What Happens to Aluminum Materials When They Encounter Intense Fire?
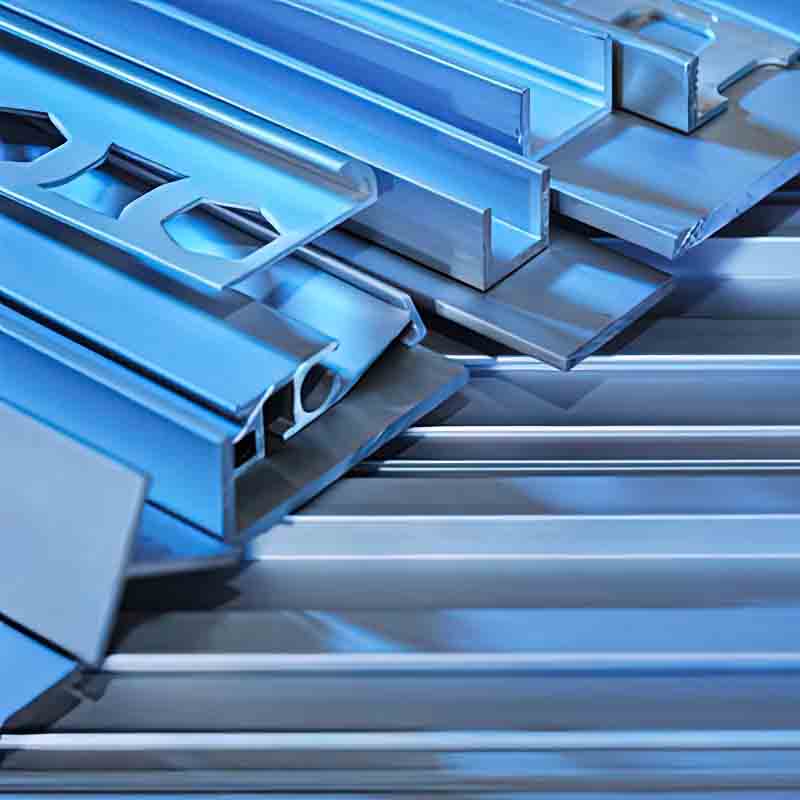
Introduction
Aluminum materials have permeated a vast array of industries, ranging from construction and automotive to aerospace and electronics. Their lightweight nature, combined with reasonable strength and excellent corrosion resistance, has made them a preferred choice for countless applications. However, when faced with the threat of intense fire, the behavior of aluminum materials becomes a critical concern. Understanding how aluminum materials react in such extreme conditions is of paramount importance for ensuring the safety of lives and property in various settings. This blog post will delve into the details of what exactly occurs when aluminum materials encounter intense fire.
Characteristics of Aluminum Materials
1. Basic Properties of Aluminum
Aluminum is a remarkable metal with several unique properties. It has a relatively low density of approximately 2.7 g/cm³, which endows it with a significant advantage in applications where weight reduction is crucial. For instance, in the aerospace industry, the use of aluminum alloys in aircraft structures helps to reduce the overall weight of the aircraft, thereby enhancing fuel efficiency and flight performance. Despite its low density, aluminum exhibits a decent level of strength, especially when alloyed with other elements. It also demonstrates good electrical and thermal conductivity, making it indispensable in electrical transmission lines and heat exchangers.
2. Advantages in Various Industries
In the construction sector, aluminum is widely utilized in the form of aluminum profiles for window and door frames, curtain walls, and structural supports. Aluminum casement windows, for example, are favored for their durability and resistance to corrosion, which helps maintain the integrity of the building envelope over time. In the automotive field, the increasing use of aluminum materials, such as extrusion aluminium and custom aluminum components, has significantly contributed to vehicle lightweighting. This not only improves fuel economy but also enhances handling and acceleration. In aerospace, high-strength and lightweight aluminum alloys are used to fabricate critical components like aircraft frames and wing spars, where every gram of weight reduction matters.
Behavior of Different Aluminum Products in Intense Fire
1. Aluminum Profiles
1.1 Industrial Aluminium Profiles
Industrial aluminium profiles are commonly used in machinery frames and conveyor structures. When exposed to intense fire, the high temperature causes the aluminum to undergo significant changes. The strength of the profile rapidly decreases as the temperature approaches and exceeds the melting point of aluminum, which is around 660°C. This leads to a loss of structural integrity, and the profile may deform or even collapse under the load it was designed to bear. For example, in an industrial plant fire, the aluminum frames supporting heavy machinery could buckle, causing the machinery to shift or become inoperable, thereby disrupting the production process and potentially endangering the safety of workers.
1.2 Custom Aluminum Profiles
Custom aluminum profiles, designed to meet specific project requirements, often have complex shapes and unique geometries. In a fire situation, these profiles may experience uneven heating due to their irregular shapes. Areas with thinner sections or sharp corners may heat up more quickly, resulting in localized overheating and premature deformation. This can have a detrimental impact on the overall functionality of the components they are part of. For instance, in a specialized manufacturing facility where custom aluminum profiles are used in precision equipment, a fire could cause the profiles to warp, leading to misalignment of the equipment and a decline in production accuracy.
2. Extrusion Aluminium
2.1 Structural Changes during Extrusion Process under Fire
Extrusion aluminium, which is formed by forcing heated aluminum through a die, has a specific microstructure that gives it its mechanical properties. When subjected to intense fire, the high temperature can alter this microstructure. The grains within the aluminum may grow and coarsen, reducing the material's strength and ductility. This is because the heat provides energy for the atoms to move and rearrange themselves, disrupting the original ordered structure. As a result, the extrusion aluminium may become more brittle and less able to withstand mechanical stresses.
2.2 Impact on Mechanical Properties
The changes in microstructure directly translate to a deterioration in the mechanical properties of extrusion aluminium. The hardness may decrease, making the material more susceptible to scratching and deformation. The tensile strength and yield strength also decline, meaning that the material can no longer support the same loads as before. In applications where extrusion aluminium is used in load-bearing structures, such as in some industrial support systems, this can lead to catastrophic failures during a fire, endangering the entire structure and any associated equipment or personnel.
3. Aluminium Casement Windows
3.1 Thermal Expansion and Its Consequences
Aluminium casement windows, a common sight in many buildings, are not immune to the effects of intense fire. As the temperature rises, the aluminum in the window frames expands. This thermal expansion can cause the frames to warp and bend, potentially breaking the glass or causing the window to become stuck in its frame. In a building fire, this can prevent the window from functioning as an emergency exit or ventilation point, trapping occupants inside and increasing the risk of smoke inhalation and heat exposure. Moreover, the deformed frames may allow fire and smoke to spread more easily between rooms or floors, compromising the fire compartmentation of the building.
3.2 Flame Resistance and Heat Transfer
Aluminum itself is not a highly flammable material, but it does conduct heat effectively. In a fire, the aluminum casement window can quickly transfer heat from the outside to the inside of the building, accelerating the spread of the fire within the room. Additionally, the heat can cause the seals around the window to degrade, further reducing the window's ability to prevent the ingress of smoke and flames. This highlights the importance of considering the fire performance of aluminum casement windows when designing and installing them in buildings.
Factors Affecting Aluminum's Response to Fire
1. Alloy Composition
1.1 Different Alloying Elements and Their Influence
The addition of various alloying elements to aluminum can significantly alter its properties in a fire. For example, copper is often added to aluminum alloys to improve their strength and hardness. However, in a fire, copper can also lower the melting point of the alloy and increase its susceptibility to oxidation. Magnesium, another common alloying element, can enhance the strength-to-weight ratio of the alloy but may also make it more reactive at high temperatures. Zinc can improve the corrosion resistance of the alloy but can have complex effects on its fire behavior, depending on the concentration and other alloying elements present.
1.2 How Alloy Ratios Affect Fire Resistance
The ratio of alloying elements in an aluminum alloy plays a crucial role in determining its fire resistance. A higher proportion of certain elements may enhance specific properties but could also have drawbacks in a fire situation. For instance, an alloy with a relatively high copper content may have better initial strength but may experience more rapid degradation in a fire compared to an alloy with a lower copper content. Manufacturers need to carefully balance the alloy composition to optimize the performance of aluminum materials under both normal and fire conditions.
2. Surface Finishes
2.1 Anodizing
Anodizing is a popular surface treatment for aluminum materials. In a fire, the anodized layer can provide some initial protection by acting as a barrier between the aluminum substrate and the heat source. The thickened oxide layer formed during anodizing can slow down the rate of heat transfer and delay the onset of melting. However, as the temperature continues to rise, the anodized layer may eventually break down, and its protective effect will be diminished. Nevertheless, it can still offer some degree of protection during the early stages of a fire.
2.2 Powder Coating
Powder coating is another common surface finish for aluminum. While powder coating can enhance the appearance and durability of the aluminum under normal conditions, its behavior in a fire can be variable. Some powder coatings may release toxic gases when exposed to high temperatures, posing an additional hazard to occupants in a fire. On the other hand, certain types of powder coatings may have some insulating properties that can help reduce heat transfer to the aluminum substrate for a short period. However, overall, the fire resistance of powder-coated aluminum depends on the specific formulation of the coating.
2.3 Other Finishing Methods and Their Fire-related Characteristics
Other surface finishing methods, such as electroplating and painting, also have their own fire-related characteristics. Electroplated layers may have different melting points and thermal conductivities compared to the aluminum substrate, which can affect the heat transfer and structural integrity of the material in a fire. Painted surfaces may provide a thin layer of protection against heat and flames, but they are generally less effective than anodizing or some powder coatings. The choice of surface finish should take into account both the aesthetic and fire performance requirements of the application.
3. Thickness and Shape of Aluminum Components
3.1 Impact of Thickness on Fire Resistance
The thickness of aluminum components has a direct impact on their fire resistance. Thicker components generally have a greater heat capacity and can absorb more heat before reaching their critical temperature. This means they can withstand the heat of a fire for a longer period compared to thinner components. For example, in a structural application where aluminum beams are used, a thicker beam will take longer to heat up and may maintain its structural integrity for a greater amount of time, providing more time for occupants to evacuate or for fire-fighting efforts to take place.
3.2 Influence of Complex Shapes on Heat Distribution and Deformation
Complex shapes of aluminum components can lead to uneven heat distribution during a fire. Areas with sharp corners or thin sections will heat up more rapidly than thicker or more rounded areas. This uneven heating can cause significant stress within the component, leading to deformation and potential failure. For instance, in a custom-designed aluminum part with intricate geometries, the areas around narrow channels or protruding features may become hot spots, causing the part to warp or crack. Designers need to consider these factors when designing aluminum components for applications where fire resistance is a concern.
Consequences of Aluminum Materials Reacting to Intense Fire
1. Safety Risks in Buildings
1.1 Structural Integrity Threats
In buildings, aluminum is often used in structural elements such as curtain walls and support frames. When these aluminum components are exposed to intense fire, their degradation can pose a serious threat to the overall structural integrity of the building. The weakening of aluminum frames can lead to the collapse of walls or ceilings, endangering the lives of occupants. Even partial failures can cause debris to fall, blocking escape routes and impeding fire-fighting and rescue operations.
1.2 Impact on Occupant Evacuation
The deformation and failure of aluminum components, especially windows and doors, can have a significant impact on occupant evacuation. As mentioned earlier, aluminum casement windows may become inoperable due to thermal expansion or frame deformation, preventing occupants from escaping or allowing fresh air to enter. This can lead to a build-up of smoke and heat, reducing the visibility and increasing the risk of asphyxiation. In addition, the collapse of aluminum structures can block stairwells and corridors, further complicating the evacuation process.
2. Damage to Industrial Equipment and Machinery
2.1 Malfunction of Industrial Machinery
In industrial settings, aluminum is widely used in machinery and equipment. When a fire occurs, the damage to aluminum components can cause the machinery to malfunction. For example, in a manufacturing plant, the aluminum frames of a conveyor system may warp, causing the conveyor belt to misalign or stop moving altogether. This can disrupt the production process and result in significant financial losses due to downtime and potential damage to the products being manufactured.
2.2 Economic Losses
The damage to aluminum materials in a fire can have far-reaching economic consequences. In addition to the direct cost of replacing damaged equipment and components, there are indirect costs such as lost production time, delays in fulfilling orders, and potential damage to the reputation of the company. The cost of repairing or replacing aluminum structures in a building can also be substantial, especially if the fire has caused significant structural damage. Insurance premiums may also increase as a result of the fire, adding to the overall financial burden.
Prevention and Protection Measures
1. Fire-resistant Coatings and Treatments for Aluminum
1.1 Types of Fire-resistant Coatings
There are several types of fire-resistant coatings available for aluminum materials. Intumescent coatings are one of the most commonly used. These coatings expand when exposed to heat, forming a thick insulating layer that can slow down the transfer of heat to the aluminum substrate. Cementitious coatings are another option, which provide a physical barrier against heat and flames. Ceramic coatings can also offer good fire resistance due to their high melting points and low thermal conductivity.
1.2 How They Work to Improve Fire Resistance
Fire-resistant coatings work through various mechanisms to enhance the fire resistance of aluminum materials. Intumescent coatings, for example, contain substances that react when heated to produce gases that cause the coating to expand. This expanded layer acts as an insulator, reducing the heat flux reaching the aluminum. Cementitious coatings rely on their dense structure to block heat and prevent the aluminum from heating up too quickly. Ceramic coatings, with their high-temperature stability, can withstand the heat of a fire for an extended period without degrading, thereby protecting the underlying aluminum.
2. Design Considerations for Fire Safety in Aluminum-based Structures
2.1 Reasonable structural design
When designing aluminum-based structures, it is essential to incorporate fire safety considerations from the outset. This includes using appropriate structural configurations to enhance fire resistance. For example, providing additional bracing or reinforcement in areas where aluminum components are subjected to higher loads can help maintain structural integrity during a fire. Designers should also avoid creating excessive stress concentrations in the structure, as these can lead to premature failure in a fire.
2.2 Fire-separation and Ventilation Design
Proper fire-separation and ventilation design are crucial in buildings and industrial facilities containing aluminum structures. Fire walls and partitions made of non-combustible materials should be installed to prevent the spread of fire between different areas. Adequate ventilation systems can help remove heat and smoke, reducing the risk of fire escalation. In addition, the location and design of vents should be carefully considered to ensure that they do not compromise the fire resistance of the aluminum components or provide a path for the spread of fire.
Conclusion
In conclusion, the behavior of aluminum materials in intense fire is a complex issue that involves multiple factors such as alloy composition, surface finish, and component geometry. Understanding these factors and their effects is essential for predicting the performance of aluminum materials in a fire and taking appropriate preventive and protective measures. The consequences of aluminum materials reacting to fire can be severe, both in terms of safety risks in buildings and damage to industrial equipment. By implementing effective fire-resistant coatings and incorporating fire safety design principles, the risks associated with aluminum materials in a fire can be mitigated. However, continuous research and development are needed to further improve the fire resistance of aluminum materials and ensure their safe use in various applications. Future efforts should focus on developing new alloys and surface treatments that can enhance the fire performance of aluminum while maintaining its other desirable properties. This will contribute to the overall safety and sustainability of buildings and industrial processes where aluminum materials are widely used.