The Shift to Low - Carbon Aluminum: An Industry's Sustainability Path
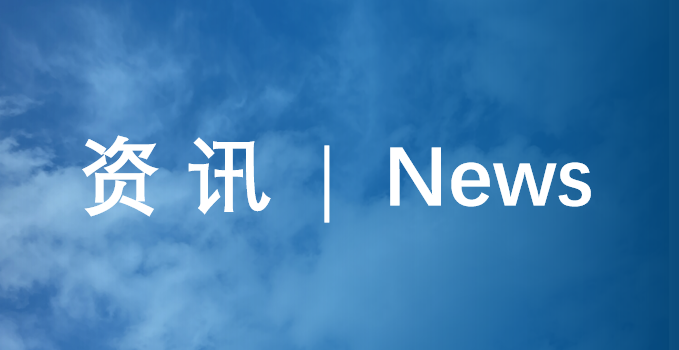
Introduction
In the global manufacturing arena, the aluminum industry is a key player. It has a wide - ranging impact, from constructing lightweight and strong structures in buildings to enabling fuel - efficient components in automotive and aerospace sectors. However, aluminum production has long been associated with high energy consumption and substantial greenhouse gas emissions.
The production of aluminum is energy - intensive. Extracting aluminum from bauxite ore and the subsequent smelting process require large amounts of electricity, much of which has historically come from fossil fuels like coal and natural gas. This reliance has made the aluminum industry a significant contributor to global carbon emissions. With the growing emphasis on climate change mitigation, the shift towards low - carbon aluminum production has become an essential environmental and strategic move for the industry.
This article will comprehensively explore this shift, covering the reasons behind it, the driving innovations, industry collaboration and policy support, aluminum's role in the circular economy, as well as the challenges and future prospects.
The Need for Low - Carbon Aluminum Production
1. The Environmental Impact of Traditional Aluminum Production
Traditional aluminum production has a significant environmental footprint. According to a report by the International Energy Agency (IEA), aluminum production globally accounts for around 3.6% of all industrial electricity consumption. This is a substantial figure considering the scale of global industrial activities.
Moreover, the industry is responsible for about 1.1% of global CO₂ emissions, as reported by the World Resources Institute (WRI). These emissions occur throughout the production process, from bauxite mining to the final smelting and refining stages. For instance, the use of carbon - based anodes in smelting releases large amounts of CO₂ into the atmosphere. A specific case is the aluminum smelting plants in some developing countries where the reliance on coal - fired power for electricity generation has led to relatively high emissions levels compared to those in regions with cleaner energy sources.
2. Aluminum's Potential in Reducing Carbon Footprints
Despite the current environmental challenges, aluminum has properties that make it crucial in reducing carbon footprints. Its recyclability is a standout feature. As noted in a study published in the journal "Resources, Conservation and Recycling," aluminum can be recycled indefinitely without losing its essential properties. This means recycled aluminum can replace virgin aluminum in many applications, significantly cutting down on energy - intensive primary production.
In sectors like the automotive industry, aluminum's lightweight nature offers great advantages. A report from the Aluminium Association indicates that using aluminum in vehicle manufacturing can lead to substantial fuel savings and, consequently, lower CO₂ emissions. For example, Ford's F - 150 pickup truck has increasingly incorporated aluminum in its body construction. By reducing the vehicle's weight, it has improved fuel efficiency, thereby reducing CO₂ emissions over the vehicle's lifecycle. Similarly, in aerospace, aluminum components contribute to lighter aircraft, reducing fuel consumption during flights. Airbus, for instance, uses aluminum alloys in a significant portion of its aircraft structures, which helps in achieving better fuel economy and lower emissions.
Innovations Driving the Shift to Low - Carbon Aluminum
1. Inert Anode Technology
Inert anode technology is a major breakthrough in aluminum smelting. As stated in research published in "Metallurgical and Materials Transactions B," in traditional smelting, carbon anodes are used, and they react with oxygen during the process to produce CO₂. In contrast, inert anodes are made from materials that do not participate in the electrochemical reaction like carbon anodes. This could potentially eliminate the CO₂ emissions associated with the anode reaction.
Companies such as Rio Tinto and Alcoa are leading the development of this technology. Rio Tinto has been conducting pilot - scale tests of its inert anode technology in some of its smelting plants. In one of their test facilities, they have achieved promising results in terms of reducing anode - related CO₂ emissions. However, there are technical challenges. For example, finding materials that can endure the harsh smelting conditions while maintaining their inert properties over long periods is complex, as reported by industry - focused websites like Aluminium Insider.
2. Use of Renewable Energy
The integration of renewable energy sources into aluminum production is vital for low - carbon aluminum.
Hydropower
Many aluminum smelters in regions rich in water resources, like Canada and Norway, utilize hydropower. According to a case study on the Norwegian aluminum industry by the Energy Research Centre of the Netherlands, some smelters in Norway are powered almost entirely by hydropower, resulting in very low greenhouse gas emissions compared to those relying on fossil - fuel - based electricity. For example, the Hydro Aluminium plant in Norway is a prime example. It sources a large portion of its electricity from nearby hydroelectric power plants. This has not only reduced its carbon footprint significantly but also provided a stable and cost - effective energy source for its aluminum production operations.
Solar and Wind Power
Solar power and wind power are also being explored. As per an article in Renewable Energy World, in areas with high solar irradiance or strong wind resources, solar farms and wind turbines can be installed near aluminum smelters. However, the intermittent nature of these energy sources poses challenges. Energy storage solutions, like batteries, are needed to ensure a continuous power supply to the smelters. In the case of an aluminum smelter in Arizona, USA, which is in a region with abundant solar energy, the company has started to install a small - scale solar power generation system on - site. Although it currently only supplies a fraction of the total energy needs, it is a step towards integrating solar power into the production process.
3. Aluminum Recycling and the Circular Economy
Aluminum recycling is fundamental to the low - carbon aluminum strategy. As reported in the "Journal of Cleaner Production," the energy required for recycling aluminum is only about 5% of that for primary aluminum production.
Closed - Loop Production Systems
Major aluminum producers are focusing on establishing closed - loop production systems. For example, Novelis, a global leader in aluminum rolling and recycling, has implemented a closed - loop system in some of its production facilities. They collect scrap aluminum from various sources, including end - of - life products like beverage cans and automotive parts. This scrap is then reprocessed into high - quality aluminum coils that can be used to make new products. In their plant in North America, they have significantly increased the amount of recycled aluminum used in their production, reducing the need for virgin bauxite ore and minimizing waste.
Product Design for Recycling
Product designers are now considering recyclability from the start. As highlighted in a design - focused magazine, Designboom, products are being designed for easier disassembly and recycling at the end of their life cycle. Apple, for instance, has been making efforts in designing its products with recyclability in mind. In their latest iPhone models, they have used more recyclable aluminum alloys and designed the product in a way that makes it easier to separate the aluminum components for recycling at the end of its life.
Traditional Aluminum Production vs. Low - Carbon Aluminum Production
Comparison |
Traditional Aluminum Production |
Low - Carbon Aluminum Production |
Energy Source |
Fossil Fuels (Coal, Natural Gas) |
Renewable Energy (Hydropower, Wind, Solar) and Recycled Aluminum |
Greenhouse Gas Emissions |
High |
Significantly Reduced (Close to Zero in Ideal Cases) |
Cost |
Variable, Influenced by Energy Prices and Raw Material Availability |
More Stable in the Long - Run due to Reduced Dependence on Fossil Fuels and Recycling Economics |
Environmental Impact |
Considerable, with High Energy Consumption and Emissions |
Minimized through Renewable Energy Use, Recycling, and Lower Emissions Technologies |
Industry Collaboration and Policy Support
1. The Role of Industry Associations
Industry associations play a crucial role in promoting low - carbon aluminum production. The International Aluminium Institute (IAI), for example, serves as a platform for global aluminum producers to collaborate and share best practices. It sets industry standards for environmental performance, quality control, and sustainable production, as reported on its official website.
The IAI conducts research and development projects in collaboration with its members. These projects, as mentioned in their annual reports, focus on areas like improving energy efficiency, reducing emissions, and enhancing recyclability. For example, in a joint project with several major aluminum producers, the IAI has been researching new methods to improve the energy efficiency of the smelting process. By pooling resources and knowledge, the industry can accelerate the adoption of low - carbon technologies.
2. Government Policies and Regulations
Government policies are important drivers for the transition.
Emissions Trading Systems (ETS)
Emissions Trading Systems (ETS) are being implemented in many countries. According to a report by the European Commission on the EU - ETS, in an ETS, companies are allocated emissions allowances. If a company emits less than its allocation, it can sell the surplus. This creates an economic incentive for aluminum producers to reduce emissions. In the European Union, aluminum companies like Alcoa Europe have been actively participating in the EU - ETS. To meet the emissions targets and potentially earn from selling surplus allowances, they have invested in cleaner production technologies and energy - efficient measures, which has led to a reduction in their overall carbon footprint.
Carbon Taxes
Carbon taxes are another policy tool. As stated in a research paper by the World Bank, by imposing a tax on carbon emissions, companies are encouraged to invest in cleaner technologies or switch to low - carbon energy sources. In Canada, for example, the introduction of carbon taxes has influenced aluminum producers in British Columbia. Some companies have started to explore alternative energy sources like hydropower more seriously as a way to reduce their carbon tax burden and move towards low - carbon production.
Subsidies for Sustainable Production
Governments also provide subsidies for sustainable production. For instance, as reported in a local government economic development report, some governments offer grants or tax breaks to aluminum producers using a certain percentage of renewable energy in their operations. In Germany, the government has provided subsidies to aluminum companies that invest in solar power generation for their production facilities. This has encouraged more companies to consider integrating renewable energy into their production processes.
The Role of Aluminum in the Circular Economy
1. The Concept of the Circular Economy in the Aluminum Industry
The circular economy, based on reducing waste, reusing materials, and recycling resources, is highly relevant to the aluminum industry. Aluminum's recyclability makes it an ideal material for a circular economy model. Instead of the traditional linear model of "extract - produce - use - dispose," the circular economy promotes a closed - loop system where aluminum products are recycled at the end of their life cycle and re - enter the production process.
2. Examples of Aluminum in the Circular Economy
Building and Construction
In the building and construction industry, aluminum is widely used in window frames, curtain walls, and roofing. As buildings are renovated or demolished, the aluminum can be recycled. As described in an article in "Architecture Today," recycled aluminum can be used to produce new building materials, reducing the need for virgin aluminum and minimizing construction waste. In the case of the Sydney Opera House renovation project in Australia, a significant amount of the aluminum components were recycled. The old aluminum was collected, processed, and then used to create new parts for the building, which not only saved costs but also had a positive environmental impact.
Packaging
The aluminum packaging industry also benefits from the circular economy. Aluminum cans, for example, have a high recycling rate. As reported on the website of the Can Manufacturers Institute, they can be recycled and back on the store shelves as new cans in as little as 60 days, conserving resources and reducing energy consumption for new can production. Coca - Cola, for instance, has been promoting the recycling of its aluminum cans globally. They have set up recycling programs in many countries, aiming to increase the recycling rate of their cans and reduce the environmental impact of their packaging.
Challenges and Future Prospects
1. Challenges in the Shift to Low - Carbon Aluminum
High Initial Investment
One of the main challenges in transitioning to low - carbon aluminum production is the high initial investment. Implementing new technologies like inert anode technology or building renewable energy infrastructure for smelters requires substantial capital. Smaller aluminum producers may struggle to afford these investments, which could slow down the industry's transformation, as pointed out in an analysis by a financial research firm. For example, a small - scale aluminum smelter in Southeast Asia was interested in installing a solar power generation system but was deterred by the high upfront cost of purchasing the solar panels, inverters, and battery storage systems.
Technological Complexity
The development and implementation of low - carbon technologies are complex. For example, inert anode technology still faces technical issues related to material durability and performance in the smelting environment, as mentioned in a technical review in "Light Metals." Integrating renewable energy sources with existing production processes also requires sophisticated control systems to manage the intermittent nature of solar and wind power. A case in point is an aluminum smelter in Europe that attempted to integrate wind power into its production process. They faced challenges in synchronizing the power supply from the wind turbines with the variable power demands of the smelting process due to the intermittent nature of wind.
Market Acceptance and Competition
There are challenges related to market acceptance and competition. Consumers may not be fully aware of the environmental benefits of low - carbon aluminum products, affecting market demand. As stated in a market research report by Nielsen, consumer awareness and perception play a crucial role in the success of sustainable products. In the case of some aluminum - based consumer products, like aluminum furniture, consumers may not be willing to pay a premium for products made from low - carbon aluminum due to lack of awareness. Additionally, in a competitive global market, aluminum producers may be hesitant to invest in low - carbon production if they think their competitors are not, fearing a cost disadvantage. For example, in the highly competitive aluminum extrusion market, some small - to - medium - sized producers are reluctant to invest in new low - carbon production technologies as they fear being undercut by competitors who are not making such investments.
2. Future Prospects for Low - Carbon Aluminum
Technological Advancements
Despite the challenges, the future of low - carbon aluminum production looks promising. Continued technological advancements are expected to overcome current obstacles. For example, research into new materials for inert anodes may lead to more durable and cost - effective options, as anticipated in a research preview in "Advanced Materials." Improvements in energy storage technology will also make it easier to integrate solar and wind power into aluminum production. In the coming years, new battery technologies are expected to be developed that can store larger amounts of energy more efficiently, which will be beneficial for aluminum smelters relying on intermittent renewable energy sources.
Growing Market Demand
As environmental awareness grows among consumers and businesses, the demand for low - carbon aluminum is likely to increase. In sectors like automotive and aerospace, where sustainability is increasingly important in purchasing decisions, the market for low - carbon aluminum components is expected to expand. This will create economic incentives for aluminum producers to invest more in low - carbon production methods, as predicted in a forecast by an industry analyst firm. For example, as more automotive manufacturers commit to reducing their carbon footprints, they will increasingly demand low - carbon aluminum for their vehicle production, which will drive the growth of this market segment.
Global Collaboration and Policy Harmonization
In the future, greater global collaboration and policy harmonization are expected. As climate change is a global issue, countries and industries need to work more closely. Standardizing environmental regulations and emissions targets across regions, as advocated by the United Nations Framework Convention on Climate Change (UNFCCC), will facilitate the growth of the low - carbon aluminum market. For instance, if all major aluminum - producing countries adopt similar emissions standards, it will create a level playing field for producers worldwide. This will encourage more companies to invest in low - carbon production technologies without fearing competitive disadvantages in different markets.
In conclusion, the shift to low - carbon aluminum production is a complex but necessary journey for the aluminum industry. Through continuous innovation, industry collaboration, and policy support, the industry can overcome challenges and fully embrace sustainability, Aluinno Aluminum contributing to a greener future.