Unveiling the Significance of Aluminum Profile Thickness in Load - Bearing Capacity
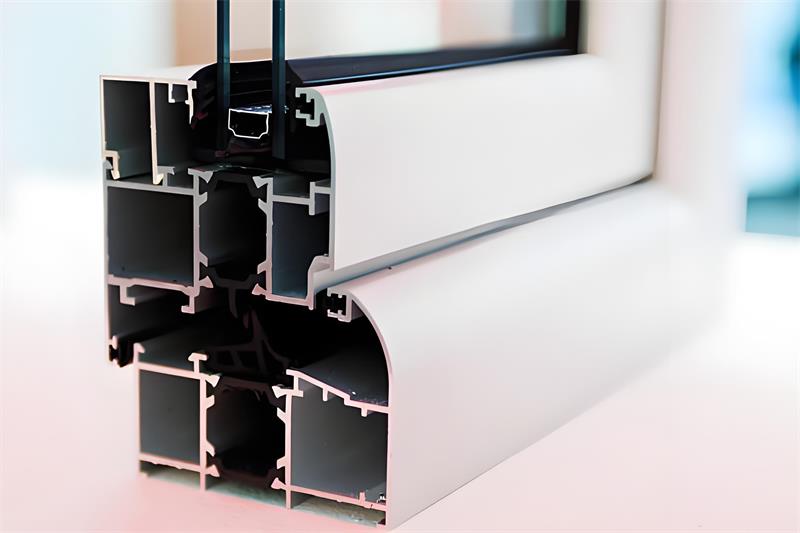
I. Introduction
In the contemporary world, aluminum profiles have permeated nearly every aspect of our built environment and industrial landscapes. They are the silent enablers of modern architecture, the cornerstones of functional interior design, and the reliable workhorses in manufacturing plants. From the towering skyscrapers adorned with sleek aluminum curtain walls to the unassuming kitchen cabinets with aluminum accents, these profiles are ubiquitous. However, a fundamental yet often underestimated characteristic - the thickness of the aluminum profile - holds the key to their load - bearing capabilities. This single dimension can make or break the performance, safety, and longevity of any structure incorporating aluminum profiles. As such, delving into its significance is of paramount importance for a wide range of professionals, from architects and engineers to product designers and end - users.
Aluminum Profile Thickness (mm) |
Compressive Load (N) |
Bending Moment (N·m) |
Tensile Load (N) |
2 |
500 |
10 |
400 |
3 |
1200 |
30 |
800 |
4 |
2200 |
60 |
1400 |
5 |
3500 |
100 |
2200 |
II. Understanding Aluminum Profiles
A. Definition and Composition
An aluminum profile is, at its core, a length of aluminum that has undergone the extrusion process to acquire a specific cross - sectional shape. Aluminum, in its pure form, is relatively soft and lacks the mechanical properties required for most practical applications. To overcome these limitations, it is alloyed with various elements. The 6063 aluminum alloy, a popular choice for profiles, contains magnesium and silicon. Magnesium, typically present in amounts around 0.45% - 0.9%, significantly boosts the alloy's strength through solid - solution strengthening. Silicon, in concentrations of around 0.2% - 0.6%, not only enhances strength but also improves the alloy's fluidity during extrusion.
The extrusion process is a fascinating feat of engineering. A billet of the aluminum alloy is heated to a specific temperature range, usually between 400°C and 500°C, depending on the alloy composition. This softened billet is then forced under high pressure, often several hundred tons, through a precisely engineered die. The die acts like a mold, imprinting the desired shape on the flowing aluminum, whether it's a simple circular tube for a handrail or a complex multi - cavity profile for a high - performance window.
B. Common Types and Applications
Aluminium Door and Window Profiles
These profiles are the guardians of our indoor comfort, separating the interior from the outside world. They must be lightweight enough for easy operation yet sturdy enough to support large glass panes. In regions prone to hurricanes or strong winds, door and window profiles need to withstand lateral forces that can reach hundreds of pounds per square foot. Additionally, they play a crucial role in thermal insulation and soundproofing, with the profile's design and thickness influencing the overall efficiency of these functions.
Aluminium Profiles for Cabinet
In modern kitchens and storage units, aluminum profiles offer a hygienic, durable alternative to wood. They can be customized to create sleek, minimalist designs. The shelves and drawers in cabinets need to bear the weight of various items, from heavy cookware to stacks of files. A well - designed aluminum cabinet profile with the right thickness ensures that the storage remains functional over time, without the shelves sagging or the drawers jamming.
Industrial Extrusion Profiles
Within industrial settings, extrusion profiles are the building blocks of machinery, conveyor systems, and structural frameworks. For example, in an automotive assembly line, aluminum extrusion profiles form the basis of robotic arms and conveyor belts. These applications demand high load - bearing capacities, as they often carry heavy components, withstand repetitive vibrations, and operate in harsh environments filled with chemicals, heat, and dust.
III. The Crucial Role of Thickness
A. Basic Principles of Load - Bearing
When a load is applied to an aluminum profile, the profile's cross - section is the first line of defense. Thickness plays a central role in how this cross - section resists stress. Consider a beam - like aluminum profile under a bending load. The outer fibers of the profile experience the highest stress levels. A thicker profile has more material in these critical outer regions, which means it can better distribute the bending stress over a larger volume. Mathematically, the moment of inertia (I), a key parameter in beam theory, is directly related to the thickness (h) of the profile. For a rectangular cross - section, the moment of inertia is proportional to h³. This exponential relationship shows that even a small increase in thickness can lead to a substantial boost in the profile's ability to resist bending.
Under compressive loads, thicker profiles also have an edge. They are less likely to buckle, as the increased cross - sectional area provides more stability. In simple terms, it's like a thick pillar being more resistant to toppling compared to a thin one when a vertical force is applied.
B. Impact on Different Applications
In Building Envelopes
For aluminum door and window frames in high - rise buildings, insufficient thickness can spell disaster. In addition to the wind loads, these frames must also account for the dead weight of the glass and any potential live loads from people leaning on them. A thin profile may start to deform, leading to air and water leakage, which can damage the interior finishes and reduce the energy efficiency of the building. In colder climates, the compromised seal due to frame deformation can also let in cold drafts, increasing heating costs.
Cabinetry Applications
As mentioned earlier, in cabinets, the wrong thickness can quickly turn a functional storage unit into a nuisance. If the vertical profiles supporting the shelves are too thin, the weight of books, dishes, or tools will cause the shelves to bow. This not only affects the aesthetics but also makes it difficult to access items stored on the shelves. Moreover, in commercial cabinetry used in workshops or offices, repeated use of drawers with thin - walled aluminum profiles can lead to premature wear and tear, reducing the overall lifespan of the cabinet.
Industrial Machinery
In industrial applications, the cost of downtime due to equipment failure is extremely high. Extrusion profiles with inadequate thickness in machinery frames may not be able to support the weight of motors, actuators, or workpieces. Vibration, which is common in machinery, can also cause thin profiles to resonate, leading to fatigue cracks over time. These cracks can propagate rapidly, ultimately causing the failure of critical components and halting production.
Key Mechanical Properties of Aluminum Alloy Profiles | ||||
Alloy Series | Tensile Strength (MPa) | Yield Strength (MPa) | Elongation (%) | Hardness (HB) |
1xxx | 70-110 | 20-50 | 10-25 | 15-30 |
2xxx | 240-480 | 140-345 | 4-12 | 60-130 |
3xxx | 110-170 | 45-110 | 15-25 | 25-45 |
5xxx | 170-280 | 90-210 | 10-25 | 45-75 |
6xxx | 180-310 | 110-240 | 8-18 | 50-85 |
IV. Factors Influencing Thickness Selection
A. Design Requirements
Structural Analysis
Engineers start by conducting a detailed structural analysis. In a large - scale building project, finite element analysis (FEA) may be used to model the behavior of aluminum curtain walls under different load scenarios. This involves inputting parameters such as the profile's cross - sectional geometry, material properties, and the expected loads. Based on the results, the required thickness can be calculated precisely. For example, in a stadium with large aluminum roofing structures, the profiles need to support not only the weight of the roof covering but also dynamic loads from wind gusts during events.
Function - Specific Requirements
Certain applications have unique requirements. For instance, in a solar panel mounting system made of aluminum profiles, the profiles need to be angled and have sufficient thickness to support the weight of the panels while also withstanding outdoor environmental conditions for decades. In a laboratory fume hood with aluminum frames, the profiles must be thick enough to hold the heavy glass sashes and resist chemical corrosion from fumes.
B. Environmental Factors
Weather Exposure
Outdoor aluminum profiles are constantly at the mercy of the elements. In coastal areas, the high salt content in the air can accelerate corrosion. A thicker profile provides more sacrificial material that can be corroded away before the structural integrity is compromised. In areas with extreme temperature variations, such as deserts, thermal expansion and contraction can cause stress in the profiles. Thicker profiles are better able to accommodate these changes without cracking or warping.
Chemical Exposure
In industrial environments, aluminum profiles may be exposed to various chemicals. For example, in a chemical processing plant, acidic or alkaline fumes can attack the surface of the profiles. A thicker layer of aluminum offers more protection, as the chemical reaction will take longer to penetrate through to the core of the profile, maintaining its load - bearing capacity for a more extended period.
C. Cost Considerations
Initial Cost
It's no secret that thicker aluminum profiles cost more. The additional raw material required for a thicker cross - section drives up the price per unit length. Moreover, the production process may be more time - consuming and energy - intensive for thicker profiles. For a small - scale DIY project, like building a simple bookshelf, the cost difference between a thin and thick aluminum profile can be a significant factor in the budget.
Long - Term Cost - Benefit Analysis
However, a myopic focus on initial cost can be a costly mistake in the long run. Structures made with thin profiles may require frequent repairs or replacements. In a commercial building, the cost of replacing a failed aluminum door and window system due to incorrect thickness selection can far exceed the initial investment in a thicker, more durable profile. A comprehensive cost - benefit analysis should consider factors such as maintenance costs, expected lifespan, and potential liability issues.
V. Production and Quality Control of Aluminum Profiles
A. Extrusion Process and Thickness Precision
Process Variables
The extrusion process is highly sensitive to multiple variables. The temperature of the aluminum billet is crucial; if it's too cold, the alloy will be too stiff to flow smoothly through the die, resulting in inconsistent thickness. If it's too hot, the profile may develop surface defects. Extrusion speed also affects thickness. A faster speed can cause the aluminum to flow unevenly, leading to thinner or thicker sections along the profile. Die design is another critical factor. A well - designed die with proper entry angles, land lengths, and cavity shapes can ensure a more uniform thickness across the entire extrusion.
Advanced Technologies for Precision
Modern extrusion plants are increasingly adopting advanced technologies. For example, laser - based thickness measurement systems can continuously monitor the thickness of the extruding profile in real - time. These systems can then feed back data to the extrusion press controls, allowing for immediate adjustments to maintain the desired thickness tolerance, which is often within a few tenths of a millimeter.
B. Quality Inspection and Standards
In - Process and Final Inspection
Quality inspection occurs at multiple stages. During the extrusion process, operators may periodically check the thickness using hand - held calipers or automated sensors. At the end of the production line, more comprehensive inspections take place. Samples are taken from batches of profiles, and their thickness is measured at multiple points along the length. Other properties such as tensile strength, hardness, and surface finish are also examined.
Compliance with Standards
There are numerous international and national standards that aluminum profile manufacturers must adhere to. For example, the European standard EN 755 specifies requirements for aluminum and aluminum alloy extruded products, including thickness tolerances, mechanical properties, and chemical composition. In the United States, ASTM standards play a similar role, ensuring that products sold in the market meet minimum quality and performance expectations.
VI. Future Trends and Innovations
A. New Alloy Developments
Researchers are constantly exploring new aluminum alloys that can offer enhanced properties with lower thickness requirements. Nano - alloying techniques are being investigated, where tiny amounts of nanoscale particles are added to the aluminum matrix. These nanoparticles can significantly improve strength, allowing for the design of thinner profiles without sacrificing load - bearing capacity. Additionally, high - entropy alloys, which combine multiple principal elements in near - equal proportions, show promise in creating aluminum - based alloys with unique mechanical and corrosion - resistant properties.
B. Smart Manufacturing
The era of smart manufacturing is upon us. In the production of aluminum profiles, this means using artificial intelligence and machine learning algorithms to optimize the extrusion process. These algorithms can analyze vast amounts of data from sensors monitoring temperature, pressure, and thickness, and predict process deviations before they occur. This enables manufacturers to produce profiles with even greater precision, reducing waste and improving quality.
C. Sustainable Production
With the growing emphasis on sustainability, recycled aluminum is becoming more prominent in profile production. Advances in recycling technologies are allowing for the purification and re - alloying of recycled aluminum to match the quality of virgin material. This not only reduces the environmental impact associated with mining new aluminum but also offers cost - savings opportunities, as recycled aluminum is generally less expensive. As more consumers demand sustainable products, manufacturers will need to ensure that recycled aluminum profiles meet the same strict thickness and load - bearing requirements as their virgin counterparts.
VII. Conclusion
The thickness of aluminum profiles is an all - encompassing factor that weaves through every aspect of their life cycle, from design and production to application and long - term performance. It is the linchpin that determines load - bearing capacity, influencing the safety, durability, and functionality of countless structures. By carefully considering design imperatives, environmental conditions, and cost implications, stakeholders can make informed decisions about the optimal thickness for aluminum profiles. As the industry hurtles forward with new technological advancements, a deep understanding of this critical dimension will be essential for harnessing the full potential of aluminum in creating sustainable, high - performing products across all sectors. Whether it's building our homes, factories, or the infrastructure of tomorrow, getting the thickness right is the first step towards a successful aluminum - based construction.