Decoding the Secrets: How to Identify High - Quality Aluminum Materials
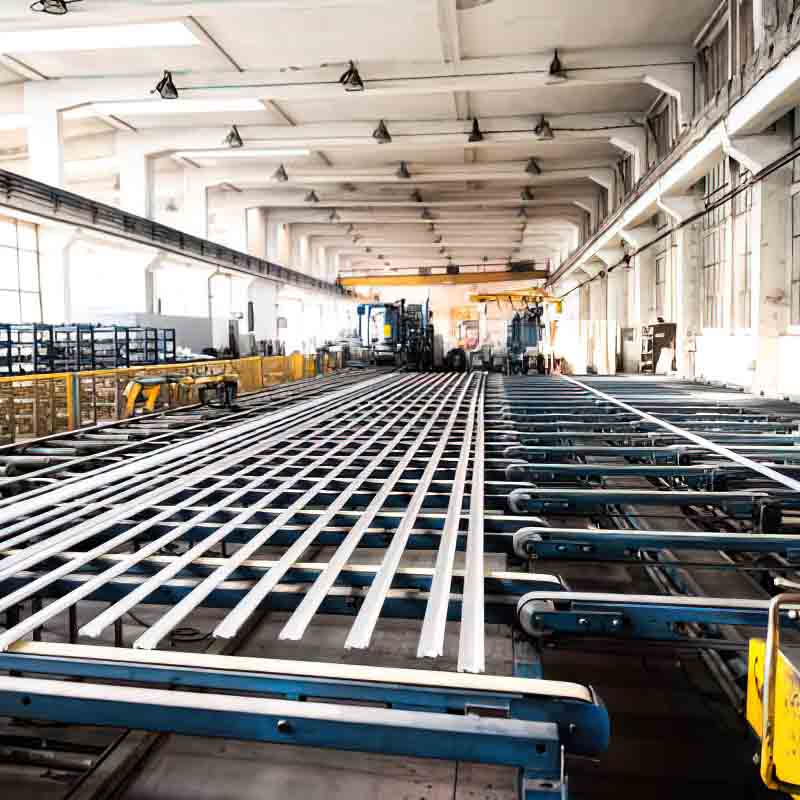
1. Introduction
Aluminum materials are widely used in modern industry and daily life, like in construction, automotive manufacturing, and electronic devices, due to their lightweight, high - strength, and corrosion - resistant features. As demand grows, the ability to distinguish high - quality aluminum becomes crucial as it ensures product performance and safety, while substandard aluminum can cause problems in different fields.
2. Aluminum Profile
Component | Chemical Symbol | Typical Content Range in General Aluminum Alloys (%) |
---|---|---|
Aluminum (Base Metal) | Al | 90 - 99.99 |
Copper | Cu | 0 - 5 (commonly 2 - 4 in certain alloys) |
Magnesium | Mg | 0 - 5 (around 0.5 - 3 in typical ones) |
Silicon | Si | 0 - 12 (for instance, 3 - 8 in some casting alloys) |
Zinc | Zn | 0 - 10 (like 4 - 7 in high-strength alloys) |
Manganese | Mn | 0 - 2 (usually 0.3 - 1.5 to enhance properties) |
Iron | Fe | 0 - 1.5 (ideally kept below 1 to maintain quality) |
Titanium | Ti | 0 - 0.5 (often added in trace amounts, e.g., 0.1 - 0.3) |
Chromium | Cr | 0 - 0.5 (about 0.1 - 0.3 in alloys for specific uses) |
2.1 Common Types of Aluminum Profiles
Aluminum profiles come in various types. One common type is the aluminum alloy window and door profile, precisely designed for a perfect window and door fit. With multiple chambers in the cross - section, like the bridge breakage aluminum alloy profile with a thermal break, it improves insulation and is suitable for energy - efficient buildings.
Industrial aluminum profiles, available in diverse shapes (T - shaped, H - shaped, L - shaped), are used in industrial machinery, automation equipment, and factory frameworks. For example, T - shaped ones are used as supports and connectors in conveyor systems due to high strength and stability.
2.2 Applications of Aluminum Profiles
In construction, aluminum profiles are crucial. They are used in building facades for a modern look, like in lightweight and weather - resistant aluminum curtain walls. In interior design, they make partitions, ceilings, and decorative trims, being flexible and customizable.
In industrial manufacturing, they are used in mechanical frames, such as in industrial robot body structures. Their lightweight nature enables faster robot movement, and high strength ensures operation stability and accuracy. They are also used in electronic device housings for protection and heat dissipation.
3. Aluminum Thickness
3.1 The Significance of Aluminum Thickness
The thickness of aluminum is crucial for material quality. Thicker aluminum sheets or profiles can bear more mechanical stress. For example, in large - span roof construction, they support roofing materials and resist wind and snow loads. Insufficient thickness may cause structural deformation or collapse.
Thickness is also linked to durability. Thicker aluminum endures wear better, especially in applications with constant friction or impact, like industrial machinery parts. Sufficient - thickness aluminum conveyor rollers can be used continuously with little wear, reducing replacements.
In aluminum - framed structures, proper thickness ensures stability. For example, in aluminum - framed greenhouses, it determines wind resistance and shape maintenance.
3.2 Measurement Methods and Tools
Common tools for measuring aluminum thickness include calipers and micrometers. A vernier caliper, with a main and vernier scale, can measure with a precision of up to 0.02 mm, useful for aluminum sheets or profiles, like window frames.
A micrometer, especially for small or high - precision components, can achieve a precision of up to 0.001 mm, such as in manufacturing aluminum heat sinks for electronic components.
Accurate measurement is vital. Incorrect measurements may lead to using non - compliant materials, affecting product performance and safety. Thus, calibrated tools and proper procedures are essential.
4. Hardness
4.1 Understanding Hardness in Aluminum Materials
Hardness in aluminum materials means the ability to resist indentation, scratching, or deformation, reflecting its quality and performance. Aluminum alloys get specific hardness by adjusting alloying elements and manufacturing processes. Adding magnesium and silicon can increase hardness and strength.
Aluminum's hardness is related to its internal structure. A fine - grained structure usually leads to higher hardness. Heat treatment can refine the grain structure and improve hardness, like solution heat treatment, quenching, and aging for aluminum alloys.
4.2 The Impact of Hardness on Quality
In different applications, aluminum hardness impacts performance. For wear resistance, harder aluminum resists abrasion better. In the automotive industry, engine components need enough hardness to endure high - pressure, high - temperature, and friction. Higher hardness means longer service life and better performance.
For compressive resistance, hard aluminum withstands more pressure without deforming. In industrial equipment construction, like aluminum storage tanks, the hardness of tank wall plates decides the tank's pressure - bearing capacity. Insufficient hardness may cause deformation or rupture.
4.3 Methods for Testing Hardness
Common methods to test aluminum hardness include the Rockwell hardness test. A diamond or steel indenter is pressed into the aluminum surface under a specific load, the indentation depth is measured, and the Rockwell hardness value is calculated. Factories often use it for quality control of aluminum alloy products.
The Brinell hardness test presses a hardened steel or carbide ball into the aluminum surface under a specified load, measures the indentation diameter, and determines the Brinell hardness number. It suits relatively soft aluminum materials or large - scale components.
5. Surface Treatment
5.1 Common Surface Treatment Methods
Aluminum materials can be treated with various surface treatment methods to enhance their properties. Anodizing, a common method, involves immersing aluminum in an electrolyte solution and applying an electric current to form a protective oxide layer, which can be further colored. Anodized aluminum is often used in architectural decoration.
Electroplating deposits a thin metal layer (like nickel, chromium, or zinc) on the aluminum surface, improving its corrosion and wear resistance. Electroplated aluminum parts are used in automotive and electronics industries.
Spraying, including powder and liquid spraying, is also widely used. Powder spraying electrostatically applies a dry powder coating cured by heat, while liquid spraying uses liquid paint. Spraying offers various colors and textures, and sprayed aluminum profiles are used in furniture manufacturing.
5.2 The Role of Surface Treatment
Surface treatment is crucial for aluminum materials. It improves corrosion resistance by acting as a barrier, such as in coastal areas. Aesthetics are enhanced with a wide range of colors, textures, and finishes, meeting design requirements in interior design. Durability is also increased as the protective layers prevent damage from external factors, like for sprayed aluminum signboards in the outdoor advertising industry.
6. Other Factors Affecting Aluminum Material Quality
6.1 Chemical Composition
The chemical composition of aluminum materials significantly influences their quality. Alloying elements are added to pure aluminum to create alloys. For example, adding magnesium (Mg) to 5052 in the 5000 - series alloys enhances strength and corrosion resistance, making it suitable for automotive fuel tanks. Silicon (Si) in 6061 of the 6000 - series alloys forms the Mg₂Si strengthening phase with magnesium, improving strength and hardness for aerospace and automotive use.
6.2 Manufacturing Process
The manufacturing process impacts quality too. In the extrusion process for aluminum profiles, precise control ensures a uniform structure and dimensional accuracy. Forging refines the grain structure of aluminum components, enhancing mechanical properties. Many aerospace critical parts, like aircraft engine components, are forged to withstand high - stress conditions.
6.3 Brand Reputation and Quality Assurance
Opting for aluminum materials from reputable brands is important. These brands have strict quality control throughout production. For example, aluinno adheres to high - quality standards. A reliable quality assurance system includes after - sales service, ensuring customer satisfaction. Considering brand reputation and quality assurance aids in obtaining high - quality products.
7. Conclusion
Distinguishing high - quality aluminum materials needs to consider multiple factors like profile type, thickness, hardness, surface treatment, chemical composition, manufacturing process, and brand reputation. Selecting quality aluminum is crucial for product performance, safety, and longevity. aluinno, a company committed to providing high - quality aluminum materials, with advanced tech, strict quality control, and good reputation, can be a reliable partner.
8. About aluinno
Aluinno is a leading aluminum material producer with years of experience and continuous innovation. It has top - notch production facilities and skilled professionals. Its products cover various aluminum items, known for high quality. The company adheres to strict international standards. It invests much in R & D, developing new alloys. Customer service is a priority, offering pre - sales consultation, technical support, and after - sales service to build long - term beneficial relationships.