Aluminum's Progressive Journey in New Energy Vehicle Lightweight Evolution
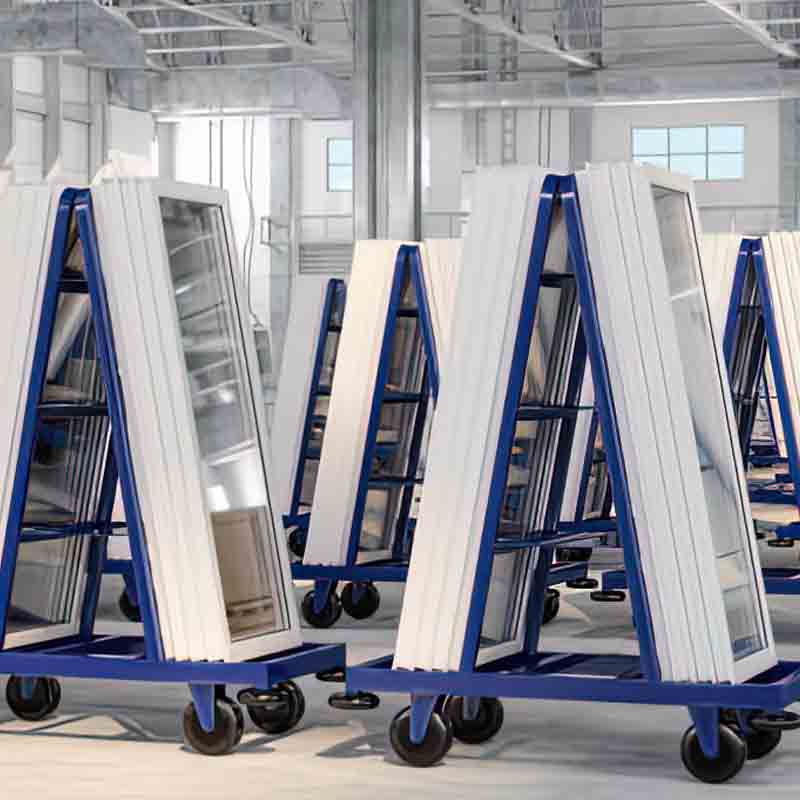
Outline
This blog post will focus on the significant role of aluminum and aluminum profiles in the lightweighting trend of new energy vehicles. Firstly, we'll explore how the increasing demand for longer range drives up the use of aluminum. Then, we'll look into the technical breakthroughs that enable aluminum to replace traditional steel in vehicle body frames and components, along with cost optimization strategies. Additionally, we'll address the challenges of ensuring compatibility with other components like batteries. Finally, we'll consider future prospects and the continued evolution of aluminum in this sector.
The Advancement Road of Aluminum in the Lightweight Process of New Energy Vehicles
In the contemporary automotive landscape, especially within the realm of new energy vehicles, the pursuit of lightweight construction has become a dominant force. Aluminum and aluminum profiles have emerged as key players in this transformative journey.
1. The Surging Demand for Aluminum Driven by Range Requirements
With the growing popularity of new energy vehicles, consumers are increasingly concerned about the driving range on a single charge. Every kilogram saved in vehicle weight can potentially translate into additional kilometers of travel. This has led to a remarkable surge in the demand for aluminum. Its relatively low density, approximately one-third that of steel, makes it an ideal candidate for reducing overall vehicle mass. In high-end electric vehicles, manufacturers are progressively substituting heavier steel components with aluminum ones. For instance, the use of aluminum in the body-in-white can significantly cut down the vehicle's weight, directly contributing to an extended driving range. This trend is not only driven by consumer preferences but also by the fierce competition among automakers to offer vehicles with superior performance and longer range.
Year |
Estimated Market Size (in billions of US dollars) |
Growth Rate (CAGR) |
2020 |
4.8 |
- |
2021 |
5.5 |
14.6% |
2022 |
6.3 |
14.5% |
2023 |
7.2 |
14.3% |
2024 |
8.3 |
15.3% |
2025 |
9.6 |
15.7% |
2026 |
11.1 |
15.6% |
2027 |
12.8 |
15.3% |
2028 |
14.7 |
14.8% |
2029 |
16.9 |
14.9% |
2030 |
19.3 |
14.2% |
2. Technological Breakthroughs in Aluminum Application
2.1. Full-scale Replacement in Vehicle Structures
To fully leverage aluminum's potential, significant technological advancements have been made. In the past, the use of aluminum in vehicle body frames was limited due to concerns about its structural integrity and manufacturability. However, recent innovations have overcome these hurdles. Advanced forming techniques, such as hydroforming and extrusion, now allow for the production of complex aluminum profiles with high strength and precision. These can be seamlessly integrated into the vehicle's structure, replacing traditional steel components. For example, the chassis and suspension systems, which were once predominantly made of steel, are now seeing a gradual shift towards aluminum-based designs. This not only reduces weight but also improves the vehicle's handling and dynamic performance.
2.2. Component-level Substitution
Beyond the body frame, aluminum is making inroads in various vehicle components. Engine parts, for instance, are being redesigned using aluminum alloys to achieve better heat dissipation and weight reduction. The cylinder heads and blocks made of aluminum offer improved thermal conductivity compared to their steel counterparts, enhancing engine efficiency. Additionally, interior components like seat frames and door panels are also being fabricated from aluminum, further contributing to the overall weight reduction goal. This component-level substitution requires meticulous engineering to ensure that the performance and durability of the parts are not compromised.
3. Cost Optimization Strategies
While aluminum offers undeniable advantages in terms of weight reduction, its cost has been a major concern. To make it a more viable option, manufacturers are exploring several cost optimization paths.
3.1. Process Improvements
One approach is to refine the manufacturing process. By optimizing casting, machining, and assembly techniques, waste can be minimized, and production efficiency can be enhanced. For example, new casting methods that reduce porosity and improve the quality of aluminum components can lower the rejection rate, thereby reducing overall costs. Advanced machining processes that require fewer tool changes and shorter setup times also contribute to cost savings.
3.2. Economies of Scale
Another crucial factor is achieving economies of scale. As the demand for aluminum in new energy vehicles rises, larger production volumes can drive down unit costs. This requires cooperation between different players in the supply chain, from aluminum producers to automotive manufacturers. By streamlining procurement, production, and distribution, costs can be effectively controlled. For instance, joint ventures or long-term partnerships can be established to ensure a stable supply of aluminum at a competitive price.
4. Compatibility Challenges with Other Components
The integration of aluminum into new energy vehicles is not without its challenges, especially when it comes to compatibility with other components.
4.1. Interaction with Batteries
In electric vehicles, the battery pack is a critical component. Aluminum's use in proximity to the battery needs to be carefully considered due to potential galvanic corrosion issues. When aluminum comes into contact with other metals in the presence of an electrolyte (such as the battery's electrolyte), it can trigger a corrosion reaction that may affect the performance and safety of the vehicle. Therefore, proper insulation and surface treatments are essential to prevent such interactions. Researchers are working on developing coatings and barrier materials that can effectively isolate aluminum from the battery components while maintaining its lightweight and conductive properties.
4.2. Joining and Assembly with Different Materials
Since vehicles are made up of multiple materials, the joining and assembly of aluminum with other materials like steel and composites pose significant challenges. Traditional welding methods that work well for steel may not be suitable for aluminum, as they can cause defects and weaken the joint. Friction stir welding has emerged as a promising solution for aluminum-aluminum joints, but when it comes to mixed material assemblies, new techniques such as riveting, adhesive bonding, and hybrid joining methods are being explored. These need to ensure both mechanical strength and long-term durability to withstand the rigors of vehicle operation.
5. Future Prospects
Looking ahead, the role of aluminum in new energy vehicles is set to expand even further.
5.1. New Alloy Developments
Researchers are constantly striving to develop new aluminum alloys with enhanced properties. These alloys aim to offer even better strength-to-weight ratios, improved corrosion resistance, and higher formability. For example, the addition of rare earth elements to aluminum alloys is being studied to achieve these goals. Such alloys could enable the production of even lighter and more durable vehicle components, further pushing the boundaries of lightweight design.
5.2. Recycling and Sustainability
With increasing environmental awareness, the recyclability of aluminum becomes a significant advantage. In the future, more efforts will be focused on improving the recycling infrastructure and processes to ensure that aluminum can be reused efficiently. This not only reduces the environmental impact but also provides a cost-effective source of material for the automotive industry. Additionally, sustainable manufacturing practices that minimize energy consumption and waste generation during aluminum production will gain prominence.
6. Conclusion
In conclusion, the journey of aluminum and aluminum profiles in the lightweight process of new energy vehicles is filled with opportunities and challenges. The demand for longer driving range is propelling the use of aluminum, while technological breakthroughs, cost optimization, and efforts to overcome compatibility issues are paving the way for its wider adoption. As we look to the future, continued innovation in aluminum technology and its application will be crucial in shaping the next generation of new energy vehicles. It's an exciting time for the aluminum industry, and the potential for growth and transformation is immense.