Aluminum Alloy Profiles and New Energy: An In - Depth Exploration
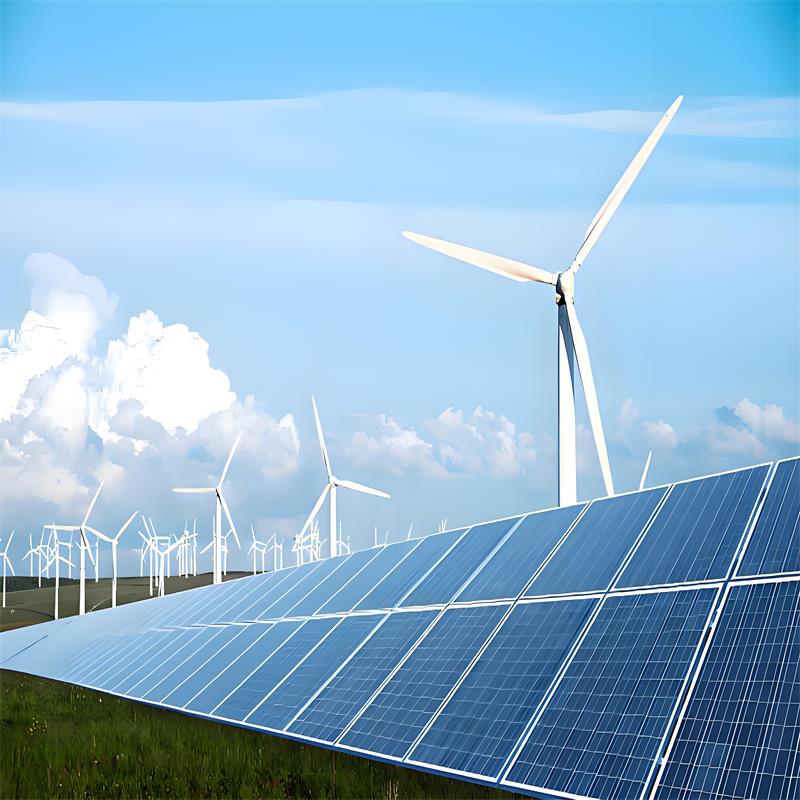
1. Introduction
In the modern world, the concepts of new energy and advanced materials are intertwined, with aluminum alloy profiles playing a crucial role. New energy, which includes solar, wind, hydro, and other renewable sources, is rapidly evolving to meet the global demand for clean and sustainable power. Aluminum alloy profiles, on the other hand, are known for their versatility, strength, and lightweight properties. This article aims to explore the relationship between aluminum alloy profiles and new energy, highlighting their applications, benefits, and future prospects.
2. Understanding Aluminum Alloy Profiles
2.1 Composition and Types
Aluminum alloy profiles are made by combining aluminum with other elements. 6063, 6061, 7005, and 7075 are some of the most common aluminum alloys used in profile manufacturing.
The 6063 alloy is favored in many applications due to its excellent formability and good surface finish. It contains magnesium and silicon as the main alloying elements. This alloy is often used in architectural applications where aesthetics and ease of fabrication are important.
6061 alloy has a higher strength - to - weight ratio compared to 6063. It contains magnesium, silicon, and copper, making it suitable for structural applications where greater strength is required.
7005 and 7075 alloys are high - strength alloys. 7005 alloy is often used in applications where a combination of strength and weldability is needed, such as in some bicycle frames. 7075 alloy, with its extremely high strength, is used in aerospace and high - performance applications.
2.2 Manufacturing Processes
One of the common manufacturing processes for aluminum alloy profiles is extrusion. Aluminum extrusion profile manufacturing involves forcing the aluminum alloy through a die to create a specific shape. This process allows for the production of complex cross - sectional profiles with high precision.
After extrusion, various surface treatments can be applied to the aluminum alloy profiles to enhance their properties. Surface treatment methods include anodized, powder coating, Electrophoresis, and more.
Anodized treatment forms a protective oxide layer on the surface of the aluminum, which not only improves its corrosion resistance but also provides a decorative finish.
Powder coating involves applying a dry powder to the surface of the aluminum profile and then curing it under heat. This provides a durable and colorful finish, protecting the aluminum from environmental factors.
Electrophoresis is a process where the aluminum profile is immersed in an electrolytic bath, and a coating is deposited on its surface. This method can produce a smooth and uniform finish.
2.3 Special Profiles
There are also some special aluminum alloy profiles in the market. For example, aluminum solar panel frames are specifically designed to support solar panels. These profiles need to be lightweight, strong, and corrosion - resistant to withstand outdoor conditions for a long time.
Aluminum tube profiles are used in various applications, such as in heat exchangers in some new energy systems. They can efficiently transfer heat due to the good thermal conductivity of aluminum.
Aluminum industry profile is a general term for profiles used in industrial applications. These profiles may have different shapes and functions according to specific industrial requirements.
3. Applications of Aluminum Alloy Profiles in New Energy
3.1 Solar Energy
In the field of solar energy, aluminum alloy profiles are widely used. Aluminum solar panel frames are a prime example. These frames are usually made of aluminum alloy profiles because of their excellent properties.
The lightweight nature of aluminum alloy profiles makes it easier to install and transport solar panels. Moreover, their corrosion resistance ensures that the solar panels can last for a long time in outdoor environments. In addition to frames, aluminum tracking systems also rely on aluminum alloy profiles. Aluminum tracking systems can adjust the orientation of solar panels to follow the sun's path, maximizing the energy absorption efficiency.
3.2 Wind Energy
In wind energy, aluminum alloy profiles are used in the construction of wind turbines. For example, the nacelle of a wind turbine may use aluminum alloy profiles for its enclosure. The lightweight and high - strength properties of aluminum alloy profiles help to reduce the overall weight of the wind turbine, which in turn improves its efficiency and reduces the load on the supporting structure.
Some parts of the wind turbine blades may also use aluminum alloy profiles. These profiles can be designed to have aerodynamic shapes through extrusion, which is beneficial for the performance of the wind turbine.
3.3 Electric Vehicles in New Energy
In the new energy vehicle industry, especially electric vehicles (EVs), aluminum alloy profiles are becoming increasingly important.
The body structure of an EV can be made lighter by using aluminum alloy profiles. This is crucial for increasing the vehicle's range, as a lighter vehicle requires less energy to move. For example, the doors, chassis, and some body panels of an EV can be made of aluminum alloy profiles.
The battery enclosure in an EV is also a key application area for aluminum alloy profiles. They need to protect the battery from external impacts and also help in dissipating the heat generated during the charging and discharging processes.
4. Benefits of Aluminum Alloy Profiles in New Energy Applications
4.1 Lightweight and High Strength
The combination of lightweight and high strength is one of the most significant advantages of aluminum alloy profiles in new energy applications. In the case of solar panels, lighter frames mean easier installation and transportation, which can reduce costs. In wind turbines, lighter components can improve the overall efficiency of the system. In electric vehicles, a lighter body can increase the vehicle's range and reduce energy consumption.
4.2 Corrosion Resistance
Most new energy applications involve outdoor or harsh environments. The corrosion resistance of aluminum alloy profiles ensures the long - term reliability of the systems. For example, solar panels are exposed to sunlight, rain, and wind for years. Aluminum alloy frames can withstand these environmental factors without significant degradation. In electric vehicles, the corrosion resistance of aluminum alloy profiles helps to maintain the integrity of the vehicle's structure and components.
4.3 Aesthetics and Design Flexibility
With various surface treatment options such as powder coating, Electrophoresis, and anodized finishes, aluminum alloy profiles can achieve different aesthetic effects. In solar panel installations, the appearance of the frames can be customized to match the surrounding environment. In electric vehicles, different surface finishes can be used to give the vehicle a unique look.
Moreover, the extrusion process allows for the production of complex shapes, providing great design flexibility. For example, in the design of wind turbine components, aluminum alloy profiles can be shaped to meet specific aerodynamic requirements.
4.4 Sustainability
Sustainability is a key factor in new energy applications. Aluminum is a highly recyclable material. At the end of the life cycle of an aluminum alloy profile - based product in new energy applications, the aluminum can be recycled and reused. This reduces the environmental impact and conserves natural resources.
5. Surface Treatments and Their Impact on New Energy Applications
5.1 Anodized Treatment
Anodized aluminum alloy profiles have a porous oxide layer on their surface, which can be dyed to different colors. In solar panel applications, anodized frames can have a decorative effect while also providing good corrosion resistance. In wind turbines, anodized parts can be more resistant to environmental corrosion.
5.2 Powder Coating
Powder coating provides a thick and durable coating on the aluminum alloy profiles. In electric vehicles, powder - coated body parts can have a smooth and attractive appearance. In solar panel frames, powder coating can protect against scratches and UV radiation.
5.3 Electrophoresis
Electrophoresis - treated aluminum alloy profiles have a uniform and smooth coating. This is beneficial for applications where a high - quality finish is required, such as in some high - end solar panel installations or in the interior components of electric vehicles.
5.4 Special Surface Treatments like Wood Grain and PVDF
Some special surface treatments like wood grain and PVDF are also used in certain applications. The wood grain finish can give aluminum alloy profiles an appearance similar to wood, which can be used in some architectural - integrated solar panel installations for aesthetic purposes. PVDF (polyvinylidene fluoride) coating is often used in high - performance applications where extreme weather resistance and durability are required.
6. Future Prospects
6.1 Technological Advancements in Aluminum Alloy Profiles
As technology continues to progress, we can expect further improvements in the properties of aluminum alloy profiles. Research may focus on developing new alloys with even better strength - to - weight ratios, higher corrosion resistance, and improved thermal conductivity.
For example, in the future, we may see the development of aluminum alloys specifically designed for high - efficiency solar tracking systems or ultra - lightweight electric vehicle components.
6.2 Expansion of Applications in New Energy
The demand for new energy is growing rapidly, and with it, the potential for new applications of aluminum alloy profiles. In the solar energy sector, as the efficiency of solar panels increases and the cost decreases, the scale of solar installations will expand. This will lead to an increased demand for aluminum alloy profiles for frames and tracking systems.
In the wind energy industry, larger and more efficient wind turbines will be developed, which may require new types of aluminum alloy profiles for their construction.
In the electric vehicle market, as electric vehicles become more mainstream, the use of aluminum alloy profiles in vehicle manufacturing will continue to increase, not only in the body and battery enclosures but also in other components.
6.3 Sustainable Development
The concept of Sustainability will play an even more important role in the future. Aluminum alloy profiles, being recyclable, are well - positioned to contribute to sustainable development in new energy applications. Manufacturers may focus on improving the recyclability of aluminum alloy profiles and reducing the energy consumption in their production processes.
7. Conclusion
In conclusion, aluminum alloy profiles are an integral part of new energy applications. Their unique properties, such as lightweight, high strength, corrosion resistance, and design flexibility, make them ideal for use in solar energy, wind energy, and electric vehicles. With various surface treatment options available, they can also meet different aesthetic and performance requirements. As the new energy industry continues to grow and evolve, the future prospects for aluminum alloy profiles in this field are very promising, especially considering the importance of sustainability in modern society.