Forging Ahead in the Ocean: Aluminum's Anti - corrosion Endeavor
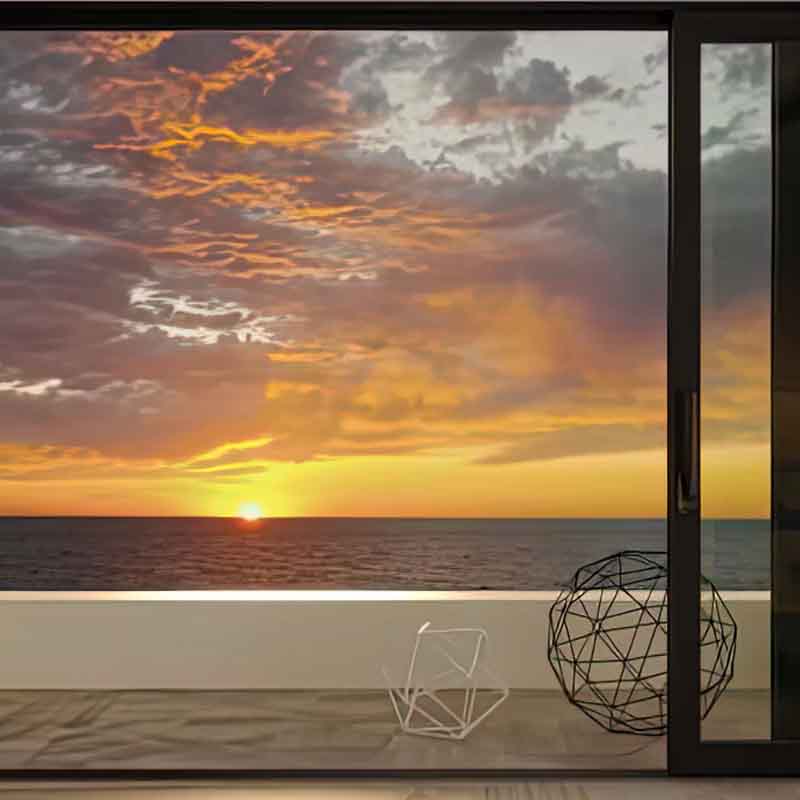
The Anti-corrosion Battle of Aluminum in Marine Engineering
In the vast and challenging field of marine engineering, aluminum and aluminum profiles have emerged as crucial materials. Their lightweight, high strength, and good formability make them ideal candidates for a variety of marine applications. However, the marine environment is notoriously harsh, presenting significant corrosion challenges that must be overcome.
1. Corrosion Challenges in Marine Environment
The marine environment is a complex and aggressive setting for materials. High salt spray concentration is one of the most prominent factors. Sea salt particles, carried by wind and waves, constantly bombard the surfaces of structures. For aluminum, this leads to the formation of chloride ions on its surface, which can initiate and accelerate corrosion processes. Chloride ions penetrate the oxide layer protecting the aluminum, disrupting its integrity and causing pitting corrosion.
Moreover, strong currents add another layer of complexity. The continuous flow of water not only erodes the surface mechanically but also facilitates the transport of corrosive substances, ensuring a constant supply of agents that can damage the aluminum. In areas with turbulent currents, like near propellers or in narrow channels, the wear and tear on aluminum components can be particularly severe.
2. Research & Development of New Corrosion-resistant Alloys
To combat these challenges, extensive research has been dedicated to developing new corrosion-resistant aluminum alloys. Scientists have been exploring different alloying elements and combinations. For instance, the addition of elements like magnesium, zinc, and rare earth metals has shown promising results. These elements can modify the microstructure of the alloy, enhancing its resistance to corrosion.
One recent breakthrough is an alloy that incorporates a specific ratio of magnesium and zinc. This alloy forms a more stable and protective oxide layer, effectively blocking the ingress of chloride ions. Laboratory tests and field trials have demonstrated its superior corrosion resistance compared to traditional aluminum alloys. Another avenue of research focuses on nanostructured alloys, which utilize the unique properties of nanoscale materials to further improve corrosion resistance and mechanical strength.
Year |
Estimated Market Size (in billions of US dollars) |
Growth Rate (CAGR) |
2020 |
5.2 |
- |
2021 |
5.8 |
11.5% |
2022 |
6.5 |
12.1% |
2023 |
7.3 |
12.3% |
2024 |
8.2 |
12.3% |
2025 |
9.3 |
13.4% |
2026 |
10.5 |
12.9% |
2027 |
11.9 |
13.3% |
2028 |
13.5 |
13.4% |
2029 |
15.3 |
13.3% |
2030 |
17.3 |
13.1% |
3. Coating Strategies for Different Marine Applications
3.1. Offshore Platforms
For offshore platforms, where structures are exposed to the harshest marine conditions, a multi-layer coating system is often employed. The base layer provides good adhesion to the aluminum surface, ensuring that subsequent layers stay firmly in place. Intermediate layers are designed to offer enhanced corrosion protection, usually containing corrosion inhibitors. The topcoat, which is exposed to the environment, must be resistant to abrasion, UV radiation, and salt spray. For example, epoxy-based coatings with added ceramic fillers have proven effective in providing long-term protection for the aluminum components of offshore platforms.
3.2. Shipbuilding
In shipbuilding, the choice of coating depends on the specific area of the vessel. For the hull, which is in constant contact with water, anti-fouling coatings are crucial. These coatings not only prevent corrosion but also inhibit the growth of marine organisms that can increase drag and fuel consumption. Copper-based anti-fouling coatings have been widely used, but new environmentally friendly alternatives, such as silicone-based coatings with biocide additives, are emerging. For interior components, coatings that provide both corrosion resistance and fire protection are preferred, given the potential fire hazards on board ships.
3.3. Subsea Facilities
Subsea facilities face extreme pressure and cold temperatures in addition to corrosion. Special coatings are required to withstand these conditions. Polyurethane coatings, with their excellent flexibility and low-temperature resistance, are often used. These coatings can adapt to the deformation of subsea structures due to pressure changes while maintaining their protective function. In some cases, sacrificial anode coatings are also applied, where a more reactive metal is incorporated into the coating to sacrificially protect the aluminum substrate.
4. Conclusion
In conclusion, while the marine environment presents formidable challenges to the use of aluminum and aluminum profiles, continuous research and innovation are paving the way for their successful application. The development of new corrosion-resistant alloys and advanced coating strategies are enabling these materials to withstand the rigors of the ocean. As technology progresses, we can expect aluminum to play an even more significant role in marine engineering, from building more efficient offshore platforms to constructing environmentally friendly ships and reliable subsea facilities. The future holds great promise for the marriage of aluminum technology and marine engineering, and it's an exciting journey that we are embarking on.