal areas, many buildings and structures use aluminum for their exterior components, such as window frames and handrails. For instance, in a coastal town in Florida, USA, a condominium complex was built with aluminium casement windows made of aluminum profiles. After 20 years of exposure to the salty sea air, the aluminum windows showed only minor signs of surface discoloration, while neighboring buildings with steel - framed windows had severe rusting and structural damage. In an industrial chemical plant in Germany, aluminum extrusion tubes were used in a corrosive liquid transfer system. Over a period of 10 years, the aluminum tubes remained in good condition, while the initially installed steel tubes had to be replaced multiple times due to corrosion.
6 Cost Considerations
6.1 Initial Material Costs
It is true that the initial cost of aluminum profiles is generally higher than that of steel profiles. This is due to several factors, including the cost of aluminum extraction and processing, as well as the relatively higher cost of alloying elements used in aluminum alloys. However, the cost difference is not always as significant as it may seem, especially when considering the overall life - cycle cost of a project.
6.2 Long - term Cost Savings with Aluminum
When looking at the long - term, aluminum's superior corrosion resistance can result in substantial cost savings. Steel structures require more frequent maintenance and repairs due to corrosion. This includes activities such as painting, rust removal, and replacement of corroded components. In contrast, aluminum structures require minimal maintenance over their lifespan. For example, a bridge made of steel may need to be repainted every 5 - 10 years at a significant cost, while an aluminum - alloy bridge may only require occasional inspections and minor touch - ups over a much longer period. In the long run, the reduced maintenance and replacement costs associated with aluminum can offset its higher initial cost.
7 aluinno: Your Trusted Aluminum Profile Partner
7.1 Company Introduction
aluinno is a leading aluminum profile manufacturer with a rich history and a reputation for excellence. With state - of - the - art production facilities and a team of highly skilled professionals, aluinno has been at the forefront of the aluminum profile industry for many years. The company is committed to providing high - quality products and exceptional customer service.
7.2 Product Range
aluinno offers a wide range of aluminum profiles, including those for aluminium casement windows, aluminum extrusion tubes, and aluminium handrail profiles. Each product is carefully designed and manufactured to meet the highest standards of quality and performance. The company also provides customization services, allowing customers to tailor the aluminum profiles to their specific needs.
7.3 Quality Assurance and Customer Service
aluinno has a strict quality control system in place to ensure that every aluminum profile leaving the factory meets the required specifications. From the selection of raw materials to the final inspection of the finished products, every step of the production process is closely monitored. In addition, aluinno's customer service team is always ready to assist customers with any questions or concerns, providing timely and professional support.
8 Conclusion
8.1 Recap of Key Points
In summary, aluminum profiles outperform steel in corrosion resistance in harsh environments due to several factors. The natural oxide layer on aluminum provides an effective barrier against corrosion, while the rust layer on steel is porous and ineffective. Alloying elements in aluminum alloys further enhance their corrosion resistance, and various surface finishes can be applied to aluminum profiles to provide additional protection. Real - world examples and case studies have demonstrated the long - term durability of aluminum in corrosive environments, and the long - term cost savings associated with aluminum's corrosion resistance can offset its higher initial cost.
8.2 Final Thoughts and Future Outlook
As industries continue to seek materials that can withstand harsh environments while maintaining performance and cost - effectiveness, aluminum profiles are likely to see even more widespread use. With ongoing research and development in aluminum alloy technology and surface treatment methods, the corrosion resistance of aluminum profiles is expected to improve further. aluinno, with its commitment to quality and innovation, will continue to play a significant role in providing high - quality aluminum profiles to meet the evolving needs of various industries.