How Metal Profiles Are Made
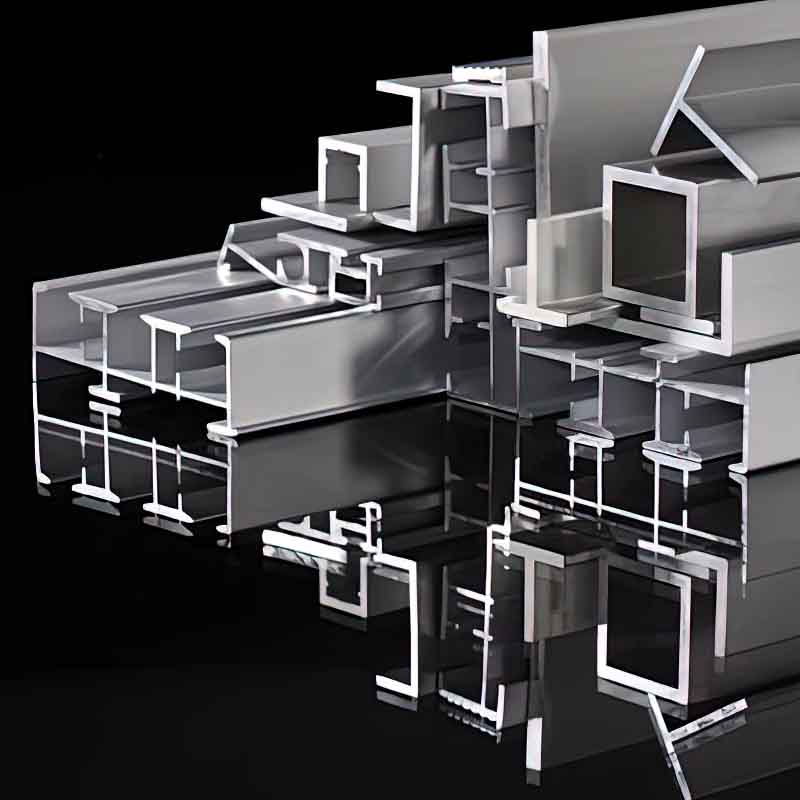
Outline
Introduction: Briefly introduce the significance of aluminum profiles in modern industries and the importance of understanding their manufacturing process.
What Are Aluminum Profiles: Define aluminum profiles and explain why aluminum is chosen for making them, highlighting its properties like low density, high strength, corrosion resistance, and recyclability.
The Manufacturing Process: Detail the steps including raw material preparation (selecting ingots and adding alloying elements), melting and casting (heating, refining, and continuous casting), extrusion process (using a die and the role of extrusion ratio), heat treatment (annealing and aging), and surface finishing (anodizing, powder coating, etc.).
Custom Aluminum Profiles: Discuss the need for customization in various industries, the process of creating them (consultation, design, mold making), and their benefits (perfect fit, unique design, tailored properties).
Quality Control: Emphasize the importance of quality control and key control points in raw materials, production process, and finished products.
Applications: Illustrate the uses of aluminum profiles in construction, automotive, aerospace, and other industries.
Why Choose Aluinno: Present the company's reputation, product range and quality, and customization and service.
Conclusion: Summarize the importance of aluminum profile manufacturing process and the role of choosing the right profiles in different industries.
Introduction
In today's modern world, aluminum profiles have become an essential part of numerous industries. From the sleek frames of high-rise buildings to the lightweight components of advanced aircraft, aluminum profiles play a crucial role in enhancing the performance and functionality of various products. Understanding how these metal profiles are made is not only fascinating but also vital for making informed decisions when it comes to choosing the right aluminum profiles for specific applications. In this article, we will take a detailed look at the manufacturing process of aluminum profiles and explore the different types and their applications.
What Are Aluminum Profiles
Definition of Aluminum Profiles
Aluminum profiles are structural components made from aluminum alloys that are processed into specific shapes through a series of manufacturing techniques. These profiles can have a wide variety of cross-sectional geometries, such as squares, rounds, rectangles, and more complex custom designs. They are widely used in construction, automotive, aerospace, industrial machinery, and many other fields due to their unique combination of properties like lightweight, high strength, good corrosion resistance, and excellent formability.
Why Aluminum for Profiles
Aluminum is the preferred material for profiles mainly because of its remarkable characteristics. Firstly, its low density makes the resulting profiles extremely lightweight, which is highly desirable in applications where weight reduction is crucial, such as in the automotive and aerospace industries. This helps to improve fuel efficiency and overall performance. Secondly, aluminum has relatively high strength, especially when alloyed with other elements like magnesium, silicon, and copper. It can withstand significant mechanical loads without deformation or failure. Additionally, aluminum has excellent corrosion resistance, forming a natural oxide layer on its surface that protects it from environmental factors like moisture and chemicals. This property makes it suitable for both indoor and outdoor applications, even in harsh conditions. Moreover, aluminum is a highly recyclable material, which aligns with the growing demand for sustainable manufacturing processes.
The Manufacturing Process of Aluminum Profiles
Raw Material Preparation
The manufacturing process begins with the careful selection of raw materials. High-quality aluminum ingots are the primary source. These ingots are sourced from reliable suppliers and undergo strict quality inspections to ensure they meet the required chemical composition standards. Depending on the desired properties of the final profiles, other alloying elements may be added in precise amounts during the melting stage. For example, adding magnesium can enhance the strength and hardness of the aluminum alloy, while silicon can improve its casting properties and fluidity.
Melting and Casting
Once the raw materials are prepared, they are loaded into a melting furnace. The furnace heats the aluminum and alloying elements to a specific temperature range, typically between 700°C to 800°C, to form a homogeneous molten metal. During this process, various refining techniques are employed to remove impurities such as oxides and other contaminants. After the melting and refining steps, the molten aluminum is cast into billets or slabs of a specific size and shape. Continuous casting is a commonly used method, where the molten metal is continuously poured into a water-cooled mold to form long, solid billets. This method ensures a uniform structure and quality throughout the length of the billet.
Extrusion Process
The extrusion process is a key step in shaping the aluminum into profiles. The preheated aluminum billet is placed in an extrusion press. A ram in the press applies a high pressure to force the billet through a die with the desired cross-sectional shape. The die is carefully designed and manufactured with high precision to ensure the accuracy of the profile's shape and dimensions. As the billet passes through the die, it takes on the shape of the die cavity and is elongated into a long profile. The extrusion ratio, which is the ratio of the cross-sectional area of the billet to that of the extruded profile, plays an important role in determining the quality and properties of the final product. A higher extrusion ratio generally results in better mechanical properties due to the intense deformation of the metal.
Heat Treatment (Optional but Common)
Heat treatment is often carried out to further improve the properties of the aluminum profiles. One common heat treatment method is annealing. During annealing, the extruded profiles are heated to a specific temperature and held for a certain period to relieve internal stresses generated during the extrusion process. This helps to improve the dimensional stability and mechanical properties of the profiles. Another important heat treatment process is aging. By subjecting the profiles to a controlled temperature and time cycle after quenching, the alloying elements precipitate out in a fine and uniform manner, significantly increasing the strength and hardness of the aluminum.
Surface Finishing
Surface finishing is an important aspect of aluminum profile manufacturing as it not only enhances the appearance but also improves the performance and durability of the profiles. Anodizing is a widely used surface treatment method. In this electrochemical process, the aluminum profile is immersed in an electrolyte solution and an electric current is passed through it. This causes the growth of a thick and dense oxide layer on the surface of the aluminum, which greatly enhances its corrosion resistance. Anodized aluminum can also be colored through the addition of dyes or pigments during the process, providing a wide range of aesthetic options. Powder coating is another popular choice. In powder coating, a dry powder is electrostatically applied to the surface of the aluminum profile and then cured under heat. This results in a smooth, durable, and highly resistant finish that can protect the profile from scratches, abrasion, and weathering. In addition to these, other surface finishing methods like mechanical polishing, brushing, and chemical etching are also used depending on the specific requirements of the application.
Custom Aluminum Profiles: Tailoring to Specific Needs
Understanding Customization Requirements
In many industries, standard aluminum profiles may not meet the unique design and performance requirements of certain projects. Custom aluminum profiles are designed to address these specific needs. The need for customization can arise from various factors. For example, in the aerospace industry, the design of aircraft components often requires highly specialized shapes and dimensions to fit within the complex structures and meet strict performance criteria. In the construction of architecturally unique buildings, custom profiles may be needed to achieve specific aesthetic and structural effects. Similarly, in the manufacturing of high-precision industrial machinery, custom aluminum profiles can provide the exact functionality and fit required.
The Process of Creating Custom Aluminum Profiles
The process of creating custom aluminum profiles starts with a detailed consultation between the customer and the manufacturer. The customer communicates their specific requirements, including the desired shape, dimensions, mechanical properties, and any special features or finishes. The manufacturer's engineering team then uses advanced design software to develop a customized design solution. Once the design is finalized, a dedicated mold is manufactured. The mold-making process requires high precision and expertise to ensure that the resulting profile meets the exact specifications. After the mold is ready, the extrusion and subsequent processing steps are carried out following the same principles as for standard profiles but with strict adherence to the custom design requirements.
Benefits of Custom Aluminum Profiles
Custom aluminum profiles offer several significant advantages. Firstly, they provide a perfect fit for the specific application, ensuring optimal performance and functionality. This can lead to improved efficiency and reliability of the final product. Secondly, custom profiles allow for unique design possibilities, enabling manufacturers to differentiate their products in the market. For example, in the consumer electronics industry, custom aluminum profiles can give products a distinctive and sleek appearance. Moreover, by tailoring the mechanical properties of the profiles to the exact needs of the project, it is possible to achieve better performance in terms of strength, stiffness, and weight distribution.
Quality Control in Aluminum Profile Manufacturing
Importance of Quality Control
Quality control is of utmost importance in aluminum profile manufacturing. High-quality profiles ensure the safety and reliability of the end products in which they are used. Poor-quality profiles can lead to structural failures, reduced performance, and increased maintenance costs. In industries such as aerospace and automotive, where safety is critical, any defect in the aluminum profiles can have serious consequences. Therefore, strict quality control measures are implemented throughout the manufacturing process to guarantee that the profiles meet the required standards.
Key Quality Control Points
During the raw material stage, comprehensive tests are conducted to verify the chemical composition and purity of the aluminum ingots and alloying elements. This includes spectroscopy analysis and other methods to ensure that the materials are free from contaminants and have the correct alloying ratios. In the production process, parameters such as temperature, pressure, and extrusion speed are closely monitored and controlled. Any deviation from the specified values can affect the quality of the profiles. Regular inspections of the extruded profiles are carried out using advanced measuring tools to check the dimensions, shape accuracy, and surface quality. After the profiles are finished, mechanical tests such as tensile strength, hardness, and impact resistance tests are performed to ensure that the profiles meet the required mechanical properties. Additionally, surface finish quality is evaluated through visual inspection and specialized testing methods to ensure that the anodizing or powder coating is of high quality and provides the expected protection and aesthetic appeal.
Applications of Aluminum Profiles
Construction Industry
In the construction industry, aluminum profiles are widely used in various applications. Aluminum window and door frames are popular due to their corrosion resistance, which ensures a long service life even in harsh weather conditions. They also provide good thermal insulation properties when properly designed. Curtain walls made from aluminum profiles are a common feature in modern high-rise buildings. These non-structural walls not only enhance the aesthetic appearance of the building but also provide protection from the elements. Aluminum profiles are also used in roofing and structural supports. Their high strength-to-weight ratio makes them an ideal choice for spanning large distances and supporting heavy loads while reducing the overall weight of the structure.
Automotive Industry
The automotive industry has increasingly turned to aluminum profiles to improve vehicle performance. Aluminum body frames are used to reduce the weight of the vehicle, which in turn improves fuel efficiency and handling. This is especially important in the era of strict fuel consumption regulations. Aluminum trims and exterior components, such as bumpers and side mirrors, are also commonly used due to their durability and resistance to corrosion. In addition, lightweight aluminum engine components are being developed to enhance engine performance and reduce emissions.
Aerospace Industry
In the aerospace sector, aluminum profiles are essential for the construction of aircraft. The frames of aircraft bodies are made from high-strength aluminum profiles that can withstand the extreme forces during flight while keeping the weight of the aircraft to a minimum. Interior structures like seating frames and overhead storage bins also utilize aluminum profiles to reduce weight. Wing components, such as spars and ribs, are critical parts made from aluminum due to its excellent strength-to-weight ratio. These components must support the wings during flight and endure significant aerodynamic loads.
Other Industries
Aluminum profiles find applications in many other industries as well. In the electronics industry, they are used in the manufacturing of computer chassis, mobile phone frames, and other electronic devices due to their good electrical conductivity and heat dissipation properties. In the furniture industry, aluminum profiles are used to create modern and durable furniture frames. In the marine industry, aluminum's corrosion resistance in saltwater makes it an ideal material for boat hulls, decks, and docks.
Why Choose Aluinno for Aluminum Profiles
Our Company's Reputation
Aluinno has built a solid reputation in the aluminum profile manufacturing industry over the years. We have a proven track record of delivering high-quality products and excellent customer service. Our commitment to quality and innovation has earned us the trust of numerous clients across various industries.
Product Range and Quality
We offer a wide range of aluminum profiles, including both standard and custom designs. Our standard profiles come in a variety of common shapes and sizes to meet the general needs of different industries. For those with special requirements, our custom aluminum profiles are tailored to perfection. We use only the highest quality raw materials and state-of-the-art manufacturing processes to ensure that our products meet the strictest quality standards. Our quality control team closely monitors every step of the production process to guarantee the consistency and reliability of our profiles.
Customization and Service
At Aluinno, we understand the importance of customization. Our experienced engineering team works closely with customers to understand their unique needs and develop customized solutions. We provide comprehensive support from the initial design concept to the final delivery of the products. Our after-sales service also ensures that our customers have a seamless experience and can rely on us for any assistance they may need.
Conclusion
The manufacturing process of aluminum profiles is a complex and sophisticated combination of various techniques that result in highly versatile and valuable products. Understanding this process and the different types of aluminum profiles available is crucial for making the right choices in different industries. Whether it's for construction, automotive, aerospace, or other applications, the quality and suitability of the aluminum profiles can significantly impact the performance and success of the final products.