Industrial Aluminum: Key Support for New Energy Vehicles
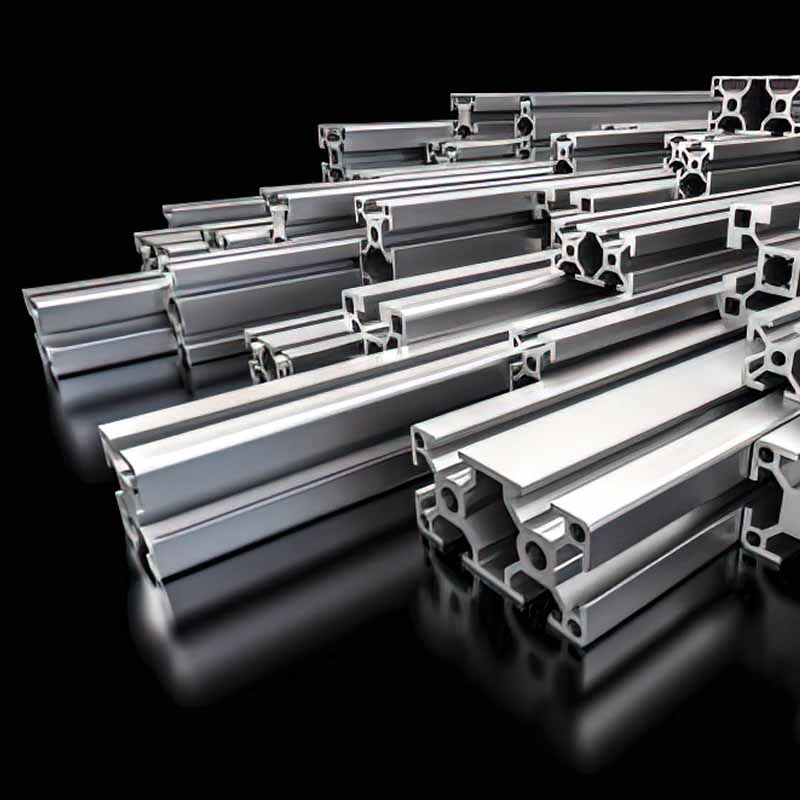
-
Introduction:
Highlight the significance of industrial aluminum in the development of NEVs, introducing the exploration of its advantages, applications, etc.
Advantages:
Applications:
Manufacturing Process:
Market and Future:
-
Conclusion:
Industrial aluminum is vital, and aluinno contributes to the industry's development.
1 Introduction
In the dynamic landscape of the automotive industry, new energy vehicles (NEVs) have emerged as a promising solution to environmental challenges and the over - reliance on fossil fuels. Among the plethora of materials contributing to the development of NEVs, industrial aluminum has emerged as a linchpin. Its unique set of properties makes it an ideal choice for a wide range of applications in NEVs, spanning from the vehicle body to the battery system. This article aims to comprehensively explore the significance of industrial aluminum in the new energy vehicle domain, delving into its advantages, applications, manufacturing processes, and future prospects.
2 The Advantages of Industrial Aluminium in the Automotive Field
2.1 Lightweight Feature and Its Significance
Industrial aluminium is well - known for its lightweight nature. With a density of approximately 2.7 g/cm³, which is roughly one - third that of steel, this characteristic is a game - changer for new energy vehicles. For instance, studies have shown that every 10% reduction in vehicle weight can lead to a 6% - 8% increase in the range of electric vehicles. In a world where extending the driving range of NEVs is a top - priority, the lightweight advantage of industrial aluminium becomes even more crucial.
Lightweight vehicles also consume less energy during operation. In battery - powered NEVs, reducing the vehicle's weight means that the battery has to expend less energy to move the vehicle, thereby enhancing the overall energy efficiency. This not only benefits the environment by reducing energy consumption but also improves the cost - effectiveness of NEV operation for consumers. For example, a mid - sized electric sedan with an aluminum - intensive body can achieve a 15 - 20% increase in energy efficiency compared to its steel - bodied counterpart, translating into longer driving ranges on a single charge.
2.2 Excellent Corrosion Resistance
Another remarkable advantage of industrial aluminium is its excellent corrosion resistance. When exposed to the atmosphere, aluminium forms a thin, self - protecting oxide layer on its surface. This oxide layer acts as a robust barrier, preventing further oxidation and corrosion of the underlying metal.
In the context of new energy vehicles, which are often exposed to various environmental conditions such as moisture, road salts, and pollutants, corrosion resistance is of utmost importance. For example, in coastal areas where the air is humid and contains salt particles, vehicles made with materials that are not corrosion - resistant can experience rapid degradation. However, vehicles with industrial aluminium components can withstand these harsh conditions, ensuring the long - term structural integrity and safety of the vehicle. A recent study on the durability of NEV components in coastal regions found that aluminium - alloy battery enclosures showed no signs of significant corrosion after five years of exposure, while those made of traditional steel had visible rust and degradation.
2.3 High Thermal Conductivity
Industrial aluminium has high thermal conductivity, with a value of around 200 - 237 W/(m·K) depending on the alloy. This property makes it an excellent material for heat management in new energy vehicles.
In NEVs, the battery and various electronic components generate heat during operation. If this heat is not dissipated effectively, it can lead to a decrease in battery performance, reduced lifespan of electronic components, and even pose safety risks. Aluminium's high thermal conductivity allows it to quickly transfer heat away from these critical components. For example, heat sink aluminum profiles are commonly used in battery packs and electronic control units (ECUs) to dissipate heat, ensuring that these components operate within the optimal temperature range. In high - performance electric vehicles, advanced heat sink designs using aluminum alloys can reduce the operating temperature of battery cells by 10 - 15°C, significantly improving battery efficiency and lifespan.
3 Key Applications of Industrial Aluminium Profiles in New Energy Vehicles
3.1 Vehicle Body Structure
Industrial aluminium profiles are extensively used in the vehicle body structure of new energy vehicles. They are employed in the construction of the body frame, doors, roof, and other structural components. The use of aluminium profiles in the body frame helps to achieve significant weight reduction while maintaining high structural strength.
For example, many modern NEV manufacturers use aluminium space - frame structures. These structures are made up of interconnected aluminium extrusions, which are lighter than traditional steel frames but offer comparable or even better crash - worthiness. The use of aluminium profile t slot in the assembly of these structures allows for easy modular construction, improving the manufacturing efficiency and reducing production costs. A leading electric vehicle manufacturer reported a 30% reduction in body - in - white weight by using an aluminum space - frame structure, along with a 20% improvement in torsional stiffness, which enhances the vehicle's handling and safety.
3.2 Battery Systems
The battery is the heart of a new energy vehicle, and industrial aluminum plays a vital role in battery systems. Aluminium is used in the manufacturing of battery enclosures, battery trays, and other battery - related components.
Battery enclosures made of aluminium provide excellent protection for the battery cells. They are lightweight, yet strong enough to withstand external impacts and vibrations. Aluminium battery trays are also crucial for supporting the battery modules and ensuring proper heat dissipation. In addition, the use of aluminium in battery systems helps to improve the overall energy density of the vehicle by reducing the weight of the battery - related components. A case in point is that some luxury electric vehicles use aluminum - alloy battery enclosures that are not only 40% lighter than traditional steel enclosures but also offer better thermal management capabilities, contributing to a higher - energy - density battery pack.
3.3 Heat Sink Aluminum Profile for Thermal Management
As mentioned earlier, thermal management is crucial for the optimal performance of new energy vehicles. Heat sink aluminum profiles are specifically designed to enhance heat dissipation. These profiles are often finned structures that increase the surface area available for heat transfer.
In the battery pack, heat sink aluminum profiles are placed in close proximity to the battery cells. They absorb the heat generated by the cells during charging and discharging processes and transfer it to the surrounding environment. Similarly, in electronic components such as inverters and chargers, heat sink aluminum profiles are used to keep the components cool, preventing overheating and ensuring their reliable operation. A recent innovation in heat sink design involves the use of micro - channel heat sinks made of aluminum, which can increase the heat transfer efficiency by up to 30% compared to traditional finned heat sinks.
3.4 Aluminium Profile T Slot in Modular Components
Aluminium profile t slot is a key feature in the modular design of new energy vehicles. These t - slots are extruded into the aluminium profiles and allow for the easy attachment of various components.
In the manufacturing of NEVs, modular components can be quickly assembled using bolts or other fasteners that fit into the t - slots. This modular design approach not only speeds up the production process but also makes it easier to replace or upgrade individual components. For example, in the interior of a new energy vehicle, modular consoles and storage units can be easily installed using aluminium profile t - slots, providing flexibility in vehicle customization. A major NEV manufacturer reported a 25% reduction in production time by adopting a modular design approach using aluminum profiles with t - slots.
4 The Manufacturing Process of Industrial Aluminium for New Energy Vehicles
4.1 Extrusion Process
The extrusion process is a fundamental step in the production of industrial aluminium profiles. First, the raw aluminium material, usually in the form of billets, is pre - heated to a suitable temperature, typically between 450 - 550°C. The billets are then placed into a large hydraulic press, which can exert pressures ranging from 1000 - 5000 tons.
The press forces the softened aluminium through a die, which has a specific cross - sectional shape corresponding to the desired profile. This process allows for the creation of complex shapes with high precision. For example, the aluminium profile t slot is formed during the extrusion process by designing the die with the appropriate t - shaped opening. The extruded profiles are then cooled, usually by air or water quenching, and further processed, such as by straightening and cutting to the required lengths. Advanced extrusion technologies, such as hydrostatic extrusion, are being developed to produce aluminium profiles with even better surface quality and dimensional accuracy.
4.2 Surface Treatment
After extrusion, industrial aluminium often undergoes surface treatment to enhance its properties. One of the most common surface treatment methods is anodizing. Anodizing involves creating an oxide layer on the surface of the aluminium through an electrochemical process. This oxide layer not only improves the corrosion resistance of the aluminium but also gives it a more aesthetically pleasing appearance. The thickness of the anodized layer can be controlled, typically ranging from 5 - 25 microns, depending on the application requirements.
Another popular surface treatment is powder coating. Powder coating involves applying a dry powder to the surface of the aluminium and then curing it under heat, usually at temperatures between 180 - 220°C. This process results in a durable, colorful, and scratch - resistant finish. In the case of new energy vehicles, surface - treated aluminium components not only look better but also last longer, withstanding the rigors of daily use. Some powder - coated aluminum parts in NEVs can maintain their color and appearance for more than 10 years under normal driving conditions.
5 Market Trends and Future Prospects
5.1 Current Market Demand
The current market demand for industrial aluminum in the new energy vehicle sector is booming. With the increasing global push towards electric mobility, more and more automakers are investing in the production of NEVs. As a result, the demand for lightweight, high - performance materials like industrial aluminum has been on the rise.
According to market research, the global demand for aluminium in the automotive industry is expected to grow at a compound annual growth rate (CAGR) of over 5% in the coming years, with the new energy vehicle segment being a major driver of this growth. This growth is driven by factors such as stricter emission regulations, the need for longer - range NEVs, and the continuous improvement of aluminium manufacturing technologies. For example, in China, the world's largest NEV market, the demand for automotive aluminum is projected to double in the next five years, mainly due to the expansion of the NEV production capacity.
5.2 Technological Innovations
In the field of industrial aluminum for new energy vehicles, there are several ongoing technological innovations. One area of focus is the development of new aluminium alloys. Researchers are constantly working on creating alloys with improved strength - to - weight ratios, better corrosion resistance, and enhanced thermal properties.
For example, some new alloys are being designed to have even higher strength while maintaining the lightweight advantage of aluminium. These alloys could potentially be used in more demanding applications in NEVs, such as high - stress structural components. In addition, improvements in manufacturing processes, such as the development of more efficient extrusion techniques and advanced surface treatment methods, are also driving innovation in the industry. A new semi - solid forming process for aluminum alloys has been developed, which can produce components with higher strength and better surface finish, reducing the need for post - processing.
5.3 Future Developments
Looking ahead, the future of industrial aluminum in new energy vehicles is very promising. As the technology of NEVs continues to advance, the demand for industrial aluminum will only increase. We can expect to see even more widespread use of aluminium in all aspects of NEV design, from the body to the powertrain.
Moreover, with the development of autonomous driving technology, the need for lightweight, reliable materials like industrial aluminum will become even more critical. Aluminium's properties make it an ideal choice for the construction of sensor housings and other components in autonomous vehicles. Additionally, as recycling technologies improve, the use of recycled aluminium in new energy vehicles is likely to increase, further reducing the environmental impact of the automotive industry. Some experts predict that by 2030, recycled aluminum will account for 30 - 40% of the total aluminum used in NEVs, contributing to a more sustainable automotive manufacturing process.
6 Conclusion
In conclusion, industrial aluminum is an indispensable material in the new energy vehicle industry. Its lightweight, corrosion - resistant, and high - thermal - conductivity properties make it a perfect fit for multiple applications in NEVs, from the vehicle body structure to the battery system and thermal management components. The manufacturing processes of industrial aluminum, including extrusion and surface treatment, have also evolved to meet the high - quality requirements of the automotive industry.
As the market demand for new energy vehicles continues to grow, and with ongoing technological innovations, the future of industrial aluminum in this field looks extremely bright. At aluinno, we are proud to be part of this exciting industry, providing high - quality industrial aluminum products that contribute to the development and advancement of new energy vehicles. We look forward to further collaborating with industry partners to drive the innovation and growth of the new energy vehicle secto