Unveiling the Pivotal Role of Aluminum Alloys in Europe's 2025 Industrial Landscape
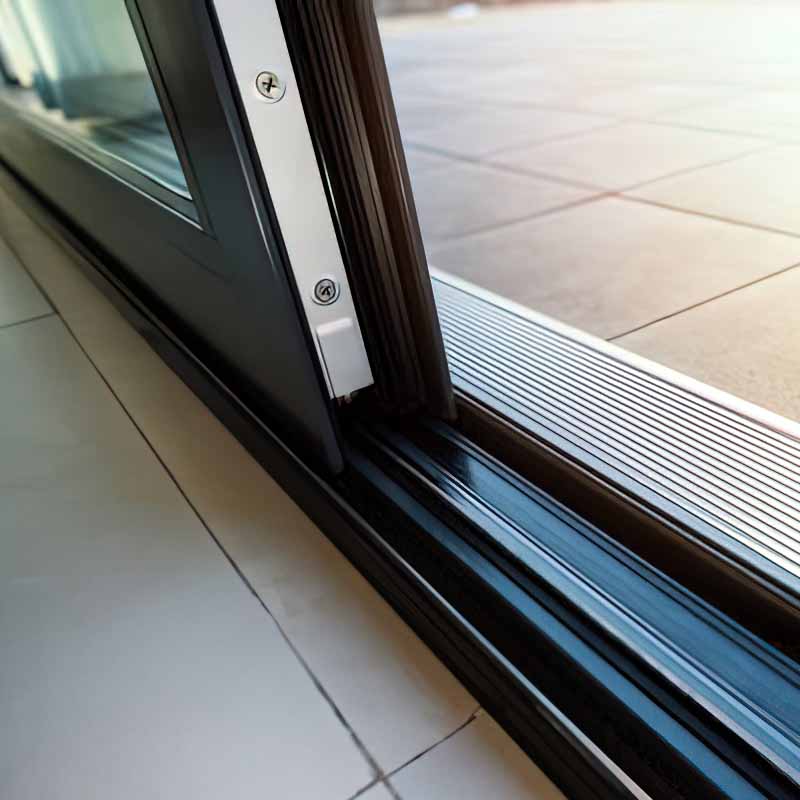
-
Introduction
Significance of aluminum alloys in modern industry due to unique properties like high strength - to - weight ratio.
Focus on their role in achieving Europe's 2025 industrial goals related to sustainability, energy efficiency, and innovation.
-
Aluminum Alloy Basics
Composition (aluminum + other elements) and properties (lightweight, strong, corrosion - resistant).
Two main types: wrought alloys (processed mechanically) and cast alloys (formed by pouring molten metal).
-
Applications
In construction (structural and decorative profiles, curtain walls for energy - efficiency).
In kitchens (cabinets, countertops, sinks for hygiene and durability).
In automotive, aerospace, and industrial machinery for lightweighting, high - performance needs.
-
European 2025 Goals
Contribution to sustainability (recycling, energy - efficiency, reducing carbon footprint).
Role in technological innovation (R&D for new alloys and applications).
-
Challenges and Solutions
Market competition, cost pressures, and technological hurdles.
Strategies like cost - reduction, R&D, and product differentiation.
-
Conclusion
Recap of applications and future prospects.
Introduction to Aluinno as a leading aluminum alloy industry player
1. Introduction
1.1 Significance of Aluminum Alloys in Modern Industry
In modern industry, aluminum alloys have emerged as materials of utmost importance. Their unique combination of properties, such as high strength - to - weight ratio, excellent corrosion resistance, and good thermal and electrical conductivity, has made them indispensable across a wide range of sectors. From construction to automotive, aerospace to electronics, aluminum alloys are driving innovation and enhancing the performance of countless products.
1.2 Focus on Europe's 2025 Industrial Goals
This article centers on the crucial role aluminum alloys play in achieving Europe's 2025 industrial goals. As Europe aims to boost sustainability, enhance energy efficiency, and foster technological innovation, aluminum alloys are set to be at the forefront, enabling industries to meet these ambitious targets.
2. Aluminum Alloy Basics
2.1 Composition and Properties
Aluminum alloys are primarily composed of aluminum, which is the third - most abundant element in the Earth's crust. To enhance its properties, other elements such as copper, magnesium, silicon, and zinc are added. This results in alloys with a remarkable set of characteristics. They are lightweight, which is a significant advantage in applications where reducing weight is crucial, like in the automotive and aerospace industries. At the same time, they offer high strength, making them suitable for structural applications. Their corrosion resistance ensures a long service life, reducing maintenance costs, especially in harsh environments.
2.2 Types of Aluminum Alloys
There are two main types of aluminum alloys: wrought alloys and cast alloys. Wrought alloys are processed through mechanical working methods like rolling, forging, and extrusion. These alloys are known for their high strength and are commonly used in applications such as aircraft structures, automotive components, and construction profiles. Cast alloys, on the other hand, are formed by pouring molten metal into molds. They are often used in applications where complex shapes are required, such as engine blocks in the automotive industry and decorative elements in construction.
3. Applications in Construction
3.1 Aluminium Construction Profiles
3.1.1 Structural Applications
Aluminium construction profiles are extensively used in the structural framework of buildings. They serve as beams, columns, and frames, providing the necessary strength and stability. Their high strength - to - weight ratio allows for the construction of large - span structures with reduced material usage, which not only cuts down on construction costs but also speeds up the building process. For example, in high - rise buildings in major European cities like London and Frankfurt, aluminum alloy profiles are used to create lightweight yet sturdy frameworks that can withstand high winds and seismic forces.
3.1.2 Decorative Purposes
In addition to their structural role, aluminium construction profiles are highly valued for decorative purposes. They are used in the design of window and door frames, providing an aesthetically pleasing and modern look. The ability to be easily extruded into various shapes and finishes, such as anodized or powder - coated, allows architects and designers to create unique and stylish facades. In many contemporary European buildings, aluminum alloy profiles are used to create intricate decorative elements, adding a touch of elegance to the overall architecture.
3.2 Curtain Wall Aluminum Profile
3.2.1 Function and Design in Modern Architecture
Curtain wall aluminum profiles play a crucial role in modern architecture. These profiles form the framework for curtain walls, which are non - structural exterior walls that enclose a building. They are designed to withstand wind loads, thermal expansion, and contraction. The design of curtain wall aluminum profiles is highly sophisticated, with features such as multi - chambered sections for improved insulation and weather - tightness. In iconic buildings like the Shard in London, the curtain wall aluminum profiles are not only functional but also contribute to the building's striking visual appearance.
3.2.2 Contribution to Energy Efficiency
One of the most significant advantages of curtain wall aluminum profiles is their contribution to energy efficiency. With the addition of thermal breaks and high - performance glazing, these profiles can significantly reduce heat transfer through the building envelope. This helps in maintaining a comfortable indoor temperature, reducing the need for excessive heating or cooling, and ultimately lowering energy consumption. In line with Europe's strict energy - efficiency regulations, curtain wall aluminum profiles are an essential component in sustainable building design.
4. Applications in the Kitchen
4.1 Aluminium Kitchen Section
4.1.1 Cabinets and Storage Units
Aluminium kitchen sections are increasingly popular in the design of kitchen cabinets and storage units. Aluminum's resistance to moisture makes it an ideal material for kitchens, where humidity can be a problem. Cabinets made of aluminum are not only durable but also easy to clean, maintaining their appearance over time. In modern European kitchen designs, aluminum - framed cabinets with sleek lines and modern finishes are becoming a common sight, offering both functionality and style.
4.1.2 Countertops and Sinks
Aluminum is also used in the production of kitchen countertops and sinks. Aluminum countertops are known for their strength and resistance to scratches and stains. They can be customized to fit any kitchen layout and come in a variety of finishes. Aluminum sinks, on the other hand, are lightweight, durable, and offer excellent corrosion resistance. They are available in different shapes and sizes, catering to the diverse needs of homeowners and professional kitchens.
4.2 Hygiene and Durability Advantages
In a kitchen environment, hygiene is of utmost importance. Aluminum is non - porous, which means it does not harbor bacteria or mold, making it a hygienic choice for kitchen applications. Its durability ensures that kitchen components made of aluminum can withstand the rigors of daily use, from frequent cleaning to heavy - duty cooking activities. This long - lasting nature of aluminum in the kitchen not only provides value for money but also reduces the need for frequent replacements, contributing to a more sustainable lifestyle.
5. Aluminum Alloys in Other Key Industries
5.1 Automotive Industry
5.1.1 Lightweighting for Fuel Efficiency
In the automotive industry, aluminum alloys are playing a crucial role in the pursuit of fuel efficiency. By replacing heavier steel components with aluminum alloys, car manufacturers can significantly reduce the weight of vehicles. This reduction in weight leads to improved fuel economy and lower emissions. For example, many European car manufacturers, such as Audi and BMW, are increasingly using aluminum alloys in the construction of vehicle bodies, engine blocks, and suspension components. This not only makes the cars more fuel - efficient but also enhances their performance and handling.
5.1.2 Safety and Performance Enhancements
Aluminum alloys also contribute to the safety and performance of vehicles. Their high strength allows for the design of more robust vehicle structures, which can better protect passengers in the event of a collision. Additionally, the use of aluminum alloys in braking systems and wheels can improve braking performance and reduce unsprung weight, leading to better handling and overall vehicle performance.
5.2 Aerospace Industry
5.2.1 Meeting Stringent Requirements
The aerospace industry has some of the most stringent requirements when it comes to materials, and aluminum alloys have been a mainstay for decades. In aircraft construction, aluminum alloys are used in the manufacture of the fuselage, wings, and engine components. These alloys must meet strict standards for strength, weight, and fatigue resistance. The development of advanced aluminum alloys, such as those with high - strength - to - weight ratios and improved corrosion resistance, has been essential in the evolution of modern aircraft.
5.2.2 Technological Advancements
Ongoing research and development in the aerospace industry have led to significant technological advancements in aluminum alloy applications. New manufacturing techniques, such as additive manufacturing (3D printing), are being used to create complex aluminum alloy components with improved performance. These advancements not only enhance the efficiency and safety of aircraft but also open up new possibilities for the design and construction of future aerospace vehicles.
5.3 Industrial Machinery
5.3.1 Machinery Frames and Components
In industrial machinery, aluminum alloys are used in the construction of frames and components. Their high strength and corrosion resistance make them suitable for use in harsh industrial environments. For example, in the manufacturing of heavy - duty machinery used in the mining and construction industries, aluminum alloy frames can provide the necessary strength while reducing the overall weight of the equipment. This makes the machinery more portable and easier to operate.
5.3.2 Customization for Specific Needs
One of the advantages of aluminum alloys in industrial machinery is their ability to be customized to meet specific needs. Through alloying and heat - treatment processes, the properties of aluminum alloys can be tailored to suit different applications. This allows manufacturers to design machinery components that are optimized for performance, durability, and cost - effectiveness.
6. European 2025 Industrial Goals and Aluminum Alloys
6.1 Sustainability and Environmental Considerations
6.1.1 Recycling and Energy Efficiency
Aluminum is highly recyclable, and recycling aluminum requires only a fraction of the energy needed to produce it from raw materials. In Europe, where sustainability is a key focus, the recycling of aluminum alloys is an important part of the circular economy. By recycling aluminum, industries can reduce their carbon footprint and dependence on virgin materials. The energy - efficient nature of aluminum production and recycling aligns with Europe's goals of reducing greenhouse gas emissions and promoting sustainable industrial practices.
6.1.2 Reducing Carbon Footprint
The use of aluminum alloys in various industries also helps in reducing the overall carbon footprint. In the construction industry, the energy - efficient properties of aluminum - based building materials, such as curtain wall profiles, contribute to lower energy consumption in buildings. In the transportation sector, the lightweight nature of aluminum - alloy components in vehicles and aircraft leads to reduced fuel consumption and emissions. This reduction in carbon emissions is crucial for Europe to meet its climate - change mitigation targets.
6.2 Technological Innovation and Development
6.2.1 Research and Development Efforts
Europe is investing heavily in research and development related to aluminum alloys. Universities, research institutions, and industries are collaborating to develop new alloys with improved properties. These efforts are focused on enhancing the strength, corrosion resistance, and recyclability of aluminum alloys. For example, research is underway to develop aluminum alloys that can withstand higher temperatures, which would open up new applications in the aerospace and automotive industries.
6.2.2 New Applications and Product Development
The continuous technological innovation in aluminum alloys is leading to the development of new applications and products. In the field of renewable energy, aluminum alloys are being used in the construction of wind turbine blades and solar panel frames. These applications take advantage of aluminum's lightweight and durable properties. In the electronics industry, aluminum alloys are being explored for use in heat sinks and electronic enclosures, where their thermal conductivity and corrosion resistance are highly valued.
7. Challenges and Solutions
7.1 Market Competition and Cost Pressures
The aluminum alloy industry faces intense market competition, especially from other materials such as steel and plastics. The price of aluminum can also be volatile, affected by factors such as raw material costs, global supply and demand, and currency fluctuations. These cost pressures can make it challenging for manufacturers to maintain profitability. To address these challenges, companies are focusing on cost - reduction strategies, such as optimizing production processes, improving supply chain management, and developing new, more cost - effective alloys.
7.2 Technological Hurdles
Despite the many advantages of aluminum alloys, there are still technological hurdles to overcome. For example, some aluminum alloys have limited formability, which can make it difficult to manufacture complex - shaped components. There are also challenges in joining aluminum alloys, as traditional welding methods can sometimes lead to defects. To overcome these hurdles, research is being conducted on new forming and joining techniques, such as friction stir welding, which offers better results for aluminum alloys.
7.3 Solutions and Strategies
To tackle the challenges in the aluminum alloy industry, a combination of strategies is being employed. Collaboration between industries, research institutions, and governments is crucial for driving innovation and addressing common problems. Investment in research and development to improve alloy properties and manufacturing processes is also essential. Additionally, companies are focusing on product differentiation, offering high - quality, customized aluminum alloy products to meet the specific needs of customers.
8. Conclusion
8.1 Recap of Aluminum Alloy Applications
Aluminum alloys have a wide range of applications across various industries in Europe, from construction and automotive to aerospace and industrial machinery. Their unique properties make them essential for meeting the demands of modern industry, including strength, lightweight, corrosion resistance, and recyclability.
8.2 Future Outlook
Looking ahead, the future of aluminum alloys in Europe's industrial landscape is promising. With continued technological innovation and a focus on sustainability, aluminum alloys are expected to play an even more significant role in achieving Europe's 2025 industrial goals. New applications and products are likely to emerge, further expanding the market for aluminum alloys.
8.3 Mention of Aluinno
Aluinno is a leading player in the aluminum alloy industry, committed to providing high - quality aluminum products. With a focus on innovation and customer satisfaction, Aluinno offers a diverse range of aluminum products, including aluminium construction profiles, curtain wall aluminum profiles, and aluminium kitchen sections. Our products are known for their superior quality, reliability, and customization options, making us a trusted partner for various industries in Europe.