Unraveling the Mysteries: 6061 vs 6063 Aluminum Profiles
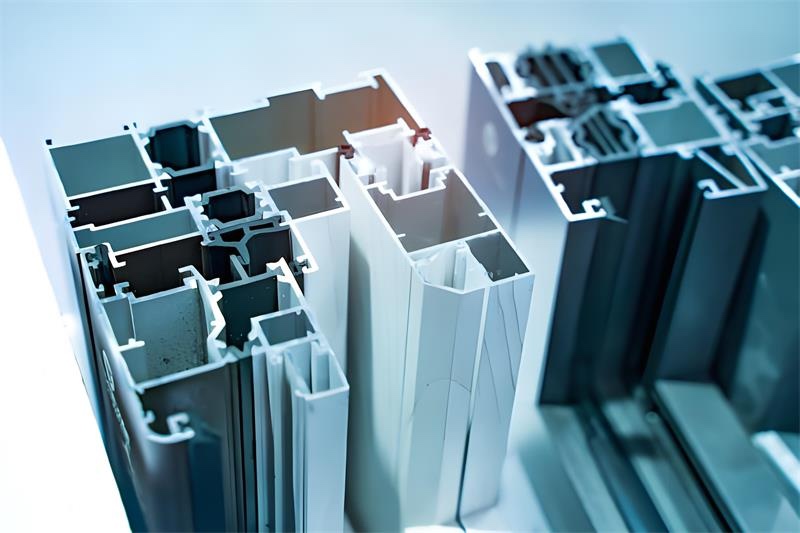
Outline
Introduction
In the realm of aluminum extrusion, the choice between 6061 and 6063 aluminum alloys is crucial. This article aims to clarify their differences, which is essential for engineers, designers, and consumers to make well - informed decisions.
Composition
· 6061 Alloy: It belongs to the Al - Mg - Si system. Key alloying elements like Mg, Si, Cu, along with traces of other elements, contribute to its strength and stress - corrosion resistance.
· 6063 Alloy: Also in the Al - Mg - Si family, mainly featuring Mg and Si, optimized for good extrusion and corrosion - resistance properties.
Physical Properties
· Strength & Hardness: 6061 has higher strength, suitable for high - load applications. 6063, with lower strength, suffices for non - critical uses.
· Density & Weight: 6061 is denser and heavier, while 6063 is lighter, influencing application choices.
Processing Capabilities
· Extrusion: 6061 has higher extrusion resistance but can make complex profiles. 6063 has excellent extrusion characteristics.
· Surface Treatment: 6061 often uses anodizing, and 6063 is popular with powder coating.
Application Areas
· Aerospace & Automotive: 6061 for critical parts; 6063 for non - critical, aesthetic components.
· Construction & Architecture: 6063 for doors, windows; 6061 for structural supports.
Selection
· Key Factors: Consider strength, weight, processing ease, cost, and aesthetics.
· Supplier: Collaborate with reliable suppliers for expertise and quality products.
Conclusion
Summarize the differences and stress the importance of careful alloy selection for project success.
1 Introduction
In the world of aluminum extrusion, the choice of alloy can significantly impact the performance and suitability of a product. Among the numerous aluminum alloys available, 6061 and 6063 stand out as two of the most commonly used, especially in the production of aluminum profiles. These alloys find their way into a vast array of applications, from construction to automotive, aerospace to industrial machinery. Whether you're an engineer, a designer, or a consumer, understanding the differences between 6061 and 6063 aluminum profiles is crucial for making informed decisions. In this blog post, we'll delve deep into the characteristics, properties, and applications of these two alloys, shedding light on what makes each one unique and when to use them. So, let's get started and explore the fascinating world of 6061 and 6063 aluminum extrusion profiles.
2 Composition: The Building Blocks
6061 Alloy Elements
The 6061 aluminum alloy belongs to the Al-Mg-Si system and is renowned for its versatility. Its primary alloying elements include magnesium (Mg), silicon (Si), copper (Cu), and traces of manganese (Mn), chromium (Cr), and zinc (Zn). Magnesium and silicon combine to form the Mg2Si phase, which is a crucial strengthening agent. This phase significantly boosts the alloy's strength, making it suitable for applications where structural integrity is vital. Copper, when added in small quantities, further enhances the alloy's resistance to stress corrosion cracking, a property that is highly valued in aerospace and marine applications. Additionally, manganese and chromium work in tandem to neutralize the detrimental effects of iron impurities, ensuring the alloy's overall performance remains top-notch.
6063 Alloy Elements
6063 aluminum alloy, also part of the Al-Mg-Si family, has a slightly different elemental makeup. It predominantly features magnesium and silicon, with a focus on achieving excellent extrusion characteristics and corrosion resistance. The ratio of magnesium to silicon is carefully controlled to optimize the alloy's properties. This alloy is designed to offer good formability, allowing it to be easily extruded into complex shapes, such as the intricate profiles used in architectural aluminum door and window frames. The presence of magnesium and silicon also contributes to the formation of a protective oxide layer on the surface, enhancing its resistance to environmental corrosion, which is especially beneficial for outdoor applications.
Mechanical Property | 6061 Aluminum Alloy (T6 Treatment) | 6063 Aluminum Alloy (T6 Treatment) |
Tensile Strength | Approximately 260 - 310 MPa (Some samples can reach 320 MPa under strict production conditions) | Usually in the range of 180 - 215 MPa |
Yield Strength | About 240 - 276 MPa | Roughly 160 - 195 MPa |
Elongation | Generally 8% - 16% | Typically 12% - 20% |
Hardness (Weiss Hardness) | Around 11 - 13 HW | Approximately 8 - 10 HW |
3 Physical Properties: Strength, Weight, and More
Strength and Hardness
One of the most significant differences between 6061 and 6063 aluminum alloys lies in their strength and hardness. 6061 alloy, with its higher alloying element content, exhibits greater strength. After proper heat treatment, it can achieve tensile strengths upwards of 290 MPa, making it suitable for applications where structural integrity and load-bearing capacity are crucial. This strength is attributed to the presence of copper and the well-optimized Mg2Si phase. In the aerospace industry, 6061 is used to manufacture aircraft frames, where it must endure extreme forces during flight. In automotive manufacturing, it's employed in engine components and chassis parts, providing the necessary rigidity and durability.
On the other hand, 6063 alloy, while still possessing decent strength, is comparatively lower in this regard. Its typical tensile strength ranges around 200 MPa. However, this doesn't mean it lacks utility. Instead, its strength is more than sufficient for many non-critical structural and decorative applications. In the building and construction sector, 6063 is the go-to choice for aluminum door and window profiles. It can support the weight of the glass panes and withstand normal wind loads while allowing for easy fabrication and installation. The relatively lower strength also means it can be more easily machined and formed into intricate shapes, which is a boon for architects and designers looking to create unique facades and interiors.
Density and Weight
Density plays a vital role in determining the suitability of an alloy for specific applications, especially when weight is a critical factor. 6061 aluminum alloy has a slightly higher density, approximately 2.7 g/cm³. This makes it denser and, consequently, heavier compared to 6063. While the difference might seem marginal, in applications where every gram matters, such as in aerospace and some high-performance automotive applications, it can have a significant impact. However, the added weight is often a trade-off for the increased strength it offers. For instance, in the construction of satellites, where the need for robustness and resistance to space debris impacts is paramount, the higher density of 6061 is tolerated in favor of its strength.
In contrast, 6063 aluminum alloy has a lower density, around 2.69 g/cm³. This makes it a preferred choice in scenarios where weight reduction is a priority. In the building industry, for example, using 6063 for curtain walls and window frames helps reduce the overall load on the building structure. It's also advantageous in the manufacturing of consumer products like aluminum ladders and furniture, where portability and ease of handling are desired. The lighter weight of 6063 allows for easier installation and transportation, without sacrificing too much on the structural integrity required for these applications.
4 Processing Capabilities: From Extrusion to Finishing
Extrusion Process
When it comes to the extrusion process, both 6061 and 6063 alloys have their own characteristics. 6061 alloy, due to its relatively higher alloying content, has a slightly higher extrusion resistance. This means that more force is required to push the heated aluminum through the die. However, this also allows for the production of more complex and structurally robust profiles. In the aerospace industry, where precision and strength are paramount, 6061 is often chosen to manufacture intricate components like wing spars and fuselage frames. The extrusion process for 6061 requires careful control of temperature, extrusion speed, and die design to ensure the desired mechanical properties are achieved.
On the other hand, 6063 alloy is renowned for its excellent extrusion characteristics. It flows more easily during the extrusion process, enabling the production of highly detailed and complex shapes with greater efficiency. This makes it a favorite in the architectural and construction sectors, where elaborate aluminum door and window profiles, curtain wall components, and decorative trim pieces are in high demand. The extrusion temperature window for 6063 is relatively wide, providing manufacturers with more flexibility in production. Additionally, its lower extrusion force requirements translate to reduced energy consumption and potentially lower production costs, making it an economically viable option for large-scale production of aluminum profiles.
Surface Treatment
Surface treatment is a crucial aspect that can enhance the performance and aesthetics of aluminum profiles. 6061 alloy, after proper surface treatment, exhibits excellent resistance to corrosion and wear. Anodizing is a commonly used surface treatment method for 6061. During anodizing, an oxide layer is formed on the surface of the aluminum, which not only provides a protective barrier against environmental factors but also allows for coloring, giving the profile a customized appearance. This makes 6061 suitable for applications where durability and a professional finish are essential, such as in industrial machinery, outdoor equipment, and high-end architectural projects.
6063 alloy, with its smooth surface finish straight out of the extrusion process, lends itself well to a variety of surface treatments. Powder coating is a popular choice for 6063 aluminum profiles, especially in architectural applications. The powder coating process creates a thick, durable finish that can mimic the appearance of other materials like wood or stone, while providing enhanced protection against UV radiation, moisture, and scratches. This allows architects and designers to achieve the desired aesthetic while ensuring the longevity of the aluminum components. Whether it's a modern office building with sleek aluminum curtain walls or a residential property with stylish aluminum window frames, 6063's surface treatment capabilities make it a standout choice for enhancing the visual appeal of any structure.
5 Application Areas: Where They Shine
Aerospace and Automotive
In the aerospace and automotive industries, where precision, strength, and weight reduction are of utmost importance, the choice between 6061 and 6063 aluminum profiles can make a significant difference. 6061 alloy, with its superior strength and stress corrosion resistance, finds extensive use in critical structural components. In aircraft manufacturing, it's employed in the construction of wing spars, fuselage frames, and landing gear components. These parts must endure extreme forces during takeoff, flight, and landing, and 6061's ability to maintain its integrity under such conditions is unmatched. In the automotive sector, 6061 is used in engine blocks, transmission housings, and chassis components. Its good heat dissipation properties, combined with its strength, make it ideal for these applications where performance and durability are key.
On the other hand, 6063 alloy, while not as strong as 6061, offers excellent formability and a smooth surface finish. This makes it a preferred choice for non-critical interior and exterior components where aesthetics play a significant role. In aerospace, 6063 is used for interior panels, overhead storage bins, and seat frames. It allows for easy customization and can be anodized or powder coated to match the overall cabin design. In the automotive industry, 6063 is commonly seen in trim pieces, such as window frames, door handles, and bumper fascias. It provides a sleek, finished look while still offering sufficient strength to withstand normal operating conditions.
Construction and Architecture
The construction and architecture industries are among the largest consumers of aluminum profiles, and both 6061 and 6063 alloys have their niche applications. 6063 alloy is the go-to choice for aluminum door and window profiles. Its moderate strength, combined with its excellent extrusion and surface treatment capabilities, allows for the production of intricate and aesthetically pleasing frames. Architects can choose from a wide range of colors and finishes to match the building's design, whether it's a modern high-rise or a traditional residential property. 6063 is also widely used in curtain wall systems, where its lightweight nature helps reduce the overall load on the building structure while providing a durable and weather-resistant enclosure.
6061 alloy, on the other hand, is often used in structural support applications within buildings. In high-rise construction, it's used for columns, beams, and trusses, where its high strength and load-bearing capacity are essential. Additionally, in areas prone to seismic activity, 6061's robustness can provide added safety and stability. It can also be used in industrial buildings and warehouses, where heavy loads and equipment need to be supported. While it may not have the same visual appeal as 6063 in decorative applications, its structural performance more than compensates in these critical support roles.
6 Selecting the Right One for Your Project
Key Consideration Factors
Selecting the appropriate aluminum alloy for your project hinges on a multitude of factors. Firstly, consider the strength requirements. If your application demands high load-bearing capacity, such as in the construction of a bridge or industrial machinery frames, 6061 alloy would be the preferred choice. Its superior tensile strength and hardness can withstand significant forces without deformation. For instance, in a building project where large-span aluminum trusses are needed to support the roof, 6061's strength ensures structural integrity.
On the other hand, if the project involves non-structural or decorative elements, like aluminum window frames in a residential building, 6063 alloy's moderate strength and excellent formability come to the fore. It can be easily fabricated into intricate designs while still providing sufficient support for the glass panes.
Weight is another crucial factor. In applications where weight reduction is essential, such as in aerospace components or portable consumer products, 6063's lower density makes it a more suitable option. In the automotive industry, using 6063 for non-critical body parts helps reduce the overall vehicle weight, leading to improved fuel efficiency. However, if strength takes precedence over weight, as in the case of engine blocks or chassis components, 6061's higher density and strength are more desirable.
The ease of processing also plays a significant role. If your manufacturing process requires complex extrusion shapes or high production volumes, 6063's excellent extrusion characteristics and wide temperature window offer greater efficiency. This is particularly beneficial in the production of aluminum profiles for architectural applications, where custom shapes and large quantities are often required. For projects that demand strict dimensional accuracy and strength in the final product, 6061 might be favored, despite its more challenging extrusion process.
Cost considerations cannot be overlooked. Generally, 6063 alloy is more cost-effective due to its easier processing and lower alloying element content. For large-scale construction projects, such as curtain wall installations in commercial buildings, using 6063 can result in significant cost savings without compromising on the overall performance. However, for specialized applications where the unique properties of 6061 are indispensable, the higher cost may be justified.
Finally, consider the aesthetic requirements. If a smooth surface finish and a wide range of color options are desired, 6063's compatibility with various surface treatments, such as powder coating, makes it an ideal choice for architectural and decorative applications. In contrast, 6061, with its emphasis on strength and durability, may have a more utilitarian appearance, suitable for industrial and infrastructure projects where functionality trumps aesthetics.
Working with Suppliers
When it comes to choosing the right aluminum alloy, collaborating with a reliable supplier is of utmost importance. A reputable aluminum extruder can offer invaluable expertise and guidance throughout the selection process. They can provide detailed information about the properties and applications of 6061 and 6063 alloys, helping you make an informed decision based on your specific project requirements.
Moreover, a good supplier will have the capabilities to offer custom extrusion profiles. If your project demands unique shapes or dimensions that are not available as standard profiles, they can work with you to design and manufacture bespoke aluminum profiles. This level of customization is especially crucial in industries like aerospace and high-end architecture, where every component needs to be tailored to precise specifications.
Quality control is another area where a reliable supplier shines. They will ensure that the aluminum profiles meet the required industry standards, whether it's in terms of mechanical properties, surface finish, or dimensional accuracy. This gives you peace of mind, knowing that the materials you receive will perform as expected in your project.
Finally, consider the supplier's after-sales support. In the event of any issues or questions regarding the aluminum profiles, a responsive and helpful supplier can provide timely assistance. This includes technical support, troubleshooting, and even assistance with installation and maintenance, ensuring the smooth progress of your project from start to finish.
7 Conclusion
In conclusion, the differences between 6061 and 6063 aluminum profiles are multi-faceted, encompassing composition, physical properties, processing capabilities, and application areas. 6061 alloy, with its higher strength and alloying element content, is tailored for applications demanding structural robustness and resistance to harsh conditions, such as in aerospace and heavy-duty industrial machinery. On the other hand, 6063 alloy, prized for its excellent formability and surface treatment options, reigns supreme in the construction and architectural sectors, where aesthetics and ease of fabrication are key.
Selecting the right alloy for your project is not a one-size-fits-all decision. It requires a careful evaluation of your specific needs, considering factors like strength requirements, weight limitations, processing complexity, and budget constraints. By understanding the unique characteristics of 6061 and 6063 alloys, you can make an informed choice that optimizes the performance and cost-effectiveness of your project.
Whether you're embarking on a large-scale construction project, designing a cutting-edge aerospace component, or simply looking to upgrade your home's aluminum fixtures, the knowledge of these two alloys will serve you well. So, the next time you're faced with the choice between 6061 and 6063 aluminum profiles, you can confidently make the decision that will drive your project to success.