Unveiling the New Patent: Revolutionary Aluminum Alloy for Battery Shells
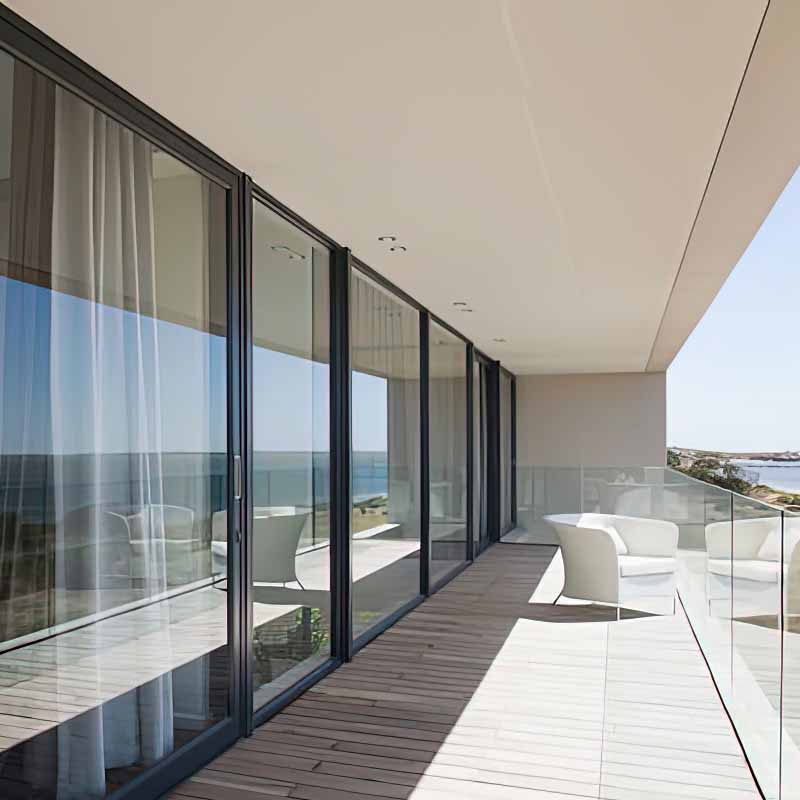
Introduction
Highlight aluminum's significance in modern industries.
Introduce the new patent - a revolutionary aluminum alloy for battery shells.
Alloy Basics
Composition: Key elements like copper, magnesium, and silicon.
Properties: High strength, good electrical and thermal conductivity, corrosion - resistance.
Manufacturing Process
Raw material selection and melting.
Different manufacturing methods for enclosures: extrusion, metal enclosure casting, die - casting.
Advantages over Traditional Materials
Lightweight yet strong.
Enhanced thermal and electrical conductivity.
Superior corrosion resistance.
Applications and Market Prospects
Electric vehicle batteries, consumer electronics, energy storage systems.
Future Trends
Research on alloy properties and manufacturing.
Impact on the industry.
Conclusion
Summarize the alloy's advantages and potential.
Mention aluinno's role in this development.
1 Introduction
In modern industries, aluminum has emerged as a material of utmost significance. Its unique combination of properties makes it a preferred choice across a wide range of applications. This blog post delves into a new patent - a revolutionary aluminum alloy designed specifically for battery shells. We will explore the alloy's characteristics, the advantages it brings over traditional materials, its compatibility with different enclosure manufacturing methods such as aluminum extrusion enclosure, aluminum case metal enclosure, and die cast aluminum enclosure, and its extensive applications in various industries. By the end, you'll have a comprehensive understanding of how this new alloy is set to transform the battery shell manufacturing landscape.
2 The Rising Star - Aluminum in Modern Industries
Aluminum has become a cornerstone material in modern manufacturing due to its remarkable properties. It is lightweight, which is crucial for applications where weight reduction is a priority, such as in the automotive and aerospace industries. For instance, in the automotive sector, the use of aluminum components helps to improve fuel efficiency and reduce emissions. Additionally, aluminum is highly durable and resistant to corrosion. This makes it suitable for use in harsh environments, whether it's the salty air near the coast or the extreme temperatures in industrial settings.
In the electronics industry, aluminum's excellent thermal and electrical conductivity make it an ideal material for heat sinks and electrical components. Its malleability also allows for easy shaping and forming, enabling the production of complex - shaped parts. As industries continue to evolve and demand more efficient and sustainable materials, aluminum's importance is only set to grow. This growth has paved the way for the development of new and innovative aluminum - based products, such as the new alloy for battery shells.
3 Decoding the New Patent: Aluminum Alloy for Battery Shells
3.1. Composition and Properties
The newly patented aluminum alloy for battery shells is a carefully engineered blend of aluminum and several other elements. Key alloying elements may include copper, magnesium, and silicon. Copper is added to enhance the alloy's strength and hardness. It forms intermetallic compounds with aluminum, which contribute to the overall mechanical properties of the alloy. Magnesium, on the other hand, improves the alloy's corrosion resistance and also has a positive impact on its strength - to - weight ratio. Silicon is added to improve the alloy's fluidity during casting processes, which is essential for the production of high - quality battery shells with complex shapes.
This alloy exhibits high strength, which is crucial for protecting the delicate components inside the battery. It can withstand external forces and impacts without deforming or cracking, ensuring the safety and integrity of the battery. Moreover, it has good electrical conductivity, which is vital for efficient charge and discharge processes in the battery. Additionally, the alloy has excellent thermal conductivity, allowing for effective heat dissipation. This is especially important as batteries tend to generate heat during operation, and proper heat management is essential for maintaining optimal battery performance and lifespan.
3.2. Manufacturing Process
The manufacturing process of this new aluminum alloy for battery shells is a multi - step and precise operation. It begins with the selection of high - quality raw materials. The aluminum and alloying elements are sourced from reliable suppliers to ensure consistent quality. The raw materials are then melted in a furnace under carefully controlled conditions. Temperature, time, and the order of adding the alloying elements are all critical factors that can affect the final properties of the alloy.
After melting, the molten alloy is either cast into ingots or directly fed into the manufacturing process for the production of battery shells. In the case of aluminum extrusion enclosure production, the molten alloy is forced through a die with a specific cross - sectional shape. This process allows for the creation of long, continuous profiles with uniform dimensions. For aluminum case metal enclosure and die cast aluminum enclosure, the molten alloy is poured into molds with the desired shape. The die - casting process, in particular, is highly efficient for producing complex - shaped parts with high precision and dimensional accuracy. Quality control measures are implemented at every stage of the manufacturing process to ensure that the final product meets the strictest standards.
4 Advantages over Traditional Materials
4.1. Lightweight yet Strong
When compared to traditional materials used for battery shells, such as steel, the new aluminum alloy offers a significant advantage in terms of weight. Steel is much denser than aluminum, which means that a steel - made battery shell would be much heavier. In applications like electric vehicles, where reducing weight is crucial for improving energy efficiency and increasing the vehicle's range, the lightweight nature of the aluminum alloy is a game - changer. Despite its low weight, the aluminum alloy maintains high strength. It can withstand the same or even higher levels of stress as traditional materials, ensuring that the battery shell provides adequate protection for the battery components.
4.2. Enhanced Thermal and Electrical Conductivity
The new aluminum alloy has superior thermal and electrical conductivity compared to many traditional materials. In batteries, efficient heat dissipation is essential to prevent overheating, which can lead to reduced battery performance and lifespan. The high thermal conductivity of the aluminum alloy allows heat to be quickly transferred away from the battery cells, keeping the battery at an optimal operating temperature. This not only improves the battery's performance but also extends its lifespan.
In terms of electrical conductivity, the alloy enables faster and more efficient charge and discharge processes. This is particularly important for high - power applications, such as electric vehicles and energy storage systems, where quick charging and discharging are highly desirable. The improved electrical conductivity reduces energy losses during these processes, making the battery more efficient.
4.3. Superior Corrosion Resistance
Corrosion is a major concern for battery shells, as it can compromise the integrity of the shell and ultimately damage the battery. The new aluminum alloy has been designed to have excellent corrosion resistance. The addition of elements like magnesium and the proper surface treatment enhance its ability to resist corrosion in various environments. Whether it's exposed to moisture, chemicals, or extreme temperatures, the aluminum alloy - made battery shell can maintain its structural integrity for a longer period. This is in contrast to some traditional materials that may corrode relatively quickly, leading to the need for frequent replacements and increased costs.
5 Aluminum Extrusion Enclosure: A Perfect Match
5.1. Extrusion Process and Features
The aluminum extrusion process is a versatile manufacturing method for creating battery enclosures. In this process, a billet of aluminum alloy is heated to a suitable temperature and then forced through a die under high pressure. The die has a specific cross - sectional shape, which determines the shape of the extruded profile. This process allows for the production of battery enclosures with a wide variety of shapes and sizes, including those with complex internal and external geometries.
One of the key features of aluminum extrusion enclosures is their high dimensional accuracy. The extrusion process can produce profiles with tight tolerances, ensuring a perfect fit for the battery components. Additionally, the extruded profiles have a smooth surface finish, which not only improves the appearance of the battery enclosure but also reduces the risk of damage to the battery due to sharp edges or rough surfaces. Another advantage of aluminum extrusion enclosures is their high strength - to - weight ratio. The extrusion process aligns the grain structure of the aluminum alloy, which enhances its mechanical properties.
5.2. Compatibility with the New Alloy
The new aluminum alloy for battery shells is highly compatible with the aluminum extrusion process. Its chemical composition and physical properties make it suitable for being extruded through dies. The alloy's good fluidity during the extrusion process ensures that it can fill the die cavities completely, resulting in high - quality extruded profiles. The combination of the new alloy and the extrusion process allows for the production of battery enclosures that are both lightweight and strong. The high thermal and electrical conductivity of the alloy are also retained during the extrusion process, further enhancing the performance of the battery enclosure.
6 Aluminum Case Metal Enclosure: Durability Redefined
6.1. Metal Enclosure Characteristics
Aluminum case metal enclosures are known for their durability and protective capabilities. They provide a robust outer layer for the battery, shielding it from physical damage, dust, and moisture. The metal enclosure can withstand impacts and vibrations, which is crucial in applications where the battery may be subject to rough handling or movement, such as in portable electronic devices or electric vehicles. Aluminum case metal enclosures also offer good electromagnetic shielding properties, which is important for preventing interference with other electronic components.
6.2. The New Alloy's Contribution
The new aluminum alloy significantly enhances the performance of aluminum case metal enclosures. Its high strength improves the enclosure's ability to withstand external forces, making it more durable. The alloy's corrosion resistance ensures that the enclosure remains in good condition over a long period, even in harsh environments. The improved thermal and electrical conductivity of the alloy also benefits the aluminum case metal enclosure. It allows for better heat dissipation, which can prevent the battery from overheating, and enables more efficient electrical connections, improving the overall performance of the battery.
7 Die Cast Aluminum Enclosure: Precision and Efficiency
7.1. Die - Casting Process
The die - casting process is a highly efficient method for producing aluminum enclosures. In this process, the molten aluminum alloy is injected into a die cavity under high pressure. The die is typically made of steel and consists of two halves that are clamped together. Once the molten alloy has filled the die cavity, it cools and solidifies, taking on the shape of the die. The die - casting process is capable of producing complex - shaped parts with high precision and dimensional accuracy. It is also suitable for high - volume production, making it an ideal choice for manufacturing battery enclosures on a large scale.
7.2. Synergy with the New Patent
The new aluminum alloy works in perfect synergy with the die - casting process. Its low melting point and good fluidity make it easy to inject into the die cavity. The alloy's ability to solidify quickly ensures a high production rate. The high strength and other desirable properties of the alloy are maintained after die - casting, resulting in high - quality battery enclosures. The use of the new alloy in die - casting can also reduce the occurrence of defects such as porosity and shrinkage, improving the overall quality of the final product.
8 Applications and Market Prospects
8.1. Electric Vehicle Batteries
The new aluminum alloy for battery shells has a huge potential in the electric vehicle (EV) battery market. In EVs, the battery is one of the most critical components, and its performance directly affects the vehicle's range, efficiency, and safety. The lightweight nature of the aluminum alloy can help to reduce the overall weight of the battery pack, which in turn improves the vehicle's energy efficiency and increases its range. The high strength and corrosion resistance of the alloy ensure the safety and durability of the battery, even under the harsh conditions of daily use.
As the demand for electric vehicles continues to grow globally, the market for battery shells made from this new alloy is expected to expand significantly. Automakers are constantly looking for ways to improve the performance of their EVs, and the use of this advanced aluminum alloy can give them a competitive edge.
8.2. Consumer Electronics
In the consumer electronics industry, the new aluminum alloy can also play a vital role. With the increasing demand for smaller, lighter, and more powerful electronic devices such as smartphones, tablets, and laptops, the need for high - performance battery shells is on the rise. The lightweight and strong nature of the alloy make it suitable for use in these portable devices. It can help to reduce the weight of the device while still providing adequate protection for the battery.
The alloy's excellent thermal and electrical conductivity also benefit consumer electronics. It can improve the heat dissipation of the battery, preventing the device from overheating during extended use. The enhanced electrical conductivity can also lead to faster charging times and better overall battery performance.
8.3. Energy Storage Systems
Energy storage systems, such as those used in renewable energy applications like solar and wind power, also stand to benefit from the new aluminum alloy. These systems require reliable and durable battery shells to store and release energy efficiently. The high strength and corrosion resistance of the alloy ensure the long - term stability of the battery in various environmental conditions.
The lightweight nature of the alloy can also be an advantage in energy storage systems, especially in applications where the battery needs to be transported or installed in remote locations. The improved thermal and electrical conductivity can enhance the performance of the energy storage system, making it more efficient and reliable.
9 Future Trends and Developments
9.1. Research and Innovation
The development of new aluminum alloys for battery shells is an ongoing process. Researchers are constantly exploring ways to further optimize the properties of the alloy. This may involve the addition of new alloying elements or the development of new manufacturing processes. For example, future research may focus on improving the alloy's recyclability, as sustainability becomes an increasingly important factor in material selection. There may also be efforts to develop alloys with even higher strength - to - weight ratios or enhanced thermal and electrical conductivity.
9.2. Industry Impact
The introduction of this new aluminum alloy patent is likely to have a significant impact on the aluminum industry and related sectors. It can drive the development of new manufacturing technologies and processes, as companies strive to make the most of the alloy's properties. In the battery manufacturing industry, it may lead to the production of more efficient and reliable batteries, which can in turn accelerate the adoption of electric vehicles and renewable energy storage systems. The new alloy may also open up new market opportunities for aluminum producers and manufacturers of battery enclosures.
10 Conclusion
In conclusion, the new patent for the aluminum alloy for battery shells represents a significant advancement in the field of battery technology. Its unique combination of properties, including high strength, lightweight, excellent thermal and electrical conductivity, and superior corrosion resistance, make it a superior choice compared to traditional materials. The compatibility of the alloy with different enclosure manufacturing methods, such as aluminum extrusion enclosure, aluminum case metal enclosure, and die cast aluminum enclosure, further expands its application potential.
As we look to the future, the new alloy is expected to play a crucial role in various industries, especially in electric vehicles, consumer electronics, and energy storage systems. aluinno, with its commitment to innovation and quality, is proud to be part of this exciting development in the aluminum materials space. We look forward to contributing further to the advancement of this technology and bringing more high - quality aluminum - based products to the market. Stay tuned for more updates on our latest developments!