The “New Three Types” of China’s Aluminum Processing Industry - Part 2 Lithium battery
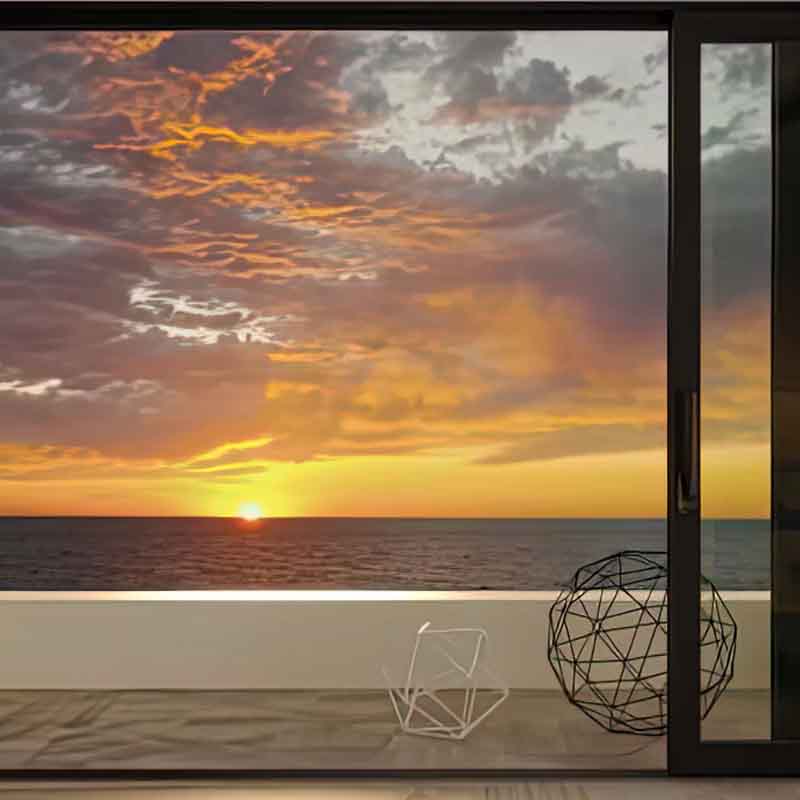
Article Outline
This article commences with a brief recap of the “new three types” in the aluminum processing industry: new energy vehicles, lithium batteries, and solar photovoltaics. It then delves into the specific role of aluminum profiles in lithium batteries. We will explore how aluminum is utilized in different components of lithium batteries, like electrodes and casings, due to its unique properties. The manufacturing processes and quality control aspects related to aluminum in lithium battery production will be discussed. Additionally, challenges faced in this application, such as material compatibility and cost management, will be analyzed, along with potential solutions. Towards the end, we will glance at future trends and conclude by highlighting our company, aluinno's contribution to the sector.
1. Introduction
The aluminum processing industry has witnessed a paradigm shift with the rise of the “new three types”. Among them, lithium batteries have emerged as a critical power source, not only for new energy vehicles but also for various energy storage applications. Aluminum, with its remarkable properties, has found extensive use in lithium battery manufacturing, playing a vital role in enhancing battery performance and durability.
2. The “New Three Types” Revisited
2.1 New Energy Vehicles
As mentioned before, new energy vehicles are revolutionizing the transportation sector. They rely heavily on lithium batteries for power and aluminum profiles for structural components, creating a synergy that drives the demand for both materials.
2.2 Lithium Batteries
Lithium batteries have become the go-to energy storage solution due to their high energy density, long cycle life, and relatively low self-discharge rate. Their production requires precise engineering and the right choice of materials, where aluminum plays multiple crucial roles.
2.3 Solar Photovoltaics
Solar photovoltaics harness sunlight to generate electricity. Aluminum profiles are used in solar panel frames and mounting systems, providing stability and durability. Although the focus here is on lithium batteries, it's important to note the interconnectedness of these three industries.
3. Aluminum Profile Applications in Lithium Batteries
3.1 Electrode Current Collectors
Aluminum foils are widely used as current collectors in the anode of lithium batteries. The excellent electrical conductivity of aluminum allows for efficient transfer of electrons during charge and discharge cycles. Its smooth surface also facilitates good adhesion of the active electrode materials, ensuring stable electrochemical performance. For example, in high-performance lithium-ion batteries, ultra-thin aluminum foils are employed to minimize internal resistance and maximize energy output.
3.2 Battery Casings
The casing of a lithium battery needs to protect the internal components from external impacts, moisture, and other environmental factors. Aluminum profiles, often in the form of extruded or stamped sheets, are favored for their lightweight, corrosion-resistant nature. They can be designed with precision to fit different battery sizes and shapes, providing a reliable enclosure. Moreover, aluminum's thermal conductivity helps in dissipating heat generated during battery operation, preventing overheating and potential safety hazards.
3.3 Battery Module Structures
In larger battery systems, such as those used in electric vehicles or grid storage, individual batteries are grouped into modules. Aluminum profiles are used to construct the frames and supports for these modules. Their high strength-to-weight ratio enables the creation of robust yet lightweight structures that can withstand the mechanical stresses during transportation, installation, and operation. This not only ensures the integrity of the battery modules but also contributes to the overall weight reduction of the energy storage system.
4. Manufacturing Processes and Quality Control
4.1 Aluminum Processing for Battery Applications
Producing aluminum materials suitable for lithium battery use requires specialized processes. This includes precise rolling of aluminum foils to achieve the desired thickness and surface finish for electrode current collectors. Extrusion techniques for battery casings need to meet strict dimensional tolerances to ensure proper fit and sealing. Quality control measures are implemented at every stage to detect any defects, such as surface roughness, thickness variations, or alloy impurities, that could affect battery performance.
4.2 Compatibility and Integration Challenges
One of the challenges in using aluminum in lithium batteries is ensuring compatibility with other materials. For instance, the interface between the aluminum current collector and the active electrode material needs to be carefully engineered to prevent chemical reactions that could degrade battery performance over time. Additionally, during the assembly of battery components, proper sealing and insulation techniques must be employed to avoid short circuits and other electrical faults. Manufacturers are constantly researching and developing new coatings and surface treatments to enhance material compatibility and overall battery reliability.
5. Challenges and Solutions in Aluminum-Lithium Battery Applications
5.1 Cost Pressures
The cost of aluminum, especially high-purity aluminum required for battery applications, can be a significant factor. Additionally, the complex manufacturing processes add to the overall cost. To address this, efforts are being made to optimize production processes, such as improving the efficiency of aluminum foil rolling and extrusion, to reduce waste and energy consumption. Recycling of aluminum from used batteries is also being explored as a cost-effective alternative to sourcing virgin materials.
5.2 Technological Innovation Needs
As lithium battery technology evolves, there is a continuous demand for better aluminum materials and manufacturing techniques. For example, the development of next-generation lithium batteries with higher energy densities and faster charging capabilities may require aluminum with enhanced properties, such as improved thermal stability and electrochemical resistance. Research institutions and companies are collaborating to develop new aluminum alloys and fabrication methods to meet these emerging needs.
6. Future Trends
6.1 Advanced Aluminum Materials for Lithium Batteries
The future will see the emergence of novel aluminum alloys and composites specifically designed for lithium battery applications. These materials will likely possess improved mechanical, electrical, and chemical properties to keep up with the demanding requirements of next-generation batteries. For instance, aluminum-based nanocomposites could offer enhanced conductivity and stability, paving the way for more efficient and reliable energy storage solutions.
6.2 Growing Market Demand and Opportunities
With the global push towards clean energy and electrification, the demand for lithium batteries and, consequently, aluminum used in their production will continue to soar. This presents vast opportunities for aluminum processing companies to expand their production capacities, develop new products, and penetrate new markets. As the energy storage market diversifies, from residential power backup to large-scale grid storage, the versatility of aluminum in lithium battery applications will be further exploited.
7. Conclusion
In conclusion, aluminum profiles have become an indispensable part of lithium battery technology. Their unique properties enable the development of high-performance, reliable, and safe lithium batteries. Despite the challenges, the industry is constantly evolving to overcome them. Our company, aluinno, is dedicated to leveraging its expertise in aluminum processing to contribute to the growth of the lithium battery sector. By investing in research and development, optimizing manufacturing processes, and collaborating with partners in the value chain, we aim to stay at the forefront of this dynamic industry and meet the ever-growing demands for aluminum in lithium battery applications.