2025: The Expanding Horizon of the Aluminum Industry
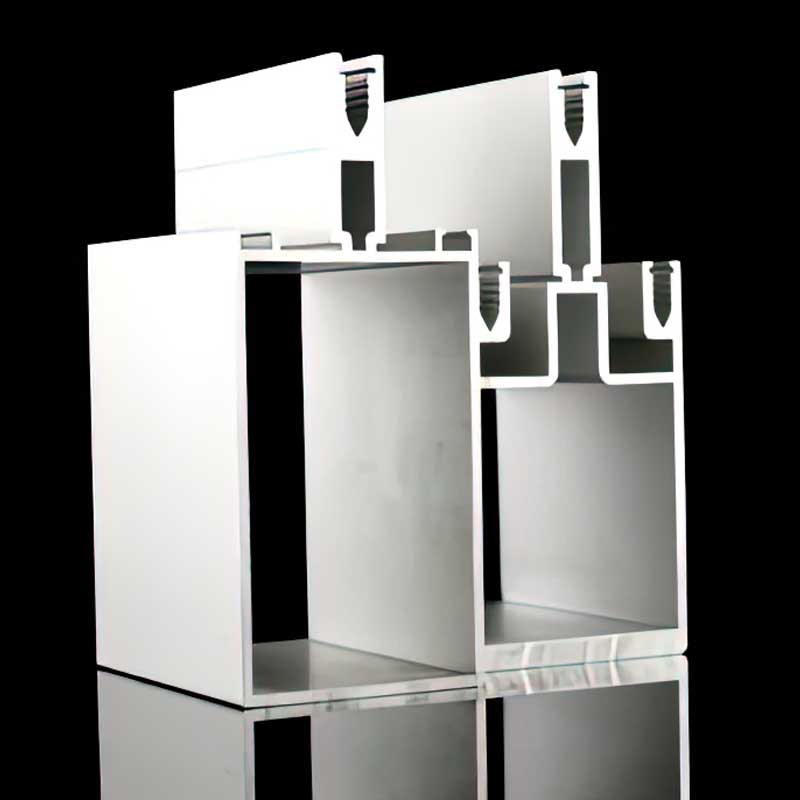
OUTLINE
1. Introduction
As we look ahead to 2025, the aluminum industry is poised on the brink of significant expansion. Aluminum, renowned for its unique combination of light weight, durability, and recyclability, has become an indispensable material in modern manufacturing. From the soaring skyscrapers that define our cityscapes to the sleek automobiles that zip along our highways, and even the handheld devices that have become extensions of ourselves, aluminum plays a crucial role.
The demand for aluminum has been on a steady upward trajectory, driven by multiple factors. In the construction sector, the push for energy-efficient and sustainable buildings has led to an increased preference for aluminum windows, doors, and curtain walls. Its corrosion resistance and aesthetic appeal make it a top choice for architects and builders alike. In transportation, the quest for fuel efficiency and reduced emissions has spurred the use of aluminum in automotive and aerospace applications. Lighter vehicles not only consume less fuel but also offer better performance and handling.
This blog post will delve into the various aspects of the aluminum industry's expansion in 2025. We will explore the latest trends in aluminum extrusion, the growing market for aluminum profiles, and the innovative applications in different sectors. Whether you're a professional in the industry, an investor looking for opportunities, or simply curious about the materials that shape our world, this post aims to provide valuable insights. So, let's embark on this journey and discover what the future holds for aluminum.
2. The Backbone of Expansion: Aluminium Profiles
2.1 Definition and Production Process
Aluminum profiles, also known as extrusion profiles, are the building blocks of the aluminum industry. They are created through the extrusion process, which involves forcing a billet of aluminum through a die to obtain a specific cross-sectional shape. This process is akin to squeezing toothpaste out of a tube, but on a much larger and more precise scale.
The raw material, typically aluminum ingots, is first heated to a specific temperature range to make it malleable. The heated billet is then placed in a container and pushed by a ram through the die. The die, which is custom-designed for each profile shape, imparts the desired form to the aluminum as it passes through. After extrusion, the profiles undergo various post-processing steps such as cooling, straightening, and cutting to the required lengths.
The extrusion process parameters, such as temperature, speed, and pressure, play a crucial role in determining the quality and properties of the final product. For instance, a higher extrusion speed can increase production throughput but may lead to surface defects and reduced mechanical strength if not carefully controlled. On the other hand, a slower extrusion speed allows for better grain structure formation and improved material integrity, albeit at a lower production rate. Manufacturers constantly strive to optimize these parameters to strike a balance between productivity and quality.
2.2 Diverse Applications
The versatility of aluminum profiles is what makes them indispensable across multiple industries. In the construction sector, aluminum window frames and curtain walls have become synonymous with modern architecture. Aluminium casement window, for example, offer excellent thermal insulation, soundproofing, and weather resistance. Their sleek design and durability enhance the aesthetic appeal of buildings while providing long-term functionality. Aluminium kitchen section, such as cabinet frames and countertops, are also gaining popularity due to their resistance to moisture, stains, and easy maintenance.
In transportation, aluminum profiles are a key enabler of lightweighting. In automobiles, they are used in the body structure, chassis components, and interior fittings. Lighter vehicles not only reduce fuel consumption but also offer better acceleration and handling. In the aerospace industry, where every gram matters, aluminum alloys are used to manufacture fuselage frames, wings, and other structural parts. The high strength-to-weight ratio of aluminum allows aircraft to carry more payload while consuming less fuel, thereby reducing operating costs.
Industrial equipment manufacturers also rely heavily on aluminum profiles. They are used to construct machinery housings, conveyor systems, and robotic arms. The excellent machinability of aluminum allows for precise fabrication and customization, enabling the production of complex and high-performance equipment. Additionally, the non-magnetic and non-sparking properties of aluminum make it suitable for applications in sensitive environments such as electronics manufacturing and chemical processing plants.
3. Extrusion Profiles: Shaping the Future
3.1 Technology Advancements
The extrusion process, a cornerstone of the aluminum industry, is undergoing remarkable transformations. Traditional extrusion methods are being enhanced with cutting-edge technologies to meet the evolving demands of various sectors.
Precision extrusion has emerged as a game-changer. With industries such as electronics and aerospace demanding components with micron-level tolerances, manufacturers are investing in state-of-the-art equipment and techniques. For instance, advanced extrusion presses equipped with high-precision control systems can maintain temperature variations within a fraction of a degree, ensuring consistent material flow and dimensional accuracy. This level of precision allows for the production of intricate profiles used in high-end electronics, where even the slightest deviation can impact performance.
Multi-chamber extrusion technology is another breakthrough. By enabling the simultaneous formation of multiple hollow chambers within a single profile, it significantly increases the material's strength-to-weight ratio. This is particularly beneficial in the automotive and construction industries, where lightweight yet structurally robust components are prized. In automotive manufacturing, multi-chamber extrusions are used to fabricate chassis components and body frames, reducing vehicle weight and enhancing fuel efficiency without compromising safety.
Compared to traditional extrusion, these new technologies offer substantial improvements in efficiency and quality. While traditional extrusion might have required multiple post-processing steps to achieve the desired precision, modern precision extrusion minimizes the need for such additional operations, saving both time and cost. In terms of quality, the enhanced control over the extrusion process parameters results in profiles with superior mechanical properties, surface finish, and dimensional stability, opening up new possibilities for their application in critical industries.
3.2 Market Trends and Demands
The market for extrusion profiles is witnessing a paradigm shift, driven by changing consumer preferences and industry requirements. Customization has become the watchword, with customers across sectors seeking tailored aluminum profiles to meet their specific needs.
In the construction industry, architects and builders are increasingly specifying unique window and door profiles to achieve distinctive aesthetic and functional designs. For example, energy-efficient buildings demand aluminum window frames with complex thermal break profiles that can reduce heat transfer and enhance insulation. According to industry reports, the demand for custom aluminum profiles in construction is projected to grow at a CAGR of over 8% in the coming years, as sustainable and intelligent building concepts gain traction.
In the automotive sector, the shift towards electric vehicles (EVs) has spurred the demand for specialized extrusion profiles. EVs require lightweight components to maximize battery range, and aluminum extrusion profiles are ideally suited for this purpose. Battery enclosures, for instance, need to be both strong and thermally conductive to ensure the safe and efficient operation of the battery pack. The automotive aluminum extrusion market is expected to expand by over 10% annually, fueled by the rapid growth of the EV market.
Industrial machinery manufacturers also rely on customized extrusion profiles to build equipment that is more efficient, compact, and durable. From robotic arms in manufacturing plants to conveyor systems in logistics, the demand for high-performance aluminum profiles is on the rise. A recent survey indicated that nearly 60% of industrial equipment manufacturers plan to increase their use of custom aluminum extrusions in the next three years to gain a competitive edge in the market.
Overall, the market for extrusion profiles is set to experience robust growth, underpinned by these diverse and growing demands. As industries continue to innovate and seek better materials solutions, aluminum extrusion profiles will play an increasingly central role in shaping the future of manufacturing.
4. Aluminium Casement Windows and Kitchen Sections: Specialized Applications
4.1 Aluminium Casement Windows
Aluminium casement windows have emerged as a popular choice in modern architecture, and for good reason. Their design allows for excellent ventilation and natural light intake. Unlike some other window types, casement windows can be opened wide, providing a large opening area that facilitates better air circulation. This is particularly beneficial in residential buildings, where fresh air is essential for a healthy living environment.
In terms of energy efficiency, aluminium casement windows have made significant strides. With the development of advanced thermal break technologies, heat transfer through the window frame is minimized. Thermal breaks are insulating elements that separate the interior and exterior parts of the aluminium frame, reducing thermal conduction. This means that in both hot summers and cold winters, the window helps maintain a stable indoor temperature, reducing the need for excessive heating or cooling. As a result, homeowners can enjoy lower energy bills while also contributing to environmental conservation.
Compared to traditional window materials like wood and PVC, aluminium casement windows offer distinct advantages. Wood windows, while aesthetically pleasing, require regular maintenance to prevent rotting, warping, and insect damage. They are also less energy-efficient than modern aluminium counterparts. PVC windows, on the other hand, may have good insulation properties initially, but over time, they can become brittle and discolored due to exposure to sunlight. Aluminium casement windows combine durability, with a lifespan of decades, and excellent resistance to weathering, making them a reliable choice for long-term use.
4.2 Aluminium Kitchen Sections
In the heart of every home, the kitchen, aluminium is carving out a significant niche. Aluminium kitchen sections, including cabinet frames, countertops, and shelving, are increasingly favored by homeowners and designers alike.
The kitchen environment is notoriously harsh, with high humidity levels from cooking and frequent exposure to water, food spills, and grease. Aluminium's natural resistance to moisture and corrosion makes it an ideal material for these applications. Aluminium kitchen cabinets do not swell or warp like wooden cabinets when exposed to water, ensuring long-term structural integrity. They are also easy to clean, as spills and stains can be wiped away with a simple damp cloth, without leaving any marks or damage to the surface.
From a design perspective, aluminium kitchen sections offer unparalleled flexibility. They can be fabricated into a variety of shapes and sizes to fit any kitchen layout, whether it's a compact urban apartment or a sprawling suburban home. The sleek, modern look of aluminium complements a wide range of interior design styles, from minimalist and contemporary to industrial and rustic. For example, brushed aluminium finishes provide a subtle, elegant texture, while polished aluminium can add a touch of glamour and sophistication.
Popular designs in aluminium kitchen sections include modular cabinet systems that can be easily customized and reconfigured. These systems often feature integrated storage solutions, such as pull-out drawers, corner carousels, and hidden compartments, maximizing the use of space. Additionally, aluminium countertops with built-in sinks and drainboards offer a seamless and hygienic surface for food preparation and cleanup. Whether it's a busy family kitchen or a professional chef's workspace, aluminium kitchen sections are designed to meet the demands of modern living.
5. Challenges and Opportunities Ahead
As the aluminum industry gears up for expansion in 2025, it faces a complex web of challenges and opportunities.
On the challenges front, one of the foremost issues is the volatility in raw material prices. Aluminum production is highly dependent on the availability and cost of bauxite and electricity. Fluctuations in global bauxite supply, influenced by factors such as geopolitical tensions and mining regulations in major producing countries, can lead to significant price swings. For instance, in recent years, disruptions in bauxite shipments from regions like Australia and Guinea have sent shockwaves through the industry, causing aluminum prices to spike. Additionally, the energy-intensive nature of aluminum smelting means that changes in electricity prices, whether due to shifts in energy policies or fuel costs, can have a profound impact on production costs.
Technological innovation, while a driver of growth, also presents hurdles. The development and adoption of new extrusion technologies, such as those required for high-precision and multi-chamber profiles, demand substantial investment in research and development. Many small and medium-sized enterprises in the industry struggle to allocate the necessary funds, putting them at a disadvantage in the race to stay competitive. Moreover, there is a shortage of skilled professionals with expertise in advanced aluminum processing techniques. Universities and vocational institutions have yet to fully meet the industry's demand for engineers and technicians proficient in areas like computer-aided design for extrusion dies and process optimization.
Market competition is intensifying both domestically and globally. Domestically, the industry is fragmented, with a large number of players vying for market share. This has led to price wars in some segments, eroding profit margins. In the extrusion profiles market, for example, numerous small manufacturers offer similar products at cutthroat prices, making it difficult for companies focused on quality and innovation to stand out. On the global stage, aluminum producers from emerging economies are ramping up their capacities, challenging the traditional dominance of established players. At the same time, alternative materials, such as advanced composites and high-strength plastics, pose a threat in certain applications, as they offer competing properties in terms of weight and performance.
However, amid these challenges, numerous opportunities beckon. The rapid growth of the electric vehicle (EV) market is a prime example. As governments worldwide push for decarbonization and consumers embrace cleaner transportation options, the demand for aluminum in EVs is skyrocketing. Aluminum is used in battery enclosures, electric motor housings, and vehicle frames to reduce weight and extend battery range. Industry projections suggest that by 2025, the aluminum content in an average EV could increase by over 30% compared to current levels, translating to millions of additional tons of demand.
The aerospace industry is another bright spot. With the resurgence of commercial air travel and the development of next-generation aircraft, the need for high-performance aluminum alloys is greater than ever. New aluminum-lithium alloys, which offer improved strength-to-weight ratios and corrosion resistance, are being increasingly incorporated into aircraft structures. The Boeing 787 and Airbus A350, for instance, already utilize significant amounts of these advanced alloys, and future aircraft designs are expected to follow suit.
In conclusion, the aluminum industry in 2025 stands at a crossroads. While challenges loom large, the opportunities for growth and innovation are equally compelling. By addressing the challenges head-on through strategic investments in technology and talent, and by capitalizing on emerging trends in key sectors, aluminum producers can not only weather the storm but also thrive in the years to come. As we move forward, it will be fascinating to witness how the industry adapts and evolves to meet the demands of a rapidly changing world. If you have any questions regarding aluminum technology or are seeking reliable extrusion profiles for your projects, feel free to reach out to us. Our team of experts is always ready to assist you in navigating the complex yet exciting world of aluminum.
6. Conclusion
In conclusion, the aluminum industry's expansion in 2025 holds great promise and potential. The continuous innovation in aluminum extrusion, the growing versatility of aluminum profiles, and the specialized applications in areas like aluminium casement windows and kitchen sections are driving the industry forward. However, it is not without its challenges, from volatile raw material prices to intense market competition and technological hurdles.
Yet, these challenges also present opportunities for those willing to adapt and invest in the future. The rise of electric vehicles and the resurgence of the aerospace industry offer new avenues for growth. The key lies in the industry's ability to collaborate, invest in research and development, and upskill its workforce.
As we move closer to 2025, it will be fascinating to see how the aluminum industry navigates these waters. Whether you're a builder looking for the latest in window technology, an automotive engineer seeking lightweight solutions, or a homeowner interested in a modern kitchen, aluminum will undoubtedly play a starring role.
If you have any questions regarding aluminum technology, extrusion profiles, or are looking for reliable aluminum products for your projects, our team of experts is here to assist you. Feel free to reach out and let's explore the possibilities of aluminum together.