3D Printing Empowers Aluminum
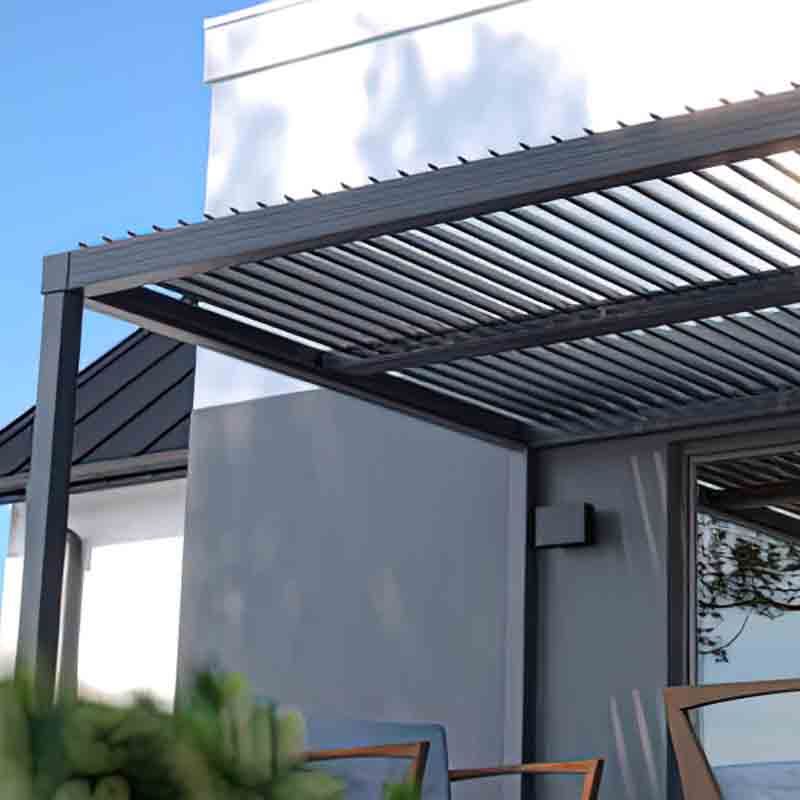
Outline
In this blog post, we'll explore the revolutionary impact of 3D printing technology on aluminum and aluminum profiles production. Firstly, we'll introduce how 3D printing enables the one - time molding of complex aluminum structures, contrasting it with traditional manufacturing. Then, we'll focus on its applications in aerospace precision components and medical implants, analyzing the advantages in terms of customization, precision, and performance. Finally, we'll discuss the future directions for improving aluminum material properties to better serve these high - tech fields.
3D Printing Aluminum: Ushering in a New Era of Customized Metal Manufacturing
In recent years, 3D printing technology has been making waves across various industries, and its integration with aluminum and aluminum profiles production is opening up a whole new realm of possibilities. This article delves deep into how 3D printing is transforming the way we manufacture aluminum products.
1. The Power of 3D Printing in Aluminum Production
1.1. One - time Molding of Complex Structures
Traditional aluminum manufacturing processes, such as casting and machining, often face limitations when it comes to creating complex geometries. Casting may introduce defects like porosity, and machining requires multiple steps and significant material waste. In contrast, 3D printing technology, specifically techniques like selective laser melting (SLM) and electron beam melting (EBM), allows for the precise deposition of aluminum powder layer by layer, enabling the one - time molding of intricate and complex structures.
For example, in the production of certain aerospace components with internal cooling channels, 3D printing can create the channels within the aluminum part during the build process itself, eliminating the need for post - processing drilling and ensuring optimal flow characteristics. This not only saves time but also enhances the overall performance of the component.
1.2. Comparison with Traditional Manufacturing
When compared to traditional methods, 3D printing offers several distinct advantages. In terms of design freedom, it allows engineers to conceive and produce parts with geometries that were previously impossible or extremely difficult to manufacture. Traditional manufacturing is constrained by tooling and setup requirements, but 3D printing only needs a digital model.
Material utilization is another area where 3D printing shines. While traditional machining can result in up to 90% material waste in some cases, 3D printing builds the part from the ground up, using only the necessary amount of aluminum powder, reducing waste significantly. Additionally, the lead time for prototyping and small - batch production is much shorter with 3D printing, enabling companies to get their products to market faster.
Year | Global 3D Printed Aluminum Market Sales (in billions of US dollars) |
---|---|
2024 | 2.08 |
2031 | 13.08 |
CAGR (2025 - 2031) | 30.5% |
2. Applications in Aerospace Precision Components
2.1. Customization and Performance Enhancement
The aerospace industry demands high - precision, lightweight, and reliable components. 3D printing of aluminum and aluminum profiles meets these requirements admirably. For instance, aircraft engine brackets can be custom - designed and printed to fit the specific requirements of each engine model, optimizing load distribution and reducing weight.
Moreover, the ability to integrate multiple functions into a single printed part is a game - changer. In the design of satellite components, 3D printing allows for the incorporation of thermal management features, structural reinforcements, and electrical conduits all within one piece, reducing the number of assembled parts and potential failure points.
2.2. Meeting Stringent Quality Standards
Aerospace components must adhere to extremely strict quality and safety standards. 3D printing technology has evolved to meet these challenges. Advanced quality control systems are integrated into the printing process to monitor parameters such as powder bed density, laser power, and layer thickness. Post - printing inspection techniques, including X - ray tomography and ultrasonic testing, ensure that each part is free from defects and meets the required mechanical and metallurgical properties.
The use of high - performance aluminum alloys in 3D printing, such as aluminum - lithium alloys, further enhances the strength - to - weight ratio of the components, making them suitable for the demanding aerospace environment.
3. Applications in Medical Implants
3.1. Tailored Solutions for Patients
In the medical field, 3D printing of aluminum and aluminum profiles is revolutionizing implant design. For orthopedic implants, surgeons can now use patient - specific data, such as CT scans, to design implants that perfectly match the patient's anatomy. This personalized approach reduces surgical time, minimizes post - operative complications, and improves the overall success rate of the implant.
For example, in hip replacement surgeries, a 3D - printed aluminum femoral head can be customized to fit the patient's femoral canal geometry, providing a more natural fit and better load transfer. The same principle applies to cranial implants, where the complex curvature of the skull can be replicated accurately, enhancing the cosmetic and functional outcomes.
3.2. Biocompatibility and Material Innovation
Biocompatibility is of utmost importance for medical implants. While pure aluminum is not suitable for direct implantation due to potential toxicity issues, researchers are developing new aluminum - based alloys with improved biocompatibility. These alloys incorporate elements like titanium and zirconium to enhance the body's acceptance of the implant.
The surface modification of 3D - printed aluminum implants is also a key area of research. By applying coatings or treatments that promote cell adhesion and tissue growth, such as hydroxyapatite coatings, the implants can integrate more smoothly with the surrounding tissues, further improving their long - term performance.
4. Future Directions for Aluminum Material Properties Improvement
4.1. Alloy Development for 3D Printing
To fully leverage the potential of 3D printing in high - tech applications, continuous alloy development is crucial. Scientists are working on new aluminum alloys specifically formulated for 3D printing processes. These alloys aim to have better flowability during powder deposition, improved solidification characteristics, and enhanced mechanical properties after printing.
For example, the addition of rare earth elements to aluminum alloys can refine the microstructure, increasing strength and ductility. This will enable the production of even more complex and high - performance 3D - printed aluminum components in the future.
4.2. Performance Optimization in Extreme Environments
As applications in aerospace and other demanding fields expand, the need to optimize aluminum material properties in extreme environments becomes evident. Research is focused on improving the high - temperature resistance, corrosion resistance, and fatigue resistance of 3D - printed aluminum components.
Techniques such as heat treatment and surface alloying are being explored to enhance these properties. By subjecting 3D - printed aluminum parts to specific heat treatment regimes, their microstructure can be modified to withstand higher temperatures and cyclic loading, making them suitable for long - term use in harsh conditions.
5. Conclusion
In conclusion, 3D printing technology is truly revolutionizing the world of aluminum and aluminum profiles production. It has enabled the creation of complex structures, opened up new applications in aerospace and medical fields, and spurred innovation in aluminum material properties. As the technology continues to mature and research progresses, we can expect even more remarkable achievements in the future, further solidifying 3D printing's position as a key enabler of customized metal manufacturing.